Tools for Lean Six Sigma: A Complete Guide
A comprehensive guide to Lean Six Sigma tools for enhancing process efficiency, reducing waste, and ensuring long-term improvements in your organization
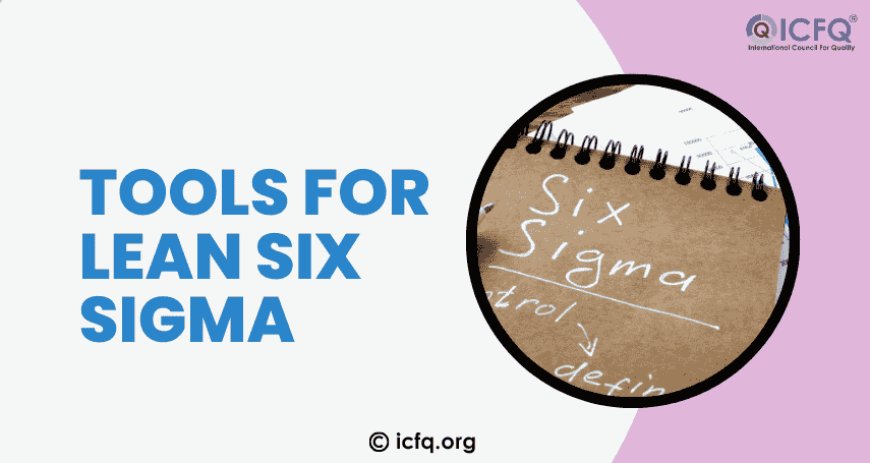
Lean Six Sigma is a methodology widely adopted by businesses to improve operational efficiency, reduce waste, and enhance product quality. By combining the principles of Lean, which focuses on eliminating waste, and Six Sigma, which highlights reducing defects, this approach has helped countless organizations streamline their processes. To effectively implement Lean Six Sigma, it’s crucial to use a set of proven tools throughout the project.
Define Phase: Setting the Foundation for Improvement
The define phase is the first step in the lean Six Sigma process. Here, the team works to clearly understand and define the problem, the project goals, and the customer requirements. This phase is critical because it ensures everyone is on the same page from the start.
Tools used in the define phase:
-
Project Charter: This tool documents the project’s objectives, scope, timeline, and team members. It helps set the boundaries and ensures alignment among stakeholders.
-
SIPOC Diagram: Standing for Suppliers, Inputs, Process, Outputs, and Customers, this diagram offers a high-level view of the process and highlights the key factors that will impact performance.
-
Voice of the Customer (VOC): Understanding the customers' needs is fundamental. VOC tools help gather and prioritize customer feedback to guide improvement efforts.
Measure Phase: Quantifying the Problem
The measurement phase is about collecting data to understand the current state of the process and identify areas of improvement. Data-driven decisions are the core of Lean Six Sigma, and this phase provides the baseline measurements needed to move forward.
Tools used in the Measure phase:
-
Process Mapping: A visual representation of the steps in a process helps identify bottlenecks, inefficiencies, or areas of waste.
-
Pareto Analysis: This tool follows the 80/20 rule, identifying the 20% of issues that cause 80% of the problems. It helps prioritize the most critical issues.
-
Measurement System Analysis (MSA): Verifies that the data collection system is accurate and reliable to ensure high-quality data.
By using these tools, teams can collect precise data that will inform the analysis phase and drive decision-making.
Analysis Phase: Identifying Root Causes
The analysis phase focuses on interpreting the data collected in the measurement phase to identify the root causes of problems. It’s essential to understand the underlying issues before proposing solutions.
Tools used in the analysis phase:
-
Fishbone Diagram: Also known as the Ishikawa or cause-and-effect diagram, this tool visually categorizes the potential causes of a problem, making it easier to identify root causes.
-
5 Whys: This simple technique involves asking “Why?” multiple times (usually five) to drill down into the root cause of an issue.
-
Failure Modes and Effects Analysis (FMEA): FMEA helps evaluate potential failure points in a process, their impact, and likelihood, allowing teams to focus on the most critical areas.
These tools enable teams to gain deeper insights into the problem’s root causes and guide the design of effective solutions.
Improve Phase: Designing Solutions
Once the root causes are understood, the Improve phase focuses on brainstorming, testing, and implementing solutions to enhance process performance.
Tools used in the Improve phase:
-
Brainstorming: Engaging the team in generating a wide range of potential solutions allows for creative problem-solving.
-
Design of Experiments (DOE): DOE is a structured approach to experimenting with different variables to identify the most effective solutions and optimizations.
-
Mistake Proofing (Poka-Yoke): This tool aims to design processes in such a way that errors are automatically prevented, ensuring that mistakes don’t occur in the first place.
With these tools, teams can design and implement effective, data-driven solutions that address the root causes identified in the analysis phase.
Control Phase: Sustaining Improvements
The control phase is about ensuring that the improvements are sustained over time. It’s not enough to simply fix problems in the short term; teams need systems in place to monitor the process and ensure continued success.
Tools used in the control phase:
-
Control Charts: These charts monitor the process over time to detect any deviations or variations that may indicate a decline in performance.
-
Standard Operating Procedures (SOPs): Documenting the newly optimized processes ensures that everyone follows the same standardized procedures, reducing variability.
-
Process Control Plans: These plans outline how the improved process will be regularly monitored and controlled to ensure that improvements are maintained.
By applying these tools, teams can ensure long-term process stability and maintain the improvements achieved.
Statistical Tools: Supporting Data-Driven Decisions
Throughout the Lean Six Sigma process, statistical tools are crucial for making data-driven decisions. These tools help ensure that decisions are based on evidence rather than assumptions.
Key statistical tools in Lean Six Sigma:
-
Sigma Level: Measures process performance, with a higher sigma level indicating fewer defects and a more efficient process.
-
Regression Analysis: Helps identify relationships between variables and predict future outcomes, providing insights into how different factors affect process performance.
-
Normal Distribution: Understanding the variation in a process is key to improving it. The normal distribution model helps visualize and analyze this variation.
These statistical tools provide the mathematical foundation to support Lean Six Sigma decisions, ensuring improvements are grounded in data.
Other Lean Tools: Complementing Six Sigma Techniques
In addition to the core Six Sigma tools, Lean Six Sigma incorporates several other tools that help eliminate waste and improve efficiency. These tools focus on streamlining processes and creating more value with fewer resources.
Additional lean tools:
-
Kaizen: A philosophy of continuous, incremental improvement that involves all employees in the process.
-
Kanban: A visual scheduling system used in just-in-time production to reduce waste and increase efficiency.
-
Value Stream Mapping (VSM): This tool helps identify waste in the value stream, allowing teams to optimize flow and eliminate non-value-added activities.
These Lean tools complement Six Sigma tools by focusing on improving process flow and reducing unnecessary waste.
Lean Six Sigma tools are powerful instruments that help businesses achieve operational excellence. Whether you’re in the Define, Measure, Analyze, Improve, or Control phase, each tool plays a vital role in streamlining processes, enhancing quality, and reducing waste. By leveraging these tools effectively, organizations can drive continuous improvement and maintain long-term success.