Discovering the Value of Six Sigma
Improve efficiency & quality with Six Sigma. Learn its value, benefits & how to use it. Upgrade your processes with Six Sigma principles.
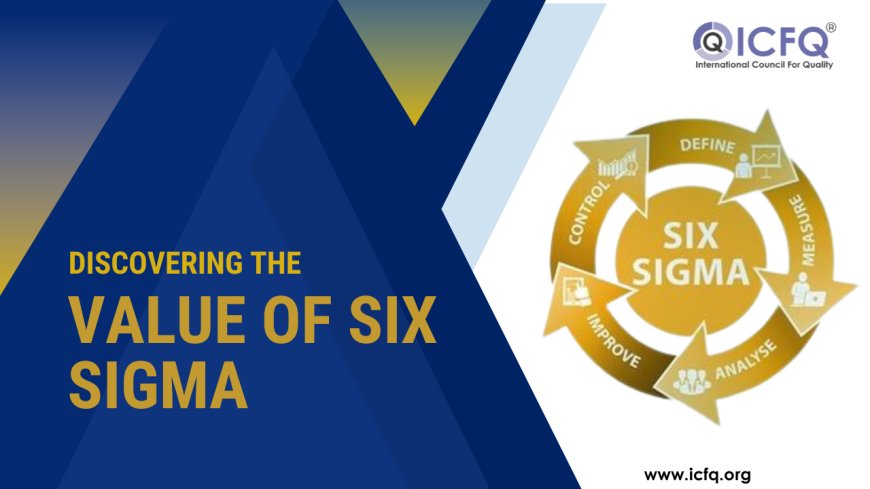
Six Sigma is a strategy that businesses use to improve how they work and maintain high quality. It focuses on understanding and fixing errors in company processes using a clear five-step method called DMAIC: Define the problem, Measure how big the issue is, Analyze the data collected, Improve by finding solutions, and Control the process to make sure it stays fixed.
This approach is used across many sectors like manufacturing where products are made, healthcare where patient care quality is crucial, finance where accuracy is key, and technology where innovation is constant. Using Six Sigma, companies can lower their costs, make customers happier, and run their operations more efficiently. This method has gained popularity because it has consistently helped improve business performance and product quality.
What are the benefits of fully implementing Six Sigma?
Six Sigma helps organizations by making their business processes more efficient and ensuring that their products are of consistent quality. It focuses on reducing mistakes and problems in operations, which leads to more reliable results. Organizations that use Six Sigma analyze their data carefully to pinpoint where the problems are and then fix them. This often helps them save money because they spend less on fixing errors and waste.
Additionally, Six Sigma promotes a workplace culture where continuous improvement is valued. Employees are trained to think critically and use data to make decisions, which not only enhances their daily work but also increases their job satisfaction as they see their contributions making a difference. This approach also improves customer satisfaction, as the quality and reliability of products and services increase. Overall, fully implementing Six Sigma can significantly improve an organization's efficiency, reduce costs, and strengthen its position in the market.
How Can Six Sigma Improve Operations, Finances, and Customer Service?
Businesses can use Six Sigma to improve in several key areas:
-
Operational Efficiency: Six Sigma helps companies find problems in their operations using a step-by-step method called DMAIC (Define, Measure, Analyze, Improve, Control). By identifying and solving these problems, businesses can make their processes smoother, reduce unnecessary work, and get more done with less effort. This practical approach to problem-solving is based on clear evidence, making the improvements reliable and effective.
-
Financial Performance: When companies implement Six Sigma, they often see cost savings. This happens because the approach helps reduce errors and defects, which means less waste and fewer costs related to fixing mistakes. Six Sigma also helps businesses manage their resources better and keep track of their inventory more effectively, which can improve financial outcomes.
-
Customer Satisfaction: Six Sigma also focuses on making products and services better by making them more consistent and reducing mistakes that bother customers. When customers consistently receive what they expect, they are more likely to stay loyal to the brand, return for more, and recommend the company to others. Better quality control and focusing on what customers need can also help businesses attract new customers and expand into new markets.
By adopting Six Sigma, companies can improve their day-to-day operations, strengthen their financial health, and build stronger relationships with their customers. This broad impact can help businesses grow sustainably and gain an edge over competitors.
Exploring the Values of Six Sigma
- Improving Process Efficiency with Six Sigma
Six Sigma improves process efficiency by reducing variability and eliminating defects in business processes. Here’s how it specifically addresses and enhances efficiency:
1. Data Analysis: Six Sigma uses statistical tools to analyze data from business processes. This analysis helps identify the root causes of inefficiencies and defects. By understanding what causes these issues, businesses can make targeted improvements.
2. Process Mapping: Six Sigma involves mapping out all steps of a process to visualize where delays, unnecessary steps, or bottlenecks occur. This clear visualization helps simplify the process, eliminating non-value-added activities, and ensuring that every step adds to the efficiency of the overall process.
3. Standardization: By standardizing processes, Six Sigma reduces variability, which is often a major cause of inefficiencies. Consistent processes are easier to manage, predict, and improve over time.
4. Continuous Improvement: The DMAIC (Define, Measure, Analyze, Improve, Control) framework encourages continuous monitoring and refinement of processes. This ongoing improvement cycle ensures that processes remain efficient even as business conditions change.
