Top Six Sigma Tools for Better Processes
Boost efficiency with key Six Sigma tools for better processes. Learn essential methods and techniques for success
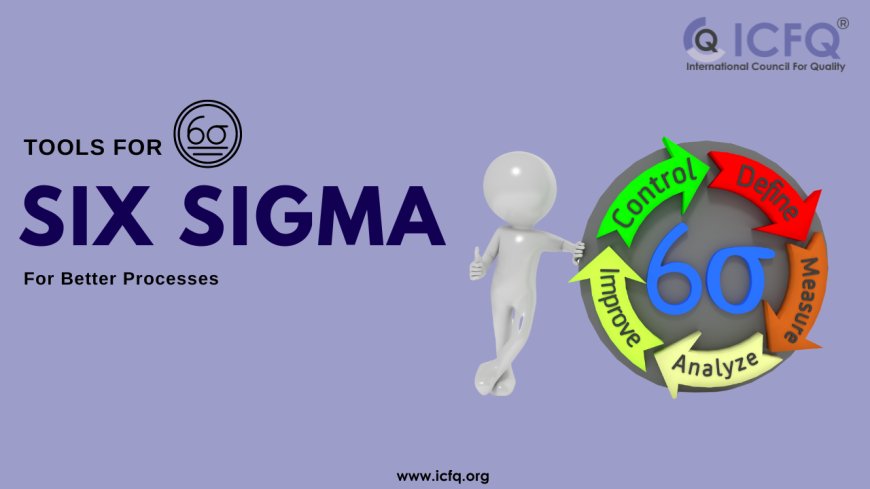
Six Sigma is a methodology designed to improve business processes and enhance quality management. Its main focus is on reducing defects and variability in processes, leading to more consistent and efficient operations. Using a data-driven approach, Six Sigma helps organizations identify the root causes of problems and implement effective solutions.
Six Sigma employs various tools and techniques to analyze and improve processes. Control charts monitor process stability over time, while FMEA (Failure Modes and Effects Analysis) identifies potential failures and prioritizes issues based on risk. Root cause analysis digs into the underlying causes of defects to ensure that solutions are effectively targeted. By using these tools, Six Sigma enables businesses to streamline processes, reduce costs, and improve overall quality. This approach to quality management can lead to higher customer satisfaction and better operational performance.
Iterative Nature and Tool Integration in Six Sigma
The iterative nature of Six Sigma underscores its effectiveness in continuous improvement without exaggerating its impact. It's not a one-time fix, but rather a cyclical process where various tools are integrated at different stages to drive ongoing improvement. From defining project scopes using tools like SIPOC diagrams and project charters, to measuring performance with process mapping and MSA, and analyzing root causes with methods like 5 Whys and fishbone diagrams, every step relies on a diverse toolkit. Pareto analysis and regression analysis further guide decision-making, while tools like brainstorming and FMEA aid in generating and prioritizing solutions. The process culminates in the control phase, where control charts, SOPs, and control plans ensure sustained improvements. This iterative approach ensures that organizations continuously adapt and refine their processes to achieve higher levels of efficiency and quality over time.
What are the top Six Sigma tools for better processes?
Six Sigma uses specific tools to improve business processes by analyzing, measuring, and controlling various elements. These tools help organizations identify problems, find their causes, and implement effective solutions.
Define Phase Tools
-
SIPOC Diagram: A SIPOC diagram, which stands for Suppliers, Inputs, Process, Outputs, and Customers, is a helpful tool used in Six Sigma projects. It helps teams understand the different parts of a process. By showing where things come from (suppliers), what goes into the process (inputs), how the process works, what comes out (outputs), and who receives the end product (customers), the SIPOC diagram gives a basic idea of what the project involves before getting into the details.
-
Project Charter: In the Define phase of a Six Sigma project, a project charter is like a map. It lays out the project's goals, what needs to be done, and who is responsible for what. This document makes sure everyone knows what they're supposed to do and why. It keeps the team on track by outlining the project's purpose, objectives, timeline, and resources, like a plan for success that everyone can follow.
Measure Phase Tools
-
Process Mapping: Process mapping is like drawing a picture of how things get done in a business. It shows all the steps in a process from start to finish. By seeing the process visually, it's easier to spot where things might be going wrong or where things could be done better. Process maps help teams understand how workflows and find ways to make them smoother and more efficient.
