Six Sigma Tips for Quality Management
Learn key Six Sigma tips for effective quality management. Enhance processes, minimize defects, and increase efficiency with proven strategies and tools.
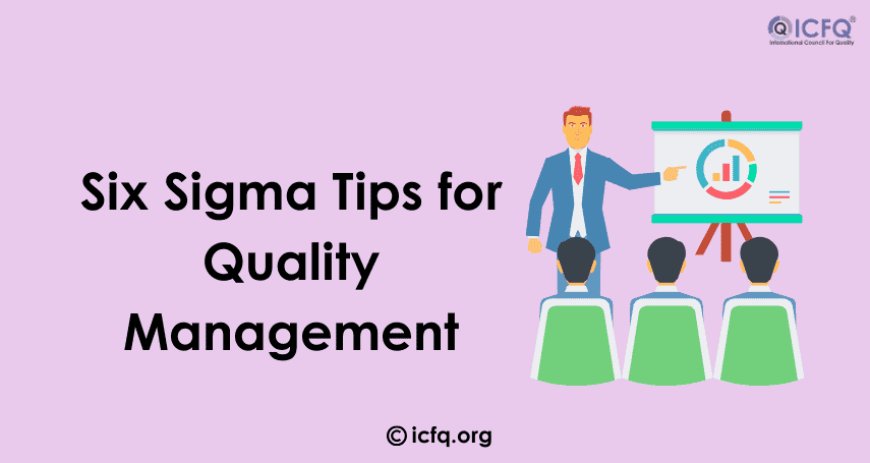
As an expert in quality management, I highly recommend adopting Six Sigma for quality management to drive meaningful improvements within your organization. This proven methodology focuses on reducing defects, streamlining processes, and enhancing operational efficiency. By leveraging data-driven approaches, Six Sigma allows organizations to identify root causes of inefficiencies and implement corrective actions that lead to better quality products and services.
By following the structured DMAIC framework (Define, Measure, Analyze, Improve, Control), businesses can continuously monitor performance, optimize processes, and ensure consistent quality. Implementing Six Sigma not only reduces waste but also fosters a culture of continuous improvement, ultimately delivering greater value to customers.
Understand the Six Sigma Methodology
Before implementing Six Sigma, it's essential to grasp the core principles that drive this methodology. Six Sigma aims to minimize process defects to such an extent that the probability of failure becomes negligible. Its ultimate goal is to reach a defect rate of just 3.4 per million opportunities, which is considered a near-perfect standard of quality and performance. This precision ensures that processes are highly efficient, reliable, and capable of delivering consistent results with minimal errors.
The methodology follows a structured framework called DMAIC, which stands for:
-
Define: Clearly outline the problem, scope, and objectives of the improvement project.
-
Measure: Collect relevant data to understand the current process performance.
-
Analyze: Identify the root causes of defects and inefficiencies.
-
Improve: Implement solutions to address the root causes and enhance process performance.
-
Control: Monitor and control the process to maintain improvements and ensure sustainability.
By adhering to this structured approach, Six Sigma helps businesses streamline their processes and significantly reduce defects and waste. The framework’s focus on data and measurement ensures that improvements are based on facts rather than assumptions.
Train Your Team on Six Sigma Concepts
For Six Sigma to succeed in your organization, your team must be properly trained in the methodology. The level of training should match the roles employees will play in the improvement process:
-
Six Sigma Yellow Belt: This is the introductory level, providing employees with an understanding of the basic concepts of Six Sigma and how it contributes to improving process quality.
-
Six Sigma Green Belt: Employees at this level typically work on process improvement projects and assist Black Belts with data collection and analysis.
-
Six Sigma Black Belt: These professionals are experts in Six Sigma and are responsible for leading large-scale projects, analyzing data, and making high-level decisions.
-
Six Sigma Master Black Belt: The highest level of certification, Master Black Belts mentor other belts and oversees the execution of complex Six Sigma projects across the organization.
Training ensures that your team members can confidently apply Six Sigma tools and techniques to improve processes and achieve meaningful results. It also fosters a culture of quality improvement throughout the organization.
