What is Six Sigma and How Does It Work?
Learn about Six Sigma, a methodology for improving business processes by minimizing defects and variations, and enhancing efficiency.
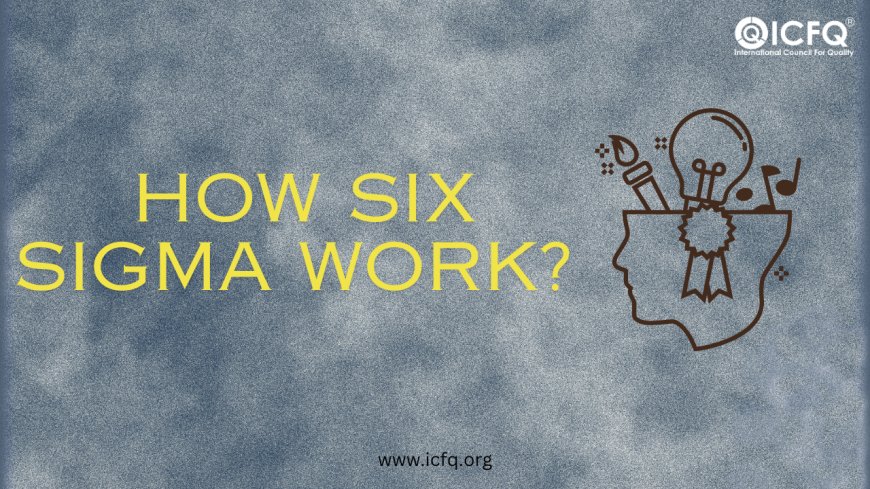
Quality management plays a crucial role in ensuring that businesses consistently deliver products or services that meet or exceed customer expectations. By implementing quality control measures throughout the production or service delivery process, businesses can enhance customer satisfaction, reduce costs associated with defects, and improve brand reputation.
Six Sigma offers a structured approach to quality management by focusing on minimizing variation and defects within processes. Using tools like DMAIC (Define, Measure, Analyze, Improve, and Control), Six Sigma helps organizations identify and address the root causes of problems, leading to enhanced efficiency and higher-quality outcomes. Embracing Six Sigma enables businesses to achieve greater consistency in their operations, driving continuous improvement and ensuring long-term success.
Understanding Six Sigma
Six Sigma is a methodology for process improvement that originated in the manufacturing industry, particularly at Motorola in the 1980s. It has since been widely adopted across various sectors, including healthcare, finance, and service industries. It aims to enhance the quality of outputs by systematically identifying and eliminating defects or errors in processes.
In Six Sigma, "sigma" represents the standard deviation from the mean in a statistical distribution. It quantifies the level of variation within a process, with higher sigma indicating less variability and higher quality. The significance of sigma lies in its role as a measure of process performance, guiding efforts to reduce defects and improve efficiency.
The primary goals of Six Sigma include:
-
Reducing defects: By minimizing variation and standardizing processes, Six Sigma aims to decrease the occurrence of defects or errors significantly.
-
Decreasing variation: Six Sigma seeks to narrow the range of variation within processes, ensuring consistent and predictable outcomes.
-
Improving processes: Through rigorous analysis and optimization, Six Sigma endeavors to enhance the overall efficiency and effectiveness of organizational processes.
Key Principles of Six Sigma
DMAIC is a structured problem-solving methodology used in Six Sigma to improve processes systematically. It consists of five phases:
-
Define: In this phase, the project goals, scope, and deliverables are clearly defined. Stakeholders' requirements are identified to ensure alignment with customer needs.
-
Measure: This phase involves gathering data related to the process to establish a baseline performance. Key metrics are defined, and measurements are taken to quantify the current state of the process.
-
Analyze: In this phase, the collected data is analyzed to identify the root causes of issues or variations within the process. Tools like cause-and-effect diagrams and statistical analysis are often used to pinpoint areas for improvement.
-
Improve: Once the root causes are identified, solutions are developed and implemented to address them. This phase focuses on making changes to the process to achieve the desired improvement goals.
-
Control: The final phase ensures that the improvements made are sustained over time. Control measures and monitoring systems are established to track performance and prevent regression to previous states.
