Fixing Problems Made Simple: Six Sigma Basics
Discover the fundamentals of Six Sigma for streamlined problem-solving. Learn how to improve processes and enhance efficiency effortlessly.
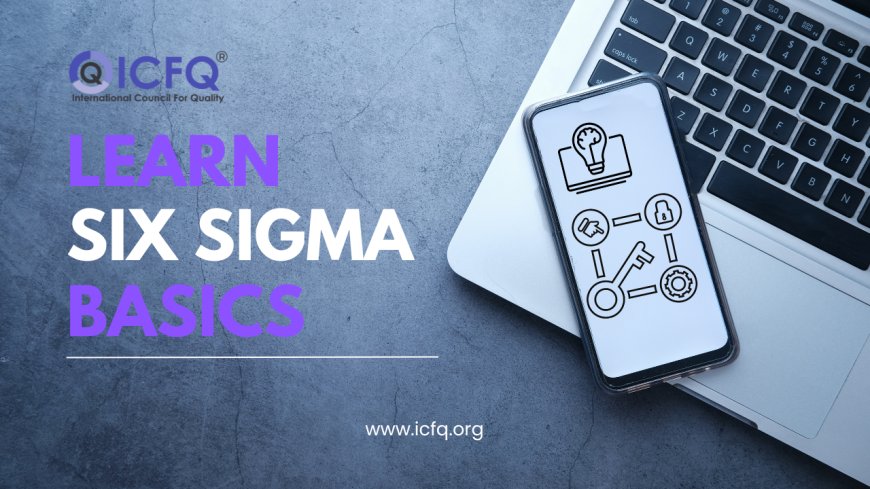
Six Sigma is a disciplined, data-driven approach and methodology for eliminating defects (driving towards six standard deviations between the mean and the nearest specification limit) in any process, from manufacturing to transactional and from product to service. It was developed by Motorola in the 1980s and later popularized by companies like General Electric.
At its core, Six Sigma seeks to improve the quality of process outputs by identifying and removing the causes of defects and minimizing variability in manufacturing and business processes. The term "Six Sigma" refers to the statistical concept of standard deviation, which measures how much variation or dispersion exists from the average.
The key principles of Six Sigma include:
-
Focus on Customer Needs: Six Sigma places a strong emphasis on understanding and meeting customer requirements and expectations.
-
Data-Driven Decision Making: Decisions in Six Sigma are based on the analysis of factual data rather than assumptions or guesswork.
-
Process Improvement: Six Sigma aims to improve processes continuously to achieve higher levels of performance and efficiency.
-
DMAIC Methodology: DMAIC stands for Define, Measure, Analyze, Improve, and Control. It is the structured approach used in Six Sigma projects for problem-solving and process improvement.
-
Cross-Functional Teams: Six Sigma projects typically involve teams comprising individuals from different departments or areas of expertise to ensure a comprehensive approach to problem-solving.
Importance of Systematic Problem-Solving in Six Sigma
A structured method for problem-solving and improvement is essential in organizations to ensure effectiveness and efficiency. Without such an approach, addressing issues may lack direction and result in ineffective solutions. A systematic approach provides a clear framework for identifying, analyzing, and resolving problems in an organized manner. By following a step-by-step process, teams can methodically define the problem, gather relevant data, analyze root causes, develop solutions, and implement changes. This systematic method ensures that efforts are focused on addressing root causes rather than just symptoms, leading to more sustainable improvements over time.
Furthermore, a systematic approach enables organizations to track progress, measure outcomes, and make informed decisions based on data and evidence. Organizations can foster a culture of continuous learning and development by consistently implementing structured methodologies such as DMAIC (Define, Measure, Analyze, Improve, and Control). This empowers teams to identify and address challenges effectively, driving ongoing innovation and optimization of processes. Ultimately, embracing a systematic approach to problem-solving and improvement enables organizations to enhance their operations, improve quality, and achieve strategic objectives with greater efficiency.
How can businesses implement Six Sigma methodologies to achieve measurable improvements in quality and efficiency?
Implementing Six Sigma methodologies can lead to measurable improvements in quality and efficiency for businesses. Here's how:
-
Training and Education: Provide comprehensive training and education on Six Sigma principles, tools, and methodologies to employees at all levels of the organization.
-
Leadership Support: Ensure strong leadership support and commitment to Six Sigma initiatives to drive cultural change and foster a mindset of continuous improvement.
-
Project Selection: Carefully select projects aligned with strategic objectives and with the potential for significant impact on quality and efficiency.
-
Define Metrics: Clearly define key performance metrics and objectives for each project to measure progress and success.
-
DMAIC Methodology: Apply the DMAIC (Define, Measure, Analyze, Improve, Control) methodology rigorously to systematically identify, analyze, and improve processes.
-
Data-Driven Decision Making: Encourage data-driven decision-making by collecting, analyzing, and interpreting relevant data to identify root causes and inform improvement efforts.
-
Cross-functional collaboration: Foster collaboration and communication across departments and functions to ensure a holistic approach to problem-solving and improvement.
-
Continuous Monitoring: Implement systems for continuous monitoring and control to sustain improvements and prevent regression.
-
Employee Involvement: Engage employees at all levels in Six Sigma projects, encouraging ownership, participation, and contribution to improvement efforts.
-
Celebrate Success: Recognize and celebrate successes achieved through Six Sigma initiatives to reinforce the importance of quality and efficiency throughout the organization.
Applying Six Sigma Tools for Root Cause Analysis
Using Six Sigma tools like process mapping, cause-and-effect analysis, and statistical analysis, the store can identify and address the root causes of the problem. This enables them to implement targeted solutions, such as improving staff training, optimizing inventory management, and streamlining checkout processes, to address the underlying issues and enhance the overall customer experience.
-
Process Mapping: The store creates a process map to visualize the customer journey, from entering the store to making a purchase and receiving assistance. This map helps identify any bottlenecks or inefficiencies in the customer experience.
-
Cause-and-effect Analysis: Using cause-and-effect diagrams, the store examines potential reasons for the decline in customer satisfaction. Factors such as long wait times, product availability issues, and staff training gaps are explored to determine their impact on customer satisfaction.
-
Statistical Analysis: The store collects and analyzes customer feedback data to identify trends and patterns. Statistical methods like regression analysis can help determine which factors have the greatest influence on customer satisfaction and which areas require immediate attention.
Fostering Continuous Improvement
Building a culture of continuous improvement starts with leaders showing commitment and providing resources. Employees need to be engaged by being encouraged to share their ideas and solutions, with their contributions recognized. Clear goals should be set and communicated, while feedback systems should be in place to gather input from all levels of the organization. Regular evaluation of processes is important, focusing on understanding what works and what doesn't. Training programs should be implemented to equip employees with the necessary skills for improvement. It's crucial to approach improvement as an ongoing process, making adjustments based on feedback. Transparency throughout the process helps build trust and keeps everyone informed and involved.
Six Sigma offers clear benefits in simplifying problem-solving and enhancing quality within businesses. Its structured approach helps identify and eliminate defects, leading to improved efficiency and customer satisfaction. By embracing Six Sigma methodologies, businesses can streamline processes, reduce variation, and increase productivity, resulting in cost savings and better resource utilization. Encouraging its adoption is essential for sustainable growth and maintaining a competitive edge, as it fosters a culture of continuous improvement and excellence, enabling organizations to meet customer demands, adapt to market changes, and drive innovation effectively.