Power of DMAIC in Six Sigma: A Guide to Process Improvement
Learn how DMAIC in Six Sigma drives process improvement. Discover how this structured, data-driven approach boosts quality, efficiency, and sustainable results.
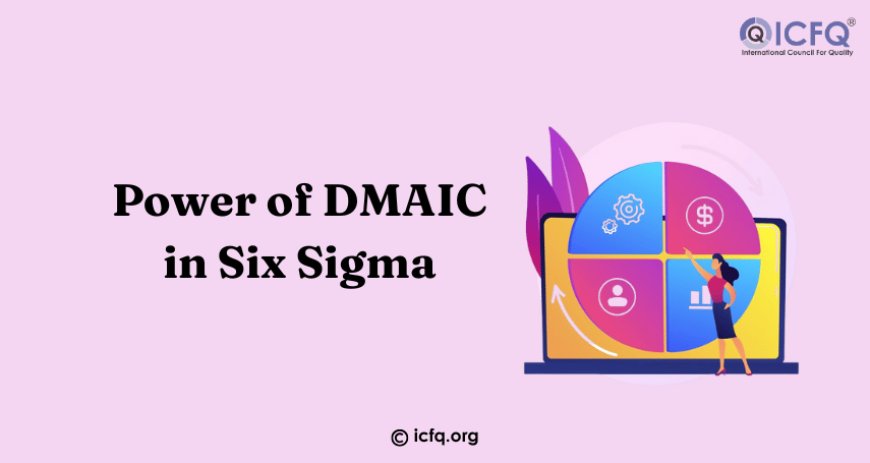
As a holder of Six Sigma Certification, with having hands-on experience, I use the DMAIC framework to systematically improve processes. It involves defining the problem, measuring performance, analyzing data to find root causes, implementing solutions to improve, and controlling the process to ensure sustained results. DMAIC ensures data-driven, repeatable, and effective process optimization.
What is DMAIC in Six Sigma?
DMAIC in Six Sigma is a five-phase approach used in Six Sigma to drive process improvements. The acronym stands for Define, Measure, Analyze, Improve, and Control. These phases guide teams through a structured methodology that allows them to address complex problems in a systematic way, ensuring improvements are not only effective but also sustainable.
Each phase of DMAIC in Six Sigma is data-driven, which means that decisions are made based on facts and measurements rather than assumptions or guesses. DMAIC in Six Sigma helps organizations pinpoint inefficiencies, implement corrective actions, and monitor their progress over time.
Define: Setting the Foundation
The Define phase of DMAIC in Six Sigma is the first step and focuses on laying the groundwork for the project. During this phase, teams define the problem, set clear objectives, and identify the scope of the project.
Key activities in the Define phase include:
-
Project Charter Creation: The project charter is a formal document that outlines the objectives, scope, resources, and timeline of the project.
-
Stakeholder Identification: Understanding who will be affected by the process change is essential to ensure the solution meets their needs.
-
High-Level Process Mapping: Creating a basic process map helps teams visualize the overall process and identify potential bottlenecks or inefficiencies.
-
Defining Critical-to-Quality (CTQ) Metrics: Identifying what factors are crucial for quality ensures that the improvements focus on what matters most to customers and the business.
Measure: Collecting the Right Data
The Measure phase is all about gathering data to understand how the process currently operates. Without data, it is impossible to assess how well the process is performing or to identify areas for improvement. During this phase, teams collect baseline performance data and determine key performance indicators (KPIs) to monitor progress.
Important activities in the Measure phase include:
-
Data Collection: A systematic approach is used to collect relevant data that reflects the performance of the process.
-
Process Flowcharts: Flowcharts are used to map the steps of the process, helping teams identify potential bottlenecks or inefficiencies.
-
Measurement System Analysis (MSA): MSA ensures that the data collected is accurate and reliable.
-
Control Charts: These charts track process performance over time, highlighting any variations that could indicate problems.
Analyze: Discovering Root Causes
The Analyze phase of DMAIC in Six Sigma digs deep into the data collected in the Measure phase to uncover the root causes of inefficiencies or defects. In this phase, teams focus on understanding the underlying issues driving process problems rather than just addressing surface-level symptoms.
Common tools used in the Analyze phase of DMAIC in Six Sigma include:
-
Fishbone Diagrams (Ishikawa): This tool helps visualize the potential causes of a problem, categorizing them into groups like people, process, equipment, and environment.
-
Pareto Charts: Pareto analysis helps identify the most significant factors contributing to the problem, focusing efforts on the vital few rather than the trivial many.
-
Hypothesis Testing: Statistical tests are used to validate or disprove assumptions about what might be causing the problem.
-
Regression Analysis: Regression helps identify relationships between variables, which can reveal patterns or correlations driving inefficiencies.
Improve: Implementing Effective Solutions
In the Improve phase of DMAIC in Six Sigma, teams move from analysis to action. Now that they have identified the root causes of the problem, the next step is to implement solutions that will resolve the issues and improve the process. The Improve phase focuses on developing, testing, and validating solutions.
Key activities in the Improve phase of DMAIC in Six Sigma include:
-
Brainstorming Solutions: The team collaborates to generate potential solutions to the problem. This often involves creative thinking and exploring new approaches.
-
Design of Experiments (DOE): DOE is a structured method for testing the effectiveness of different solutions or process changes.
-
Mistake-Proofing (Poka-Yoke): This technique involves designing the process so that mistakes are either impossible or easily detected before they cause harm.
-
Lean Tools: Lean methodologies, like value stream mapping or waste reduction, are often used in conjunction with Six Sigma to eliminate non-value-added activities.
Control: Sustaining the Gains
The Control phase ensures that the improvements made in the Improve phase of DMAIC in Six Sigma are sustained over time. Even the best solutions can fail without proper monitoring and controls in place to prevent the process from reverting to its old ways.
Key activities in the Control phase include:
-
Standard Operating Procedures (SOPs): SOPs provide clear guidelines for operating the improved process, ensuring consistency and quality.
-
Control Charts: These are used to monitor ongoing process performance and identify any deviations that require attention.
-
Training and Documentation: Proper training ensures that employees understand and can maintain the improved processes.
-
Ongoing Monitoring Plans: Continuous monitoring helps ensure that the process stays on track and that any issues are addressed promptly.
The Control phase is essential for ensuring that the gains made during the Improve phase are sustained and that the process remains efficient and effective in the long term.
How DMAIC in Six Sigma Works
-
Structured Process: DMAIC follows a clear, step-by-step methodology to ensure systematic problem-solving.
-
Data-Driven: Decisions are based on data, ensuring accurate insights and informed choices.
-
Root Cause Focus: DMAIC identifies and addresses root causes, leading to long-term improvements.
-
Repeatable & Scalable: It can be applied across industries and repeated for consistent results.
-
Sustained Results: The Control phase ensures improvements are maintained with ongoing monitoring and standardization.
DMAIC in Six Sigma is more than just a problem-solving tool; it’s a comprehensive methodology that empowers organizations to drive meaningful change and continuous improvement. By following the Define, Measure, Analyze, Improve, and Control phases, businesses can achieve measurable improvements that enhance quality, reduce costs, and increase customer satisfaction.