Mastering Lean Six Sigma for Success
Learn how to master Lean Six Sigma techniques for guaranteed success in business. Gain valuable skills with our easy-to-follow training
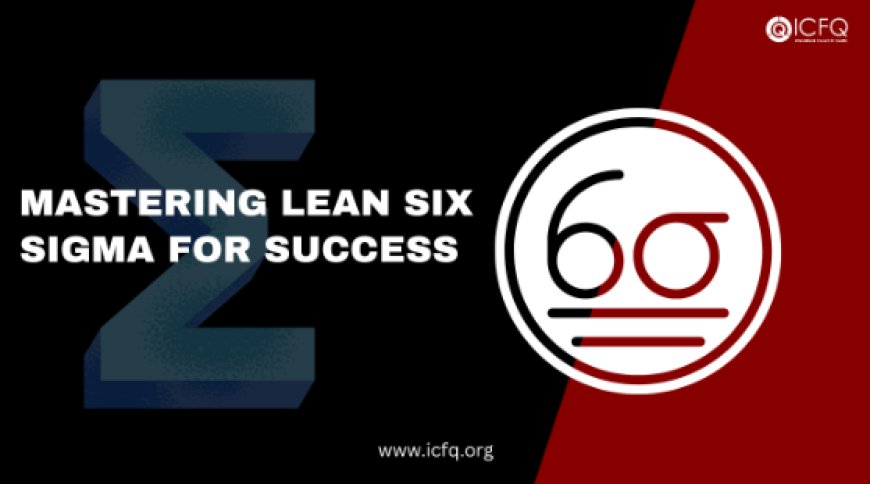
Lean Six Sigma is a strategy that merges Lean manufacturing principles with Six Sigma tools to improve efficiency and quality in business processes. Lean aims to cut down waste by identifying and removing unnecessary steps, while Six Sigma focuses on minimizing errors and inconsistencies by using detailed data analysis and process improvements.
This method involves a structured framework known as DMAIC: Define, Measure, Analyze, Improve, and Control. This five-step process helps teams identify issues, measure their impact, find their root causes, implement solutions, and maintain these improvements over time. By applying Lean Six Sigma, organizations can reduce costs, improve compliance with regulations, and support a culture where employees are encouraged to enhance processes. This approach is used in various sectors such as manufacturing, healthcare, and services to streamline operations and improve customer satisfaction.
Driving Business Excellence Through Lean Six Sigma
In many industries, the current state of business processes is characterized by an increasing push toward operational excellence. Organizations are continuously seeking ways to improve efficiency, reduce costs, and enhance customer satisfaction. This drive for better performance and competitive advantage has led to the widespread adoption of methodologies like Lean Six Sigma.
Lean Six Sigma, which combines the waste-reducing practices of Lean with the defect-reducing focus of Six Sigma, is being increasingly implemented across various sectors. This method helps companies streamline their operations and minimize errors through a structured approach involving the DMAIC phases: Define, Measure, Analyze, Improve, and Control. The adoption of this methodology is driven by the need to adapt to changing market conditions, increase productivity, and deliver higher-quality products and services to customers.
What are the key components of Lean Six Sigma that are critical for success?
Lean Six Sigma is a powerful methodology for process improvement, combining elements from both Lean manufacturing and Six Sigma. The key components that are critical for its success include:
-
DMAIC Framework: This stands for Define, Measure, Analyze, Improve, and Control. It is a systematic, structured approach used for problem-solving and project management, ensuring that improvements are consistent and measurable.
-
Lean Principles: These focus on reducing waste and increasing process speed. Key principles include value stream mapping, 5S (Sort, Set in order, Shine, Standardize, Sustain), and Just-In-Time production, which help identify and eliminate non-value-adding activities.
-
Six Sigma Tools: These are techniques used to improve quality and reduce variability. They include statistical analysis tools like control charts, regression analysis, and hypothesis testing, which help in understanding and minimizing process deviations.
-
Continuous Improvement: Lean Six Sigma encourages a culture of ongoing improvement where processes are continually evaluated and refined. This mindset helps organizations adapt to changes in demand or technology without sacrificing quality or performance.
-
Training and Certification: Comprehensive training programs for Green Belts, Black Belts, and other roles are essential. These programs equip individuals with the necessary skills to lead Lean Six Sigma projects and drive change effectively within an organization.
