Tools and Techniques for Success with Six Sigma
Meta Description: Learn essential tools and techniques for Six Sigma success. Improve efficiency, reduce errors, and achieve business excellence.
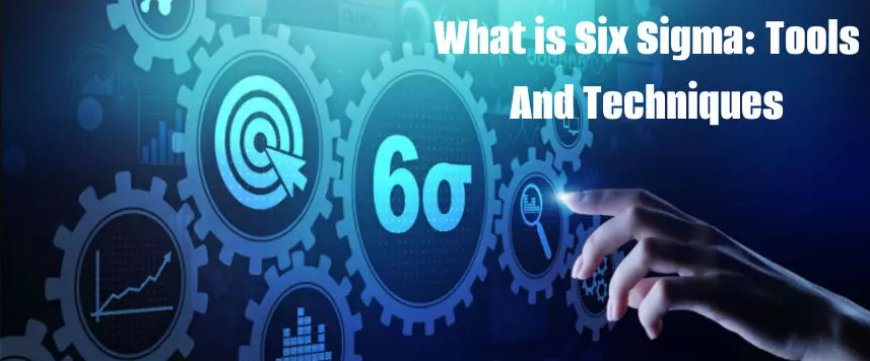
Six Sigma is a method for improving processes and reducing errors. It aims to make processes almost perfect, with very few errors. To achieve this, Six Sigma uses tools and techniques like process mapping, cause and effect analysis, statistical process control charts, and more. These tools help in identifying problems, analyzing data, and finding solutions. The importance of these tools lies in their ability to provide structure to problem-solving and decision-making. They help prioritize improvement efforts, monitor process performance, and ensure consistent quality. For businesses, mastering these tools can lead to increased efficiency, reduced waste, and higher customer satisfaction.
The main purpose is to explore these tools and techniques in-depth, offering practical insights and examples. By understanding and applying these tools effectively, organizations can drive continuous improvement and achieve success with Six Sigma initiatives.
Understanding Six Sigma
Six Sigma is a method for improving processes by reducing errors and variations. It originated in the 1980s at Motorola and gained popularity through General Electric. The term "Six Sigma" refers to achieving a level of quality where there are only 3.4 defects per million opportunities.
There are also some key principles of Six Sigma, which include customer focus, data-driven decision-making, process improvement, and organizational involvement. The main objectives are to improve quality, increase efficiency, reduce costs, and enhance customer satisfaction.
Essential Tools for Six Sigma
1. Statistical Process Control (SPC)
Statistical Process Control (SPC) is a method used in Six Sigma to monitor and control processes. It involves using statistical techniques to track and analyze process performance over time. SPC helps identify trends, patterns, and variations in data, allowing organizations to detect and address issues before they lead to defects or errors in products or services. Examples of SPC charts include control charts, which plot process data over time to identify any trends or shifts that may indicate a problem. Histograms are used to visually represent the distribution of data and identify patterns or outliers.
2. Design of Experiments (DOE)
DOE, or Design of Experiments, is a powerful tool in Six Sigma for figuring out which factors are most important in a process. It helps identify critical process variables, meaning it pinpoints which factors have the biggest impact on outcomes. By testing different variables in controlled experiments, teams can see which ones really matter and focus their efforts there. This saves time and resources by avoiding guesswork and targeting improvements where they'll make the most difference. DOE systematically changes factors to see their impact on outcomes, and by planning and analyzing these experiments, teams gain valuable insights. This helps make informed decisions and improve processes effectively.
3. Failure Mode and Effects Analysis (FMEA)
FMEA, or Failure Mode and Effects Analysis, is a method used in Six Sigma to identify and prioritize potential risks in a process or product. FMEA is all about spotting problems before they happen. It helps teams anticipate potential failures in processes or products and understand their effects on quality and customers. By identifying these risks early, organizations can take steps to prevent them and improve their overall performance.
Identify potential failure modes: List all the ways a process or product could fail. This step involves brainstorming and listing all the different ways a process or product could go wrong. It's like making a list of possible problems or errors that could occur.
Determine the effects of each failure: Once potential failure modes are identified, it's important to understand how each one could impact the quality of the product or service, or how it might affect customer satisfaction. This helps in assessing the seriousness of each potential issue.
Assign severity, occurrence, and detection ratings: Here, we rate the seriousness of each potential failure (severity), how often it might happen (occurrence), and how likely it is to be caught before causing harm (detection). These ratings help prioritize which failures need immediate attention.
Calculate risk priority numbers (RPNs): RPNs are calculated by multiplying the severity, occurrence, and detection ratings together. This helps prioritize which failures are most critical and need to be addressed first.
