Demystifying Six Sigma: Tools, Techniques, and Certification
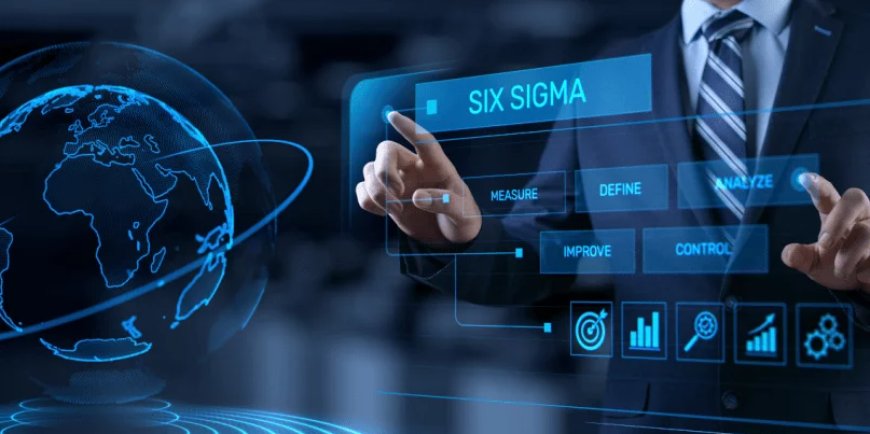
Six Sigma is a method used by businesses to make things work better. It's all about finding problems and fixing them to make things work smoother and cheaper. People who know Six Sigma use special tools and techniques, like looking at data and doing tests, to figure out what's wrong and how to make it right. When businesses use Six Sigma, they can save money, make customers happier, and do better than their competition.
Knowing how to use Six Sigma tools and techniques helps people smartly fix problems. It's like having a special toolbox to solve puzzles at work. By using these tools, businesses can save money by not wasting materials or time. They can also make customers happier by giving them what they want. When people get certified in Six Sigma, it shows they're good at fixing things. This can help them get better jobs or do better in the jobs they already have. Overall, Six Sigma helps businesses and people do their jobs better and be more successful.
Understanding Six Sigma
Six Sigma is a way for businesses to improve how they work. It started in manufacturing but is now used by many types of companies. The main idea is to make processes better by reducing mistakes and making things more efficient. The key principles of Six Sigma are focusing on what customers want, using data to make decisions, and aiming for perfection, even if it's hard.
Implementing Six Sigma can help organizations in a few ways. It can save money by cutting down on mistakes and waste. It also makes customers happier because products and services are better. Plus, it helps companies compete better in the market.
What are the essential tools for the Six Sigma methodology?
DMAIC is a structured approach used in Six Sigma to solve problems and improve processes. It stands for define, measure, analyze, improve, and control. Each phase has specific tasks aimed at understanding the problem, gathering data, finding root causes, implementing solutions, and maintaining improvements.
Essential tools in the Six Sigma methodology encompass various techniques and methods aimed at improving processes and reducing defects. These tools are systematically applied throughout the Define, Measure, Analyze, Improve, and Control (DMAIC) phases. Some fundamental tools include:
-
Process Mapping: This tool involves visually representing the steps in a process, including inputs, outputs, and actions taken. It helps identify bottlenecks, redundancies, and areas for improvement by providing a clear understanding of how the process flows.
-
Cause and Effect Diagrams (Fishbone or Ishikawa Diagrams): These diagrams help identify potential causes of a problem by categorizing contributing factors into main categories such as people, processes, equipment, materials, and environment. By organizing factors in this way, teams can systematically explore root causes.
-
Data Collection Plans: Establishing a structured approach to collecting data is crucial for understanding the current state of the process and quantifying the extent of the problem. Data collection plans outline what data needs to be collected, how it will be collected, and who is responsible for collecting it.
-
Statistical Analysis: Statistical methods such as descriptive statistics, hypothesis testing, regression analysis, and correlation analysis are used to analyze collected data. These analyses help identify patterns, trends, and relationships within the data, enabling teams to make data-driven decisions and identify the root causes of problems.
-
Design of Experiments (DOE): DOE is a systematic approach to testing multiple variables simultaneously to optimize processes and identify the most effective solutions. It allows teams to understand how different factors interact and their impact on process outcomes.
-
Control Charts: Control charts are graphical tools used to monitor process performance over time. By plotting data points on a chart and comparing them to control limits, teams can identify trends, patterns, and variations in the process and take corrective action if necessary.
