The Impact of Six Sigma on Financial Performance
Learn how Six Sigma improves financial performance by reducing costs, increasing efficiency, and enhancing customer satisfaction through better decision-making and process improvements.
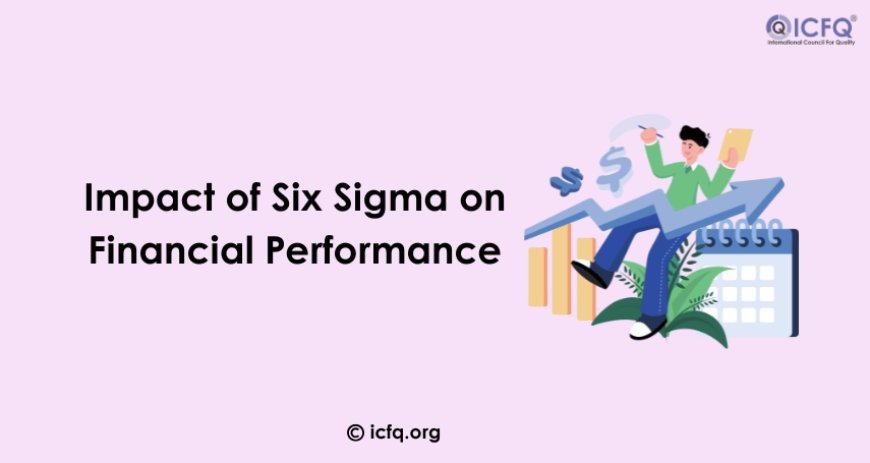
As someone who holds a Six Sigma certification, I’ve seen how powerful this method can be for businesses. It’s not just about improving quality—it’s about saving money, working smarter, and boosting overall performance. We’ll look at how Six Sigma can make a real difference in a company’s financial success.
What Is Six Sigma and Why Does It Matter?
Six Sigma is a data-driven methodology that focuses on reducing variability and eliminating defects in processes. It uses statistical tools and techniques to identify inefficiencies, ensuring that processes consistently produce high-quality results.
The term “Six Sigma” refers to a process that operates with a defect rate of less than 3.4 defects per million opportunities (DPMO). By reaching this level of precision, organizations can avoid costly errors, rework, and customer dissatisfaction.
Cost Reduction Through Process Improvement
-
Core of Six Sigma: Focuses on process improvement to eliminate inefficiencies and reduce waste across various industries, including manufacturing, customer service, and logistics.
-
Real-World Example: A company manufacturing electronic components may face recurring defects in the assembly line, leading to costly product returns, warranty claims, and damage to the brand.
-
Six Sigma Tools: Using tools like root cause analysis and control charts, the company can identify the cause of defects and implement solutions.
-
Financial Impact: By reducing defects, the company saves significant amounts of money annually, improving its overall financial health.
-
Direct Benefits: Fewer defects mean lower costs for returns, repairs, and reputational damage, directly boosting the company's profitability.
Increased Productivity and Operational Efficiency
Six Sigma significantly enhances productivity by optimizing processes and reducing inefficiencies. By streamlining workflows, businesses can improve resource allocation, increase turnaround times, and boost overall operational efficiency.
-
Process Optimization: Streamlines workflows by eliminating non-value-added activities, leading to faster execution and better resource use.
-
Improved Efficiency: Identifies bottlenecks in operations and resolves them, increasing throughput and reducing delays.
-
Real-World Impact: In industries like healthcare or finance, Six Sigma reduces waiting times and errors, leading to better service quality.
-
DMAIC Framework: Uses the DMAIC methodology (Define, Measure, Analyze, Improve, Control) to target and eliminate inefficiencies in processes.
-
Revenue Growth: More efficient operations allow businesses to serve more customers, launch products quicker, and respond to market demands faster.
Boosting Customer Satisfaction and Retention
Six Sigma not only helps businesses reduce costs but also plays a crucial role in boosting customer satisfaction and retention. Ensuring consistent quality and meeting customer expectations helps businesses deliver excellent experiences that keep customers coming back.
-
Consistent Quality: Six Sigma ensures that products and services consistently meet or exceed customer expectations, leading to higher satisfaction.
-
Customer Loyalty: Satisfied customers are more likely to make repeat purchases, refer others, and stay loyal to the brand.
-
Avoiding Negative Impact: Prevents issues that could lead to poor reviews, customer dissatisfaction, and reputational damage.
-
Long-Term Success: Embedding quality at every stage helps businesses build trust and strengthen relationships with customers, leading to sustained growth.
-
Financial Benefits: Retaining loyal customers and delivering a great experience directly contribute to long-term profitability and a stronger market position.
Data-Driven Decision Making
Six Sigma empowers companies to make decisions based on reliable, measurable data, reducing the reliance on assumptions or intuition. By using statistical analysis and real metrics, businesses can identify issues, test solutions, and measure the effectiveness of their decisions, leading to smarter, more informed choices.
-
Data-Driven Culture: Encourages the use of statistical analysis and reliable data to guide decision-making and process improvements.
-
Reduced Risk: Minimizes the chances of making poor business decisions, leading to more successful project outcomes.
-
Informed Decision-Making: Teams rely on concrete metrics rather than assumptions, ensuring smarter business choices.
-
Cost Savings: Fewer missteps result in reduced costs and more efficient use of resources.
-
Improved Financial Performance: By making better decisions, businesses can optimize operations, improve results, and achieve stronger financial outcomes
Real-World Success Stories of Six Sigma
Many Fortune 500 companies credit Six Sigma with delivering significant financial benefits. General Electric, for example, saved over $10 billion during the first five years of adopting Six Sigma. Companies like Honeywell, 3M, and Samsung have also implemented Six Sigma strategies to boost their bottom line.
These aren’t just one-off success stories. Organizations that commit to Six Sigma often see long-term gains in revenue, efficiency, and customer loyalty. Whether it’s through reducing cycle time, minimizing scrap rates, or improving service delivery, the financial impact is undeniable.
How to Get Started with Six Sigma
If you're ready to reap the financial benefits of Six Sigma, the next step is to get started with its implementation. The best approach is to train employees at different certification levels—Yellow Belt for beginners, Green Belt for project-level expertise, and Black Belt for leadership roles.
-
Certification Levels: Start by training your team at various certification levels: Yellow Belt (beginner), Green Belt (project-level), and Black Belt (leadership).
-
Structured Learning: Enroll in programs from recognized bodies like ICFQ, which offer comprehensive courses on Six Sigma principles, tools, and real-world applications.
-
Building Skills: Certification equips your team with the necessary skills to implement Six Sigma effectively, promoting a culture of continuous improvement.
-
Start Small: Begin with a few pilot projects to test Six Sigma methods, gather data, and showcase tangible results.
-
Expand for Impact: Once you demonstrate success, gradually expand Six Sigma practices across the organization to maximize financial benefits and long-term improvements.
Six Sigma is much more than a quality improvement methodology. It’s a strategic tool that can deliver measurable financial performance across all areas of a business. From cutting costs and improving productivity to increasing customer retention and enabling better decisions, Six Sigma helps organizations become more agile, efficient, and profitable. In a world where every dollar counts, investing in Six Sigma can be the smartest financial move your company makes.