Roles in Six Sigma
Each role in Six Sigma contributes to the success of projects by leveraging their unique skills and expertise to drive continuous improvement within the organization. In Six Sigma projects, various individuals play distinct roles:
-
Champions: These are senior leaders within the organization who sponsor and support Six Sigma initiatives. Their responsibilities include aligning projects with strategic goals, allocating resources, and removing obstacles. Champions need strong leadership skills, strategic thinking, and the ability to drive organizational change.
-
Black Belts: Black Belts are full-time project leaders responsible for executing Six Sigma projects. They possess in-depth knowledge of Six Sigma methodologies and statistical analysis techniques. Black Belts lead project teams, analyze data, identify improvement opportunities, and implement solutions. Strong analytical skills, project management capabilities, and the ability to communicate effectively are essential for Black Belts.
-
Green Belts: Green Belts are team members who work part-time on Six Sigma projects while maintaining their regular job responsibilities. They assist Black Belts in data collection, analysis, and implementation of improvement strategies. Green Belts require basic knowledge of Six Sigma tools and techniques, as well as good teamwork and problem-solving skills.
Tools and Techniques in Six Sigma
Some tools are applied throughout the DMAIC (Define, Measure, Analyze, Improve, Control) process to identify and solve problems systematically. For instance, Pareto charts and Fishbone diagrams are often used in the Analyze phase to identify root causes of issues, while SPC is utilized in the Control phase to monitor process stability and ensure that improvements are sustained. By leveraging these tools, Six Sigma teams can make data-driven decisions and implement targeted solutions to achieve their project goals.
Common tools and techniques in Six Sigma projects include:
-
Pareto charts: These charts help identify the most significant factors contributing to a problem by displaying data in descending order of frequency or impact. This allows teams to prioritize areas for improvement effectively.
-
Fishbone diagrams (Ishikawa diagrams): Fishbone diagrams visually represent possible causes of a problem, categorized into different branches stemming from a central line representing the problem. This tool helps teams systematically identify root causes and brainstorm potential solutions.
-
Statistical Process Control (SPC): SPC involves using statistical methods to monitor and control processes. Control charts, a key component of SPC, track process performance over time and detect any trends or variations that may indicate a need for intervention.
Implementing Six Sigma offers several benefits
-
Cost Reduction: By minimizing defects and errors, Six Sigma helps organizations save costs associated with rework, scrap, and warranty claims. This leads to improved profitability and financial stability.
-
Process Improvement: Six Sigma methodologies focus on optimizing processes to increase efficiency and effectiveness. This results in streamlined operations, reduced cycle times, and improved resource utilization.
-
Customer Satisfaction: By delivering products or services that consistently meet or exceed customer expectations, Six Sigma enhances customer satisfaction and loyalty. This can lead to increased market share and a positive brand reputation.
-
Employee Engagement: Six Sigma empowers employees by involving them in problem-solving and decision-making processes. This fosters a culture of continuous improvement, boosts morale, and encourages innovation among teams.
-
Strategic Alignment: Six Sigma projects are aligned with organizational goals and priorities, ensuring that improvement efforts contribute to overall strategic objectives. This helps drive organizational growth and competitiveness in the marketplace.
Difficulties and Criticisms of Six Sigma
During Six Sigma implementation, challenges such as resistance to change among employees and a lack of management support can hinder progress. Resistance may stem from unfamiliarity with new methodologies, while insufficient backing from leadership can impede project success. Additionally, inadequate training on Six Sigma principles and tools may limit the effectiveness of improvement initiatives.
Critics argue that Six Sigma's focus on metrics may overlook qualitative aspects of processes. Moreover, bureaucratic tendencies, including excessive documentation and rigid methodologies, can slow decision-making and hinder organizational agility. Addressing these concerns requires fostering a culture of adaptability and continuous learning, ensuring alignment of Six Sigma efforts with strategic objectives, and maintaining flexibility in implementation approaches.
we explored the key principles, benefits, challenges, and criticisms of Six Sigma. We highlighted its role in enhancing quality, reducing costs, and increasing customer satisfaction. Six Sigma offers a structured approach to process improvement, addressing issues like resistance to change and bureaucratic tendencies. Its emphasis on data-driven decision-making and continuous improvement fosters organizational excellence. Considering the significant advantages it brings, organizations are encouraged to explore Six Sigma implementation to drive efficiency and achieve operational excellence, ultimately leading to sustainable growth and success.