Achieve More with Lean Six Sigma
Discover how Lean Six Sigma can optimize processes and enhance efficiency. Achieve more with streamlined operations and continuous improvement methodologies.
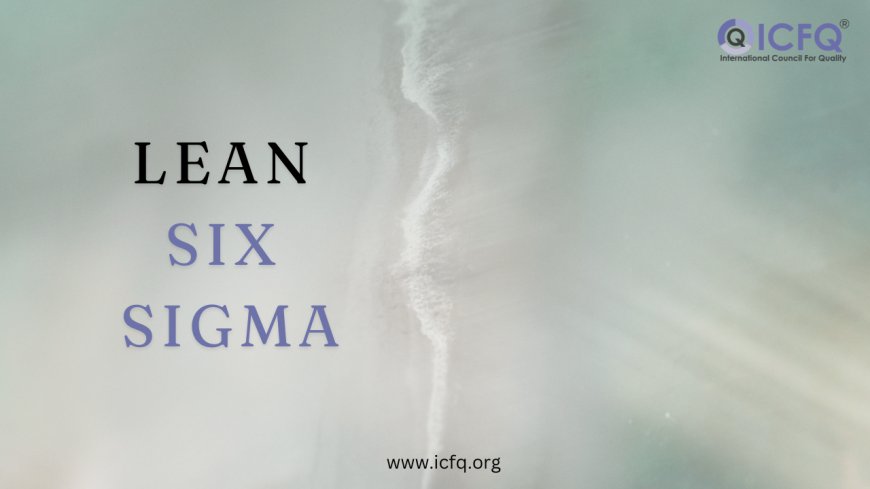
The current business environment is shaped by quick technological changes and a focus on efficiency and sustainability. Companies face challenges such as digital transformation, global competition, and changing consumer demands. To address these issues and improve operations, many organizations adopt Lean Six Sigma.
Lean Six Sigma merges Lean's approach of minimizing waste in processes with Six Sigma's goal of reducing variations and enhancing quality. This method helps businesses streamline processes, improve product quality, and increase customer satisfaction while cutting costs. It uses a structured approach known as DMAIC (Define, Measure, Analyze, Improve, Control), which provides tools and techniques to systematically address problems and improve business performance. By using Lean Six Sigma, companies can make decisions based on data and promote a culture of ongoing improvement, which is vital for success in the current market.
What is Lean Six Sigma?
Lean Six Sigma is a powerful methodology that combines the principles of Lean and Six Sigma, both established frameworks for business improvement. Originating from Toyota's production system in the mid-20th century, Lean focuses on eliminating non-value-added activities to boost efficiency. Six Sigma, which Motorola established in the 1980s, aims to reduce faults and unpredictability in processes by conducting rigorous data-driven analysis. By combining these approaches, Lean Six Sigma enables organizations to make more informed decisions and foster a culture of continuous improvement, which is critical for success in today's fast-paced business climate.
This combined approach helps businesses streamline their processes, improve product quality, and enhance customer satisfaction, all while minimizing costs. Lean Six Sigma employs a structured methodology known as DMAIC—Define, Measure, Analyze, Improve, Control. This method uses specific tools and techniques to systematically address and solve business problems, effectively merging Lean's emphasis on speed and waste reduction with Six Sigma's focus on quality and precision. The result is a comprehensive strategy that enhances overall business performance.
Core Principles of Lean Six Sigma
These principles combine to form a powerful approach for businesses looking to optimize processes, thereby enhancing their performance and competitive advantage.
-
Focus on the Customer: Everything in Lean Six Sigma is driven by customer needs and the desire to increase value to the customer, from reducing process times to eliminating defects.
-
Identify and Understand Value: All activities in a process are evaluated to determine whether they add value from the customer's perspective. Non-value-adding activities are targeted for elimination.
-
Eliminate Waste: Lean Six Sigma targets eight types of waste in processes—defects, overproduction, waiting, non-utilized talent, transportation, inventory, motion, and extra processing. Efforts are focused on reducing or eliminating these wastes.