-
SIPOC Diagram (Suppliers, Inputs, Process, Outputs, Customers): This diagram provides a high-level overview of the process, outlining key components such as suppliers, inputs, process steps, outputs, and customers. It helps teams understand the scope of the process, identify stakeholders, and establish process boundaries.
-
Project Charter: A project charter is a document that outlines the project objectives, scope, timeline, resources, and stakeholders. It serves as a roadmap for the project and ensures alignment with organizational goals and priorities.
Six Sigma Techniques:
A. Lean Six Sigma: Lean Six Sigma combines the principles of Six Sigma and Lean manufacturing to improve efficiency and reduce waste in processes. It focuses on identifying and eliminating activities that don't add value to the customer, streamlining operations, and optimizing resources.
B. Design for Six Sigma (DFSS): DFSS is a methodology used in product or service development to ensure that customer requirements are met and defects are minimized from the outset. It emphasizes the importance of understanding customer needs, designing processes that meet those needs, and minimizing variation in the final product or service.
C. Voice of the Customer (VOC): VOC techniques involve gathering and analyzing customer feedback to understand their needs, preferences, and expectations. Methods include surveys, interviews, focus groups, and observations. By capturing the VOC, organizations can align their products and services with customer requirements, leading to higher satisfaction and loyalty.
D. Failure Mode and Effects Analysis (FMEA): FMEA is a proactive approach to identifying potential failures in processes, products, or services, and assessing their impact. By analyzing potential failure modes and their effects, organizations can prioritize risks and implement preventive measures to mitigate them, improving overall process reliability and quality.
The Career Success of Six Sigma Certification
Six Sigma certification demonstrates expertise in process improvement methodologies, enhancing career opportunities and advancement prospects. It signifies proficiency in problem-solving, data analysis, and project management, which are valued skills across various industries.
Different Levels of Six Sigma Certification:
In the journey of Six Sigma certification, individuals progress through distinct levels, each signifying a deeper understanding and proficiency in process improvement methodologies:
-
White Belt: Grasps fundamental Six Sigma concepts and terminology, laying the groundwork for further learning and application.
-
Yellow Belt: Embraces basic tools and techniques, often contributing to project teams and gaining hands-on experience in process improvement initiatives.
-
Green Belt: Acquires comprehensive knowledge of Six Sigma methodologies, is capable of leading projects with guidance from Black Belts, and drives meaningful improvements within organizations.
-
Black Belt: Attains mastery of Six Sigma principles, is adept at leading complex projects independently, mentoring Green Belts, and implementing impactful changes to enhance efficiency and quality.
-
Master Black Belt: Reaches the pinnacle of certification, providing strategic direction to organizations, offering expert guidance to Black Belts, and shaping the continuous improvement culture through coaching and training initiatives.
Requirements for Each Certification Level
Requirements vary by certifying body but generally involve completing training, passing exams, and demonstrating practical application through project work. Prerequisites typically include relevant work experience and the completion of prerequisite certifications for higher levels.
Benefits of Certification
Benefits include increased job opportunities, higher earning potential, enhanced problem-solving skills, and recognition as a qualified process improvement professional. Certification also validates expertise, instills confidence in employers, and opens doors to leadership roles in organizations committed to quality and continuous improvement.
Common Misconceptions about Six Sigma
Common myths about Six Sigma include the belief that it's only for manufacturing, which isn't true and can be applied across various sectors in healthcare, finance, and services. Another myth is that it's too complicated and needs lots of statistical knowledge. However, Six Sigma focuses on practical problem-solving and can be tailored to different skill levels. Misunderstandings about Six Sigma include thinking it's a quick fix but a process needing dedication. Also, it's not just for big companies—any organization can benefit. Six Sigma doesn't aim to eliminate all defects; it focuses on reducing variation to meet customer needs consistently. Overall, it's a flexible and powerful tool for achieving excellence and improvement.
the basics of Six Sigma include its origins, key principles, and common misunderstandings. It's clear that Six Sigma isn't just for big companies or limited to manufacturing—it's applicable across various industries and focuses on practical problem-solving rather than complex statistics. Understanding Six Sigma tools, techniques, and certification is crucial for professionals and organizations alike. It equips individuals with valuable skills in process improvement and data analysis, enhances career opportunities, and contributes to organizational success. Certification serves as a badge of expertise, demonstrating dedication to quality and continuous improvement. Ultimately, Six Sigma enables organizations to streamline processes, meet customer needs, and stay competitive in today's fast-paced business world.