Achieving Goals in Six Sigma: A Success Path
Learn how to achieve goals in Six Sigma using structured methods, data analysis, and teamwork to drive quality, efficiency, and long-term success.
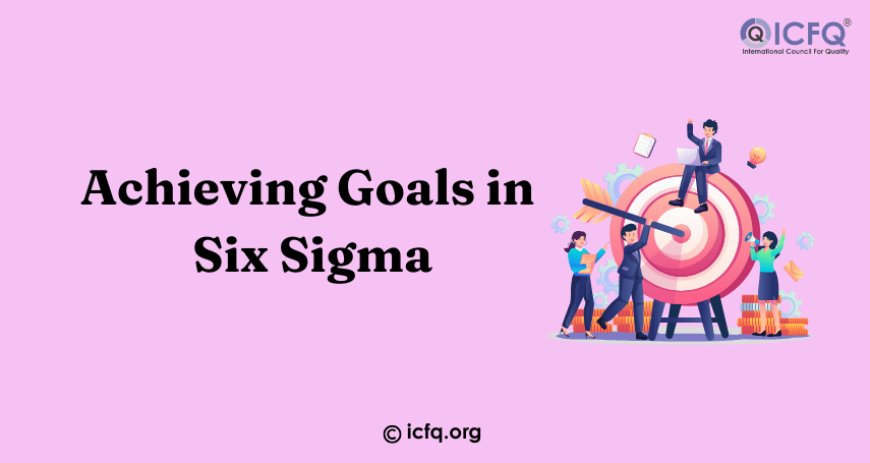
In my journey with Six Sigma, I’ve learned that achieving goals isn’t just about using tools—it’s about clarity, collaboration, and consistency. One of my earliest projects involved reducing defects on a production line. By aligning the team with SMART goals and using data to drive decisions, we not only met our targets but also sustained the improvements. Achieving goals in Six Sigma has shown me that success comes from structured effort and a problem-solving mindset. But achieving goals in Six Sigma isn’t about shortcuts—it’s about following a well-defined path to success.
Understanding the Core Principles of Six Sigma
To begin your Six Sigma journey, it’s essential to understand the philosophy behind it. Six Sigma is a methodology focused on improving quality by minimizing variation and defects. These core principles are the foundation for achieving goals in Six Sigma effectively.
Key principles that define Six Sigma:
-
Customer focus: Every improvement must meet or exceed customer expectations.
-
Data-driven decisions: Success is based on facts, not assumptions.
-
Process orientation: Understand and improve processes, not just outcomes.
-
Continuous improvement: Always strive to do better, even when things seem to be working.
-
Team collaboration: Involvement at all levels leads to more effective results.
Setting SMART Goals Aligned with Six Sigma Methodology
One of the first steps in achieving goals in Six Sigma is setting clear, actionable objectives. SMART goals—Specific, Measurable, Achievable, Relevant, and Time-bound—ensure that Six Sigma projects are strategically aligned and results-driven.
What SMART goals look like in Six Sigma:
-
Specific: Define exactly what you want to achieve (e.g., reduce defect rate in product A).
-
Measurable: Use quantifiable metrics (e.g., reduce cycle time by 20%).
-
Achievable: Ensure goals are realistic given time and resources.
-
Relevant: Align with organizational priorities and customer needs.
-
Time-bound: Set clear deadlines to maintain momentum.
By setting SMART goals, you're laying a solid foundation for achieving goals in Six Sigma that are both impactful and sustainable.
The Role of Data in Driving Success
Six Sigma thrives on data. Every decision, improvement, and solution in the Six Sigma methodology is backed by data analysis. That’s why achieving goals in Six Sigma requires a disciplined approach to measuring and interpreting key performance indicators.
How data drives Six Sigma success:
-
Measure phase: Collect data to understand current performance.
-
Analyze phase: Identify root causes using tools like Pareto charts and histograms.
-
Improve phase: Use data to test and validate solutions.
-
Control phase: Monitor results to ensure lasting success. Without data, Six Sigma cannot function, and achieving goals in Six Sigma becomes guesswork instead of science.
Identifying and Eliminating Process Variations
Variation is one of the primary causes of inefficiency and poor quality. Six Sigma equips professionals with the tools to detect and minimize these variations, making a huge difference in achieving goals in Six Sigma projects.
Six Sigma tools to reduce variation:
-
Statistical Process Control (SPC): Monitor process performance over time.
-
Fishbone Diagrams: Diagnose root causes of inconsistency.
-
FMEA (Failure Modes and Effects Analysis): Predict and prevent failures.
-
Standardization: Implement consistent procedures for reliability.
Reducing process variation means greater efficiency, better results, and smoother progress toward your Six Sigma goals.
Importance of Teamwork and Leadership in Six Sigma Projects
No project in Six Sigma succeeds alone. Team collaboration and leadership are essential for driving Six Sigma initiatives forward. Together, they create the momentum and structure necessary for achieving goals in Six Sigma across all departments.
Key elements of Six Sigma teamwork:
-
Clear roles: From Yellow Belt to Master Black Belt, everyone plays a part.
-
Cross-functional involvement: Diversity in skills leads to better outcomes.
-
Strong leadership: Leaders ensure projects stay aligned and resourced.
-
Effective communication: Keeps the team informed, engaged, and motivated. Great results in Six Sigma come from great teams—empowered by vision, direction, and purpose.
Measuring Progress with Key Performance Indicators (KPIs)
Progress in Six Sigma isn’t just observed—it’s measured. KPIs (Key Performance Indicators) are used throughout projects to ensure improvements are taking place and goals are being met. They are critical to achieving goals in Six Sigma with clarity and confidence.
Common KPIs include:
-
Defect rate: Tracks reduction in product or service errors.
-
Cycle time: Measures how long a process takes from start to finish.
-
Cost savings: Evaluates the financial impact of improvements.
-
Customer satisfaction: Gauges the customer’s response to changes.
Sustaining Improvements for Long-Term Success
Success in Six Sigma doesn’t stop at implementation. Sustaining the results is key to long-term value, which is a crucial part of achieving goals in Six Sigma for the future, not just the present.
Ways to maintain improvements:
-
Control charts: Monitor performance metrics over time.
-
Process documentation: Keep procedures aligned with changes.
-
Training programs: Reinforce new standards and methods.
-
Regular reviews: Spot any signs of regression early.
Walking the Path to Success
Achieving goals in Six Sigma requires more than technical knowledge—it requires strategy, discipline, and teamwork. From understanding its core principles to setting SMART goals, leveraging data, and sustaining improvements, the path to success is clear and proven.
Whether you’re a professional pursuing certification or a leader managing improvement projects, the Six Sigma methodology provides a powerful roadmap to consistent, measurable, and lasting success.