-
Measurement System Analysis (MSA): Measurement System Analysis (MSA) is like checking the accuracy of a ruler before measuring something. It makes sure that the tools and methods used to collect data are reliable and give the right information. By doing this, MSA ensures that decisions made based on the data are trustworthy and accurate.
-
Data Collection Plan: A data collection plan is like making a shopping list before going to the store. It's a plan for gathering the information needed for a project. It outlines what data is needed, how it will be collected, and who will collect it. Having a clear plan helps make sure that the right information is gathered efficiently and accurately.
Analyze Phase Tools
-
Root Cause Analysis (5 Whys and Fishbone Diagram): Root cause analysis methods, such as the 5 Whys and fishbone diagram, are crucial for understanding problems deeply without exaggeration. The 5 Whys technique involves repeatedly asking "why" to uncover the root cause behind issues, resembling peeling layers of an onion. Meanwhile, the fishbone diagram visually organizes potential causes of a problem, making it easier to comprehend.
-
Pareto Analysis: Pareto charts play a vital role in prioritizing issues without overstating their importance. Following the 80/20 rule, where 80% of problems often stem from 20% of cases, it ensures efforts are focused on the most impactful areas efficiently.
-
Regression Analysis: Regression analysis aids in understanding relationships between variables straightforwardly. Without using exaggerated claims, it predicts future trends and helps comprehend how changes in one factor may influence another.
Improve Phase Tools
-
Brainstorming and Affinity Diagrams: Brainstorming and affinity diagrams are helpful tools for generating and organizing ideas simply. Brainstorming encourages team members to share their thoughts freely, sparking creativity. Affinity diagrams then group these ideas into categories, making it easier to identify potential solutions and prioritize them effectively.
-
FMEA (Failure Modes and Effects Analysis): FMEA, or Failure Modes and Effects Analysis, is a useful tool for anticipating and addressing potential failures in processes. It systematically identifies potential failure modes, evaluates their effects, and prioritizes them based on their severity, occurrence, and detectability. By doing so, it helps reduce risks and improve process reliability.
-
Design of Experiments (DOE): DOE, or Design of Experiments, is a methodical approach to testing and optimizing process changes. It involves planning and conducting experiments to understand how different factors affect outcomes. By varying these factors systematically, DOE helps identify the best combination for achieving desired results efficiently.
Control Phase Tools
-
Control Charts: Control charts are simple tools that help monitor process performance without using exaggerated claims. They track data points over time, showing if a process is stable or if there are any changes. Control charts help maintain consistency and stability in processes by ensuring things run smoothly over time.
-
Standard Operating Procedures (SOPs): Standard Operating Procedures (SOPs) play a crucial role in maintaining successful process improvements without overstating their importance. They are like instruction manuals that detail the steps needed to perform tasks consistently and effectively. By standardizing procedures, SOPs ensure that everyone follows the same guidelines, reducing errors and ensuring quality.
-
Control Plans: Control plans document the measures needed to sustain improvements and straightforwardly prevent regression. They outline the steps to maintain the changes made during process improvement projects. By doing this, control plans ensure that improvements are sustained over time and that processes continue to perform at their best without exaggeration.
Hurdles in Adopting Six Sigma Tools
While Six Sigma tools offer significant advantages in improving business processes and quality management, many organizations find it challenging to select and apply the appropriate tools. This difficulty can stem from a lack of expertise, insufficient training, or the complexity of the tools themselves.
For instance, understanding when to use control charts versus FMEA can be confusing for teams new to Six Sigma. Additionally, conducting a thorough root cause analysis requires a deep dive into process data, which may not be straightforward without the right skills and experience. Consequently, companies may not fully realize the potential improvements Six Sigma can bring. Addressing these challenges involves investing in training, developing in-house expertise, and gradually integrating Six Sigma tools to build confidence and capability within the organization
The top Six Sigma tools play a vital role in enhancing business processes by identifying areas for improvement and ensuring quality management without exaggerating their significance. From tools like control charts and root cause analysis to Pareto analysis and regression analysis, each tool serves a specific purpose in streamlining operations and driving efficiency. Organizations need to explore and implement these tools effectively to achieve better process performance and quality management. By doing so, they can optimize their operations and deliver higher value to customers while ensuring long-term success.