What is Six Sigma?
Discover the essence of Six Sigma methodology, a data-driven approach aimed at enhancing quality and efficiency in business processes. Learn its principles and benefits.
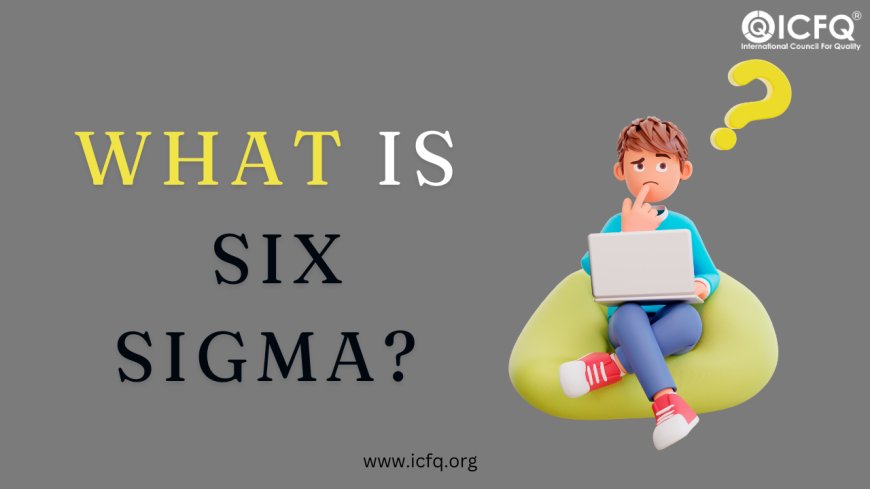
Six Sigma is a system that businesses employ to optimize their processes and manage quality effectively. Its primary goal is to identify and eliminate errors or faults to improve operations and products or services. Originating at Motorola in the 1980s, Six Sigma has since been widely adopted by various industries worldwide. Its development continued through the efforts of companies like General Electric, which popularized its use in the 1990s. The goal of Six Sigma is to reduce variation and maintain consistency in processes, leading to fewer mistakes and higher customer satisfaction. It achieves this by using data-driven approaches and statistical methods to measure and analyze performance, identify problems, and implement solutions. Over time, Six Sigma has evolved into a comprehensive framework that emphasizes continuous improvement and the pursuit of excellence in all aspects of business operations.
Key Principles of Six Sigma
Six Sigma revolves around key principles that guide its implementation:
-
Focus on Customer Satisfaction: Six Sigma puts customers at the center by aiming to deliver products or services that meet or exceed their expectations.
-
Data-Driven Decision-Making: Data is crucial in Six Sigma. It's used to understand how processes are performing, identify areas for improvement, and measure the impact of changes.
-
Process Improvement through Reduction of Variation: Six Sigma aims to reduce variation in processes, making them more consistent and reliable. This leads to fewer errors and higher-quality outcomes.
-
Emphasis on Achieving Measurable Results: Six Sigma sets clear goals and measures progress using quantifiable metrics. This ensures that improvements are tangible and impactful.
-
Leadership Commitment and Involvement: Successful Six Sigma implementation requires commitment and active involvement from leadership. Leaders set the tone, allocate resources, and support employees in driving improvement initiatives.
What are the two main methodologies used in Six Sigma?
DMAIC for Improving Existing Processes
-
Define: This phase focuses on specifying the problem, identifying process boundaries, and setting the project goals. It also involves gathering expectations from stakeholders to align the project outcomes.
-
Measure: Current process performance is quantified by collecting relevant data. This phase establishes a data-driven understanding of defects or issues, providing a benchmark for improvement.
-
Analyze: The goal here is to identify the root causes of defects using statistical tools. This may involve looking at patterns, identifying outliers, and exploring relationships between variables.
-
Improve: Solutions aimed at addressing the root causes are developed and implemented. Techniques such as brainstorming, the design of experiments, and process simulation are typically used.
-
Control: This phase ensures that the improvements are maintained over time. It involves implementing control systems, continuous monitoring, and transitioning management to the process owners.
DMADV for Designing New Processes
-
Define: Goals for the new process are established, focusing on meeting customer needs and business objectives. The definition of success for the project is also clearly stated.
-
Measure: Factors critical to quality and process performance are identified and measured. This might involve using predictive analytics to forecast process outcomes.
-
Analyze: Different process options are explored and analyzed. This often includes using detailed process modeling and criteria to select the most suitable alternative.
-
Design: The chosen design is detailed and optimized. This phase may involve creating prototypes or pilot runs to validate the design under simulated conditions.
-
Verify: The new design is tested to confirm it meets the needs defined earlier. Feedback is used to make necessary adjustments, refining the process to ensure it performs effectively when fully implemented.
Roles and Responsibilities
In Six Sigma projects, several key roles contribute to the effective management and execution of improvement initiatives:
-
Executive Leadership: These are the top-level managers who provide the support and resources necessary for Six Sigma projects. They play a crucial role in fostering a culture that embraces continuous improvement.
-
Champions: Typically middle to senior management, champions set the project goals and priorities. They select projects and ensure that they align with the organization’s strategic objectives.
-
Master Black Belts: These individuals are experts in Six Sigma methodologies. They lead and mentor black belts, helping them understand and apply Six Sigma tools and techniques effectively. Master Black Belts also assist in selecting and scoping projects.
-
Black Belts: Black Belts are responsible for leading improvement projects. They analyze process issues and manage project teams, applying Six Sigma methodologies to solve complex problems.
-
Green Belts: These team members assist with improvement projects. Working under the guidance of Black Belts, Green Belts help collect data, analyze processes, and implement improvements.
-
Yellow Belts: Individuals in this role have a basic understanding of Six Sigma principles. Yellow Belts support project teams by participating in problem-solving tasks and applying basic Six Sigma tools.
Tools and Techniques
Six Sigma projects utilize a variety of tools and techniques to analyze and improve processes. Here’s an overview of some common methods:
-
Process Mapping: This tool involves creating a detailed diagram of a process to visualize its steps and identify areas for improvement. It helps in understanding the flow of materials and information.
-
Cause-and-effect Analysis (Fishbone Diagram): Also known as Ishikawa diagrams, these are used to identify potential causes of a problem. The diagram helps categorize ideas into useful groups.
-
Statistical Analysis: Techniques like hypothesis testing and regression analysis are used to interpret data, identify trends, and make predictions. These methods help in understanding relationships between variables and validating improvements.
-
Control Charts: These charts are used to monitor process performance over time. They help determine if a process is in control or if deviations are due to random variations or a specific cause.
-
Failure Mode and Effects Analysis (FMEA): FMEA is a systematic approach for identifying potential failure modes in a process and their effects on outcomes. It is used to prioritize risks and implement corrective actions.
-
Lean Principles for Waste Reduction: Lean principles focus on eliminating non-value-added activities, thus improving efficiency. Techniques include streamlining workflows and reducing waste in processes.
Finally, the key Six Sigma ideas and methodology are discussed, with a focus on data-driven decision-making, the DMAIC framework, and statistical tools for defect reduction. For those who are attracted by its potential, additional research into Six Sigma promises to improve organizational efficiency and quality through systematic issue-solving and continuous improvement. Consider how to apply these concepts to your initiatives or company, regardless of industry. Embracing Six Sigma methodology provides an opportunity to streamline operations, reduce variance, and ultimately increase customer satisfaction.