Develop action plans: Based on the RPNs, action plans are created to reduce the likelihood or severity of high-priority failures. These plans outline specific steps to be taken to prevent or mitigate potential problems.
Implement and monitor improvements: Once action plans are developed, they are put into action. It's important to monitor how well these improvements work and make adjustments as needed. This step ensures that the organization continues to improve its processes and prevent future failures.
4. Root Cause Analysis (RCA)
Root Cause Analysis (RCA) is a method used in problem-solving to identify the underlying reasons behind issues or failures, aiming to prevent them from reoccurring. Rather than just treating symptoms, RCA digs deep to find the real reasons behind problems. By uncovering the root causes, organizations can implement effective solutions that address the core issues and prevent similar problems in the future. RCA is crucial in problem-solving because it helps teams tackle issues at their source, leading to more sustainable and long-lasting improvements.
There are two techniques in RCA:
5 Whys: This technique involves asking "why" repeatedly to get to the root cause of a problem. By asking "why" multiple times, teams can peel back the layers of the issue until they reach its underlying cause.
Fishbone diagram (or Ishikawa diagram): This visual tool helps teams brainstorm and organize potential causes of a problem into categories like people, processes, equipment, environment, and materials. By mapping out these factors, teams can systematically explore and identify the root cause of the problem.
What are the techniques for Six Sigma success?
-
Lean Six Sigma integration
It combines the efficiency-focused principles of Lean with the quality-centric methodologies of Six Sigma, offering a comprehensive approach to process improvement. It focuses on waste elimination, process streamlining, and reducing variation and defects. A combined approach results in faster processes with fewer errors and improved customer satisfaction due to enhanced quality. Lean Six Sigma has reduced costs through waste reduction, improved efficiency, increased profitability from streamlined processes, and satisfied customers. Some examples of lean tools are value stream mapping and 5S.
-
Change Management Strategies
Change management is crucial in Six Sigma projects to ensure successful implementation and sustained improvements. Effective change management should ensure that Six Sigma initiatives are embraced by employees and integrated into the organizational culture. It helps manage resistance, aligns stakeholders, and ensures that changes are implemented smoothly, minimizing disruptions and maximizing benefits. There are some strategies for overcoming resistance to change:
-
Communication: Effective communication is key. It involves explaining why the change is happening, its benefits, and how it will affect everyone involved. Frequent updates keep everyone informed, and honesty builds trust.
-
Involvement: Engaging employees in the change process makes them feel valued and invested. By seeking their input and involving them in decision-making, employees are more likely to embrace the change and take ownership of its success.
-
Education and Training: Providing adequate training and resources ensures that employees have the skills and knowledge needed to adapt to the change. Training sessions and workshops equip employees with the tools they need to succeed in the new environment.
-
Leadership Support: Visible support from leaders is crucial. When leaders endorse the change and actively demonstrate their commitment, it inspires confidence and reassures employees that the change is necessary and worthwhile.
-
Celebrate Success: Recognizing and celebrating milestones and achievements along the way boosts morale and motivates employees to continue working towards the goals of the change. Celebrations reinforce progress and encourage continued commitment to the change process.
-
Project Management Techniques
-
Project Planning Methodologies
Project planning and scheduling Methodologies involve breaking big projects into smaller tasks. We use tools like Gantt charts or the Critical Path Method (CPM) to help us organize these tasks and figure out which ones need to be done first. Gantt charts show us when tasks start and finish, as well as any important milestones. Meanwhile, CPM helps us find the longest sequence of tasks that need to be done on time. Additionally, Agile methods like Scrum or Kanban help us plan flexibly, so we can easily adapt to any changes that come up during the project. These methods make sure our projects stay on track, everyone knows what they need to do, and we can adjust our plans if needed.
-
Stakeholder Management and Communication Strategies:
These strategies start with identifying key project stakeholders and learning what they care about. We then create a communication plan to keep them in the loop about project updates. Regular meetings, reports, and updates keep everyone informed about project progress, risks, and changes. We make sure to address any feedback or concerns from stakeholders quickly to keep their support. We use different communication tools, like meetings, emails, and collaboration platforms, to make sure everyone stays connected and informed at every stage of the project. This helps build trust and teamwork throughout the project's journey.
The future of Six Sigma and continuous improvement efforts appears promising. As businesses strive for excellence and adapt to evolving market demands, the need for systematic problem-solving and quality management will only grow. By embracing Six Sigma principles and leveraging its tools and techniques, organizations can stay competitive and drive sustained success in the years to come.
They provide structure to problem-solving, help prioritize improvement efforts, and ensure consistent quality. By mastering these tools, organizations can increase efficiency, reduce waste, and enhance customer satisfaction.