-
Reduce Variability and Defects: Six Sigma's core aim is to minimize variability in process outputs by using statistical tools to identify and control sources of variation, thus improving quality.
-
Continuous Improvement: Lean Six Sigma encourages continuous scrutiny and improvements of the process through incremental and breakthrough improvements, ensuring that gains are sustained over time.
What strategies can be employed to ensure successful Lean Six Sigma integration?
Integrating Lean Six Sigma successfully into an organization requires thoughtful planning and execution. Here are some straightforward strategies to help ensure its success:
-
Leadership Support: It's important that the organization's leaders fully back the Lean Six Sigma efforts, providing the necessary resources and solving any issues that arise.
-
Training: Everyone in the organization should understand the basics of Lean Six Sigma. Specialized training should be given to those directly involved in the projects to ensure they can apply the methods effectively.
-
Choose the Right Projects: Focus on projects that align with the business's overall goals and can make a noticeable impact. This keeps efforts focused and relevant.
-
Collaborative Teams: Form teams from different areas of the business to bring various perspectives and skills to the project. This helps in analyzing and solving problems more effectively.
-
Cultural Adjustment: Encourage a workplace culture that supports ongoing improvement and is open to new ideas. Employees should feel comfortable suggesting changes and reporting issues.
-
Data-Driven Approach: Lean Six Sigma relies heavily on data, so it's important to use accurate metrics to measure progress and make decisions based on solid data.
-
Maintain Improvements: Once improvements are made, it's crucial to keep them in place. This might mean making new procedures standard and keeping an eye on how they're performing over time.
-
Regular Check-Ins: Continuously check how the integration is going and be ready to make adjustments. This ensures that the approach remains effective and aligned with the organization’s needs.
Monitoring and Continuous Improvement
Monitoring and continuous improvement are essential elements of Lean Six Sigma, ensuring that the benefits of initial process enhancements are sustained and further developed over time. Regular monitoring helps maintain improvements by catching any slip-backs into old habits or inefficiencies. It also identifies new opportunities for enhancement as business environments and technologies evolve. This ongoing evaluation supports incremental improvements, making small, manageable changes that accumulate significant benefits. Additionally, a continuous feedback loop allows for learning from outcomes, adjusting strategies, and staying adaptable to changes in market conditions, customer preferences, and regulations. By integrating continuous monitoring and improvement into their operations, organizations uphold the robustness, responsiveness, and efficiency of their Lean Six Sigma initiatives.
Enhancing Lean Six Sigma with Strategic Planning
Strategic planning is vital for successful Lean Six Sigma initiatives because it gives a clear direction and ensures all efforts are focused on achieving common objectives.
-
Direction and Focus: Setting clear goals with Lean Six Sigma helps everyone understand what they need to work towards, which helps in using resources and efforts efficiently.
-
Relevance: Goals aligned with Lean Six Sigma make sure that the improvements you aim for matter both to your business needs and the methodology, leading to changes that genuinely enhance your business, like cost reduction, better quality, or improved customer satisfaction.
-
Motivation and Engagement: When team members know how their work helps achieve broader goals, they're more likely to be committed and creative.
-
Measurement and Accountability: Specific goals allow you to track progress and hold people accountable, using Lean Six Sigma’s data-driven tools to see if you’re reaching your targets.
-
Continuous Improvement: Strategic planning isn’t about reaching one final goal. It’s about continuous growth, setting new goals after achieving old ones, and constantly improving processes.
-
Adaptability: Strategic planning also means regularly assessing and adjusting your goals to stay effective in a rapidly changing business environment, keeping your organization flexible and responsive.
We've discussed how Lean Six Sigma combines the best of Lean and Six Sigma to improve business efficiency and quality. By using Lean Six Sigma, businesses can manage their processes better, reduce waste, and improve product quality. To keep these improvements, it's important to continuously check and adjust processes. If you're thinking about using Lean Six Sigma, start by looking at your current processes to find areas that could be better. Train your team on Lean Six Sigma basics and pick a small project to begin with. This will help you apply Lean Six Sigma in a way that fits your specific needs and encourages ongoing success.