The Role of Artificial Intelligence in Modern Quality Management
Explore how Artificial Intelligence is revolutionizing modern quality management with smarter analytics, automation, and real-time decision-making tools.
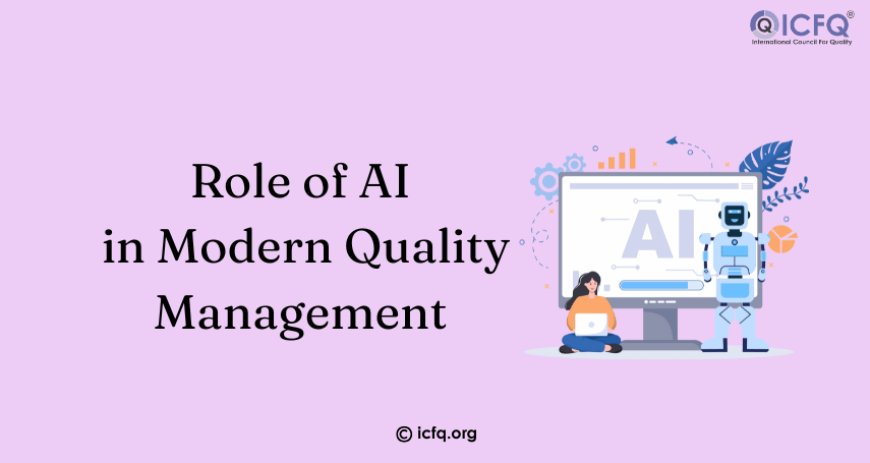
Quality management has always been essential in my work, making sure products and services consistently meet customer expectations. But over the years, I've seen a big shift. It’s no longer just about following rules; it’s about adding real value by keeping customers happy and minimizing risks.
One of the biggest changes? Integrating AI. I used to rely on manual checks and routine processes, but as production scaled up, that just wasn’t enough. AI made a difference by automating data analysis and spotting issues before they turned into problems.
What is Artificial Intelligence and Why It Matters in Quality Management
AI makes machines smart enough to handle tasks like decision-making, data analysis, and problem-solving, just like a human would. In quality management, it’s a powerful tool for spotting issues and predicting problems fast, like having an always-alert assistant by your side.
Why Use AI in Quality Management?
-
Better Data Analysis and Decisions: AI can handle tons of complex data and find patterns that might slip past human eyes.
-
Automatic Monitoring and Maintenance: No need for constant human supervision—AI keeps an eye on things automatically, cutting down on downtime.
-
More Accurate Predictions: Instead of guessing when something might go wrong, AI uses data to predict potential failures, making maintenance proactive rather than reactive.
-
Spotting Mistakes in Real-Time: If something doesn’t look right, AI can catch it right away, helping maintain quality standards.
AI-Powered Data Analytics for Smarter Quality Decisions
One of the coolest things about AI in quality management is its ability to make data-driven decisions faster and more accurately. AI tools sift through massive datasets, spotting patterns that wouldn’t be obvious otherwise. This means businesses can address potential issues before they become major problems.
Real-Life Applications:
-
Finding Defect Trends: Analyzing production data to see if certain defects keep cropping up.
-
Customer Feedback Analysis: Using Natural Language Processing (NLP) to scan customer reviews for hints about quality issues.
-
Predicting Maintenance Needs: Analyzing past maintenance data to figure out when a machine might fail.
-
Improving Supply Chain Quality: AI spots bottlenecks or areas where the process could be more efficient.
Automation and Predictive Maintenance: Transforming Manufacturing
Manufacturing has seen a massive shift with AI-driven automation and predictive maintenance. Instead of doing routine checks that might not catch everything, AI monitors equipment in real-time and predicts when maintenance is needed. This approach not only keeps production running smoothly but also saves time and money.
Key Benefits:
-
Less Manual Inspection: Automated systems catch defects consistently, without human fatigue.
-
Consistent Quality: Automation ensures that every product meets the same high standards.
-
Preventing Breakdowns: AI sensors detect subtle signs of wear before a machine breaks down.
Real-Time Monitoring and Error Detection Using AI
One major advantage of using AI in quality management is real-time monitoring. Instead of waiting until the end of production to find errors, AI systems spot them as they happen. This not only improves product quality but also cuts down on waste—because it’s easier to fix something when it’s caught early.
How Real-Time Monitoring Works:
-
Constant Quality Checks: Automated systems monitor quality continuously, flagging issues right away.
-
Instant Process Adjustments: If a problem is detected, the system can adjust settings to fix it.
-
Fast Problem Alerts: Operators are notified immediately when something’s off, allowing for quick intervention.
Challenges of Implementing AI in Quality Management
While AI sounds great on paper, there are some hurdles to getting it up and running.
-
High Initial Costs: Implementing AI systems can be pricey, especially for smaller companies.
-
Cultural Resistance: People who are used to traditional methods might be hesitant to trust AI-driven solutions.
-
Data Privacy Issues: With AI analyzing so much data, companies need to be extra careful about following privacy regulations.
-
Skill Gaps: Not every team has data scientists on hand, and training can take time.
The Future of Quality Management with Artificial Intelligence
AI will become even more integrated into quality management, making it simpler to use without needing technical expertise. Future systems won’t just predict issues—they’ll also recommend fixes. Plus, AI will help companies cut waste and save energy while maintaining high standards, reshaping how we think about quality management.
Quality certifications boost quality management by proving that a company meets industry standards. They build trust, promote consistency, and support continuous improvement, enhancing overall performance.