-
Top Management Support and Commitment: Leadership buy-in is critical for the success of Lean Six Sigma initiatives. Leaders must support the methodology, provide the necessary resources, and be actively involved in the change process to foster a supportive environment.
Lean Six Sigma Methodologies and Tools
Lean Six Sigma is a methodology that merges Lean manufacturing practices focused on reducing waste with Six Sigma techniques aimed at reducing process variability and defects. This approach is designed to enhance organizational efficiency, product quality, and customer satisfaction. Key methodologies like DMAIC (Define, Measure, Analyze, Improve, Control) and DMADV (Define, Measure, Analyze, Design, Verify) provide structured processes for improving existing systems and designing new ones to meet Six Sigma standards, respectively.
The effectiveness of Lean Six Sigma largely hinges on the use of specific tools and techniques:
Lean Tools
-
Value Stream Mapping: Helps identify all actions within a process, distinguishing between value-added and non-value-added steps.
-
Kaizen: Focuses on continuous, incremental improvements through team collaboration.
-
5S: Aims to create a clean, organized, and efficient work environment through a systematic approach to workplace organization.
Six Sigma Tools
-
Statistical Process Control (SPC): Employs statistical methods to monitor and control a process for optimal performance.
-
Design of Experiments (DOE): Assists in determining relationships between different process factors and their effects on output.
-
Root Cause Analysis (RCA): Helps identify the underlying causes of defects or problems to prevent recurrence.
These tools are critical in translating the principles of Lean Six Sigma into practical, actionable steps that improve processes. They enable organizations to perform detailed analyses, make data-driven decisions, and implement solutions that lead to better process management and enhanced output quality. By adopting Lean Six Sigma, organizations can improve workflows, reduce costs, and achieve more consistent outcomes, thus embedding quality into every facet of their operations.
Implementation Strategies for Lean Six Sigma
Steps to Effectively Train Teams in Lean Six Sigma Principles
-
Assessment of Current Skills: Begin by assessing the current understanding and skills of the teams regarding Lean Six Sigma to tailor the training accordingly.
-
Structured Training Program: Implement a structured training program that includes courses and workshops tailored to different roles within the organization, such as Yellow Belts, Green Belts, and Black Belts.
-
Hands-On Projects: Encourage learning by doing, where trainees participate in actual projects as they learn. This practical experience helps to reinforce theoretical knowledge.
-
Mentorship: Pair trainees with experienced Lean Six Sigma practitioners who can provide guidance, feedback, and support as they apply their learning in real-world scenarios.
-
Certification: Offer certification at the end of the training process to validate the skills and knowledge acquired, which also serves to motivate employees to complete their training.
How to Cultivate a Culture That Supports Continuous Improvement?
Leadership involvement is key in Lean Six Sigma initiatives, requiring leaders to actively participate and show their commitment to continuous improvement. A system to recognize and reward contributions to process improvements can motivate employees to actively seek opportunities for enhancement. Regular communication about the goals, processes, and outcomes of Lean Six Sigma projects is necessary to keep all employees informed and engaged. By empowering employees with the authority and responsibility to identify and implement improvements, organizations encourage a proactive attitude. Furthermore, promoting an environment of continuous learning through participation in workshops, seminars, and industry conferences helps sustain employee development and process innovation.
Key Metrics to Monitor for Ensuring Ongoing Success
-
Process Efficiency: Measure improvements in process efficiency, such as increased speed, reduced cycle time, and better throughput.
-
Quality Metrics: Track quality metrics like defect rates, the number of errors, or customer complaints to evaluate improvements in product or service quality.
-
Customer Satisfaction: Monitor customer satisfaction through surveys, feedback, and service metrics to assess how process changes enhance customer experience.
-
Financial Metrics: Keep an eye on financial metrics such as cost savings, return on investment (ROI), and profit margins to quantify the financial impact of Lean Six Sigma projects.
-
Employee Engagement: Measure employee engagement levels through surveys and feedback channels to ensure that the workforce is motivated and committed to continuous improvement efforts.
Mastering Lean Six Sigma equips organizations with tools to enhance their operational efficiency by identifying and eliminating wasteful practices and reducing process variability, which leads to more consistent quality in products or services. The methodologies encourage a culture of continuous improvement, promoting detailed analysis and streamlined processes. Adopting these practices can support long-term business success by fostering better customer satisfaction and achieving more predictable and stable outcomes. This approach not only helps in maintaining competitive advantage but also encourages a proactive workforce engaged in ongoing development and innovation.