- Six Sigma Sustaining Cost Reduction
Six Sigma is a strategy used by businesses to cut down on costs while maintaining quality. Here’s how it helps reduce expenses effectively:
1. Identifying Waste: Six Sigma helps companies identify parts of their operations where resources are being used inefficiently, such as time, materials, or manpower.
2. Reducing Defects: By focusing on quality control, Six Sigma reduces errors in production or service delivery. Fewer defects mean less money spent on fixing mistakes or replacing faulty products.
3. Streamlining Processes: Six Sigma involves reviewing and refining processes to make them more efficient. This can include simplifying steps, improving workflow, or introducing more effective technologies.
4. Consistent Monitoring: Continual monitoring is a key part of Six Sigma. This helps ensure that the improvements lead to sustained cost savings and prevent old habits from causing costs to rise again.
- Enhancing Quality with Six Sigma
Six Sigma is a method that helps businesses improve the quality of their products and services. It does this by focusing on removing errors and inconsistencies from processes. Here’s how it works:
1. Setting High Standards: Six Sigma sets strict standards to measure quality, aiming to reduce defects to nearly zero.
2. Analyzing Processes: This involves thoroughly examining all steps in a process to find out where things might go wrong or where quality might drop.
3. Implementing Changes: Based on the analysis, changes are made to eliminate errors and ensure that every part of the process contributes to a high-quality result.
4. Ensuring Consistency: Six Sigma uses ongoing monitoring and controls to make sure that improvements are maintained and quality remains high over time.
- Boosting Customer Satisfaction with Six Sigma
Six Sigma is a strategy businesses use to improve customer satisfaction by ensuring their services and products consistently meet customer expectations. Here’s how it works:
1. Understanding Customer Needs: Six Sigma focuses on clearly defining what customers expect from products and services in the first phase. This is done through customer feedback and market analysis.
2. Measuring Performance: Next, the actual performance of products or services is measured. This helps to see how closely the current outputs match with what customers expect.
3. Tailoring Improvements: Specific improvements are planned Using the data from the first two steps. These adjustments are directly tied to the customer's needs and expectations, ensuring that changes are relevant and impactful.
4. Continual Monitoring: Six Sigma includes ongoing checks to make sure that the improvements are working and customer satisfaction is increasing. If any new issues arise, they can be quickly addressed.
By focusing on customer needs from the start and continuously monitoring outcomes, Six Sigma helps businesses deliver products and services that make their customers happy, thereby boosting customer satisfaction.
- Six Sigma and Cultural Transformation
Six Sigma can change the way a company works by encouraging a culture focused on continuous improvement and quality. Here’s how it does this in simple terms:
1. Everyone Gets Involved: Six Sigma includes people at all levels in a company, from the top to the bottom. This helps everyone feel they are part of making things better.
2. Decisions Based on Facts: This approach teaches companies to make decisions based on data, not just guesses. This means better choices that can lead to better results.
3. Constant Improvement: Six Sigma pushes for ongoing improvements, not just one-time changes. It encourages a mindset of always looking for ways to do things better.
4. Training and Skills: It provides training in specific skills that help employees understand and improve their work processes.
5. Valuing Improvements: When improvements are made, they are recognized and rewarded, which motivates everyone to keep focusing on quality and efficiency.
This way, Six Sigma helps build a work culture that embraces change, focuses on quality, and is always trying to improve.
- Gaining Strategic Advantage
Six Sigma can give businesses a strategic edge in competitive markets by improving quality and efficiency. Here’s how it does this in straightforward terms:
1. Better Quality: Six Material helps companies make sure their products and services are top-notch. This leads to fewer mistakes, happier customers, and more repeat business.
2. More Efficient: By making processes smoother and cutting out waste, Six Sigma helps businesses do more with less. This can mean faster service or lower costs, both of which can make a company more competitive.
3. Smarter Decisions: Six Sigma is all about using data to make decisions. This approach helps businesses avoid guesswork and focus their efforts where they can make a difference.
4. Always Improving: Six Sigma encourages companies to keep looking for ways to get better. This drive for continuous improvement keeps a business dynamic and better prepared to adapt to new challenges.
5. Engaged Employees: Six Sigma training can make employees more skilled and involved in their work. When employees are engaged, they're more likely to do a good job, which boosts the overall performance of the company.
Barriers to Six Sigma Adoption
Six Sigma is a systematic approach aimed at enhancing business operations and ensuring high quality, but some organizations hesitate to adopt it. This hesitation often stems from the perceived complexity of the methodology and the initial costs involved. The process of integrating Six Sigma can seem daunting due to its detailed, data-driven nature, which requires a thorough understanding and implementation of its five key phases: Define, Measure, Analyze, Improve, and Control.
Additionally, setting up Six Sigma involves training employees, investing in data analysis tools, and sometimes hiring specialists, which can lead to significant upfront expenses. Despite these challenges, the potential long-term benefits like cost savings, improved customer satisfaction, and better overall efficiency can outweigh the initial hurdles for many companies.
Six Sigma is a powerful approach that offers many benefits to businesses, including reducing costs, enhancing efficiency, and providing a competitive edge. It helps organizations streamline operations and improve quality by focusing on reducing waste and managing defects. Adopting Six Sigma can transform how a business operates, encouraging a culture of continuous improvement and alignment with customer needs. This makes it a valuable tool for any company looking to improve its processes and overall performance.