Make Data-Driven Decisions
One of the cornerstones of Six Sigma for quality management is the emphasis on data-driven decision-making. Rather than relying on intuition or guesswork, Six Sigma requires that you gather and analyze data to guide improvements. Data provides insights into where defects are occurring, how often, and why.
Here are some key steps for using data to improve quality management:
-
Data Collection: Ensure that you are gathering accurate, relevant data on your processes. This might include tracking defect rates, process times, or customer feedback.
-
Statistical Tools: Utilize statistical tools, such as Pareto analysis, control charts, and scatter plots, to analyze trends and identify areas that require improvement.
-
Root Cause Analysis: Use data to uncover the underlying causes of defects or inefficiencies. This is a crucial part of the analysis phase in the DMAIC process.
By making decisions based on data, your organization will be able to identify issues early, reduce waste, and implement targeted improvements. This approach not only improves the quality of your products or services but also optimizes operational efficiency.
Implement Continuous Improvement Practices
A key principle of Six Sigma for quality management is continuous improvement. It’s not enough to make a few improvements and call it a day—Six Sigma encourages organizations to continually refine and optimize processes over time.
Here are some tips to foster a culture of continuous improvement:
-
Regular Process Reviews: Schedule periodic reviews to evaluate the effectiveness of changes and identify new areas for improvement. Use metrics and data analysis to guide these evaluations.
-
Kaizen Approach: Encourage small, incremental changes to improve processes on an ongoing basis. The Kaizen philosophy—meaning "change for the better"—aligns well with Six Sigma's commitment to continuous improvement.
-
Employee involvement: Engage employees in identifying areas for improvement and implementing solutions. They often have valuable insights based on their firsthand experience with the processes.
Continuous improvement ensures that your organization remains adaptable and can proactively address emerging issues. By fostering a mindset of constant refinement, you can maintain high-quality standards and stay competitive in the market.
Create a Culture of Quality
The success of Six Sigma for quality management doesn’t just depend on the tools and methodologies—it also requires a strong culture of quality within your organization. This culture should be embedded across all levels of the company, from leadership to frontline employees.
Here are key strategies for building a culture of quality:
-
Leadership Commitment: Leaders should demonstrate a strong commitment to quality and support Six Sigma initiatives. Their actions and priorities should reflect the importance of continuous quality improvement.
-
Employee Ownership: Encourage employees to take ownership of their role in maintaining and improving quality. Involve them in decision-making and encourage feedback.
-
Recognize Successes: Celebrate achievements and improvements, both big and small. Recognizing the contributions of teams and individuals fosters a sense of accomplishment and motivation.
-
Open Communication: Create an environment where employees feel comfortable sharing their ideas and concerns about quality. Regularly seek feedback and input from the entire team.
A culture of quality motivates employees to consistently focus on maintaining high standards and drives a sense of pride in their work. This cultural foundation supports the effectiveness of Six Sigma initiatives and leads to lasting quality improvements.
Usage of Technology and Tools
In addition to the human elements of Six Sigma, technology can play a significant role in optimizing quality management processes. Modern tools and software solutions can help you collect, analyze, and visualize data more efficiently, speeding up decision-making and improving accuracy.
Here’s how technology can enhance your Six Sigma efforts:
-
Process Mapping Software: Tools like Microsoft Visio or Lucidchart can help you create detailed process maps that visually represent workflows, helping to identify inefficiencies and bottlenecks.
-
Data Analysis Tools: Software like Minitab or SAS provides advanced statistical analysis capabilities, allowing you to perform complex data analysis and hypothesis testing quickly.
-
Project Management Tools: Platforms like Trello, Asana, or Jira help track Six Sigma projects, assign tasks, and monitor progress, ensuring that initiatives stay on schedule and goals are met.
By using technology, you can streamline the implementation of Six Sigma for quality management and ensure that your team has the tools they need to succeed.
Adopting Six Sigma for quality management can significantly enhance your organization’s efficiency and product quality. By focusing on reducing defects, optimizing processes, and fostering a culture of continuous improvement, Six Sigma helps businesses deliver better results with fewer errors.
With the right training, data-driven decision-making, and commitment to quality, your organization can streamline operations and drive lasting improvements. By leveraging technology and engaging employees, Six Sigma can create a foundation for long-term success, ultimately boosting customer satisfaction and business growth.