Mastering Six Sigma Techniques
Discover the essence of Six Sigma techniques for mastery. Learn proven strategies to optimize processes and drive efficiency.
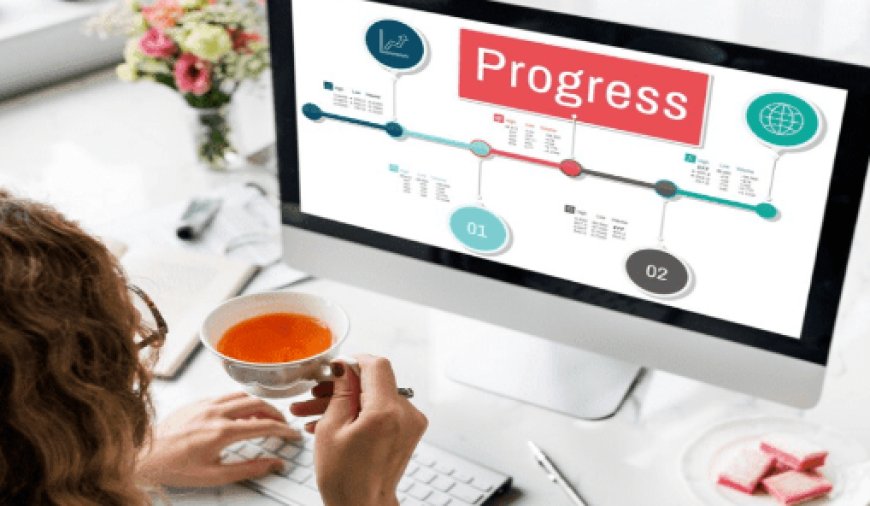
Efficiency and quality are vital in business because they determine how well a company operates and satisfies its customers. Efficiency means doing things quickly and effectively, while quality ensures that what you deliver is top-notch and meets customer expectations. Both aspects are essential for keeping customers happy and maintaining a competitive edge in the market.
Six Sigma is a method that helps businesses improve efficiency and quality by identifying and fixing any problems or errors in their processes. It uses data and analysis to pinpoint areas for improvement, leading to smoother operations and better products or services. Ultimately, Six Sigma helps companies save money, reduce waste, and deliver consistent quality, contributing to their overall success and growth.
Common Productivity Hurdles
-
Maintaining high standards of quality and efficiency can be tough for businesses due to several challenges. One common issue is defects, which are mistakes or errors in products or services. These defects can lead to customer dissatisfaction, increased costs, and wasted resources.
-
Variability is another challenge businesses face. Variability refers to inconsistencies in processes or outputs, making it difficult to predict outcomes or maintain consistent quality. This inconsistency can lead to inefficiencies and lower customer satisfaction.
-
Waste is also a significant issue that hinders productivity. Waste can come in various forms, such as excess materials, time, or energy. It occurs when resources are not used efficiently, leading to increased costs and reduced profitability.
How can businesses effectively address these challenges and achieve operational excellence?
Businesses can tackle these challenges and achieve operational excellence by implementing specific strategies. To address defects, they can invest in quality control measures like regular inspections and employee training to ensure products or services meet standards. For managing variability, businesses can standardize processes and use tools like Six Sigma to identify and minimize variations, leading to more consistent outcomes.
To combat waste, companies can adopt lean principles, which focus on reducing unnecessary steps and resources in processes. This includes practices like just-in-time inventory management and optimizing workflows to eliminate bottlenecks and inefficiencies.
Moreover, fostering a culture of continuous improvement within the organization is crucial. Encouraging employees to identify problems, suggest solutions, and participate in process optimization can lead to ongoing enhancements in quality and efficiency.
Training and Certification
Formal training in Six Sigma is important as it gives individuals a structured understanding of the methodology and its tools. This training equips them with the knowledge and skills needed to effectively apply Six Sigma principles to improve processes and solve business problems.
Six Sigma certification levels include the Yellow Belt, Green Belt, and Black Belt. Yellow Belt certification offers a basic understanding of Six Sigma concepts and terminology. Green Belt certification signifies deeper knowledge and the ability to lead smaller improvement projects within an organization. Black Belt certification indicates mastery of Six Sigma principles and the capability to lead complex improvement initiatives and mentor Green Belts.
Options for Six Sigma training and certification programs vary, ranging from in-person courses to online training modules. Many accredited institutions and organizations offer these programs, providing flexibility in terms of timing and delivery methods. Additionally, some companies offer internal training programs for employees interested in pursuing Six Sigma certification. These options allow individuals to choose the training format that best fits their learning preferences and schedule.
Key principles and techniques of Six Sigma
-
Six Sigma relies on a few key principles and techniques to improve processes. One important principle is DMAIC, which stands for Define, Measure, Analyze, Improve, and Control. This method guides teams through the process of identifying problems, measuring performance, analyzing data to find root causes, implementing solutions, and establishing controls to sustain improvements.
-
Another technique is statistical analysis, which involves using data to understand variation and make informed decisions. Tools like histograms, control charts, and regression analysis help teams identify patterns and trends in processes, enabling them to pinpoint areas for improvement. Additionally, Six Sigma emphasizes the importance of setting clear goals and metrics to measure progress. This ensures that improvements are aligned with the organization's objectives and that teams can track their success over time.
Why are leadership, training, and continuous improvement vital for Long-Term Six Sigma success?
-
Implementing Six Sigma in a business involves practical steps and key factors for success. First, leadership commitment is crucial. Leaders must support and champion Six Sigma initiatives, allocating resources and setting clear expectations for improvement.
-
Employee training is essential for ensuring everyone understands Six Sigma principles and techniques. Providing training on DMAIC methodology and statistical tools equips teams with the skills needed to identify and solve problems effectively.
-
Continuous improvement is vital for sustaining Six Sigma initiatives over time. Encouraging a culture of ongoing learning and innovation empowers employees to seek opportunities for improvement and implement changes to processes continuously.
-
Regular monitoring and review of Six Sigma projects help ensure that progress is on track and that improvements are sustained. By focusing on leadership commitment, employee training, and continuous improvement, businesses can successfully implement and sustain Six Sigma initiatives, driving meaningful change and long-term success.
Embracing Six Sigma techniques enables businesses to enhance efficiency, quality, and customer satisfaction, laying a solid foundation for long-term success. By mastering Six Sigma methodologies, companies can streamline processes, reduce defects, and optimize resource utilization, leading to cost savings and improved profitability. Moreover, Six Sigma encourages a culture of continuous improvement, empowering employees to identify and address issues proactively, and driving innovation and adaptation to meet evolving customer needs. Overall, embracing Six Sigma principles as a strategic approach enables businesses to deliver greater value to customers while maintaining a competitive edge in the market.
mastering Six Sigma techniques is not merely about implementing a set of tools and methodologies; it's about fostering a culture of continuous improvement and unwavering commitment to quality and efficiency. By embracing Six Sigma principles, organizations can streamline processes, reduce defects, and ultimately enhance customer satisfaction. However, sustained success in Six Sigma initiatives requires strong leadership support, comprehensive employee training, and a relentless dedication to ongoing improvement efforts. By prioritizing these elements, businesses can unlock the full potential of Six Sigma, driving lasting transformation and competitive advantage in today's dynamic marketplace.