Lean Six Sigma: The Path to Quality
Discover the transformative power of Lean Six Sigma in driving quality and efficiency. Explore its principles and benefits for organizational success.
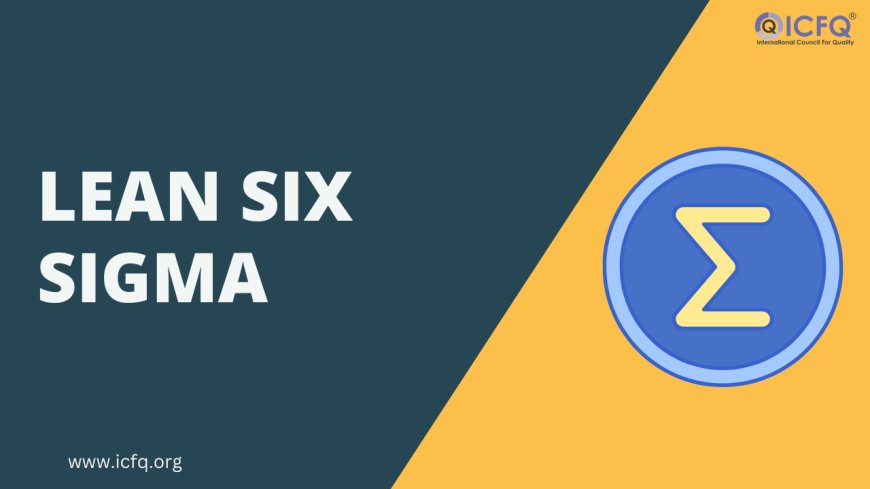
Lean Six Sigma is a method that helps organizations improve their processes by reducing waste and minimizing defects. It combines two approaches: Lean, which cuts unnecessary steps to make processes smoother, and Six Sigma, which focuses on reducing errors and variations.
Using Lean Six Sigma, companies follow a structured approach called DMAIC: Define the problem, Measure key aspects, Analyze data to find root causes, Improve processes, and Control to sustain improvements. This method ensures businesses operate more efficiently, deliver higher quality products or services, and satisfy customers better. Lean Six Sigma fosters a culture of continuous improvement, where everyone contributes to making processes better, leading to long-term success for the organization.
Present Situation of Quality Management in All Sectors
In today's business world, quality management is a big deal. Companies in all kinds of industries are stepping up their game to deliver top-notch products and services while keeping their operations efficient. This is because customers expect nothing less than the best, and competition is fierce.
Industries like manufacturing, healthcare, finance, and technology are all-embracing quality management systems to raise the bar. They're using tools like ISO 9001 and Lean Six Sigma to tighten up their processes, monitor how well things are going, and find ways to make improvements. With competition going global and regulations getting stricter, quality has become a make-or-break factor for staying in business. And thanks to advancements in technology, companies now have even more tools at their disposal to track what's happening and make smart decisions to keep quality standards high.
Quality Issues Without Lean Six Sigma
Industries that don't use Lean Six Sigma often face persistent quality issues. These can include inconsistent processes leading to unreliable outcomes, wasted time and resources due to inefficient workflows, and frequent errors or defects in products or services, resulting in customer dissatisfaction and additional costs for rework. Without a structured approach to continuous improvement, businesses may struggle to address customer needs effectively and make informed decisions based on data, leading to ongoing challenges that impact competitiveness and success.
How can Lean Six Sigma be leveraged to enhance quality and streamline processes?
Lean Six Sigma can be leveraged to enhance quality and streamline processes through its structured methodology and focus on continuous improvement. Here's how:
-
Identifying and Defining Problems: Lean Six Sigma begins by clearly defining the problem or opportunity for improvement. This step ensures that efforts are targeted toward areas that will have the most significant impact on quality and efficiency.
-
Data-Driven Analysis: The methodology emphasizes the use of data and statistical analysis to understand process performance and identify root causes of defects or inefficiencies. By analyzing data, organizations can make informed decisions and prioritize improvement efforts effectively.
-
Process Optimization: Lean principles help eliminate waste and non-value-added activities from processes, making them more streamlined and efficient. This optimization results in reduced cycle times, lower costs, and improved overall productivity.
-
Standardization and Control: Lean Six Sigma emphasizes the importance of standardizing processes and implementing controls to sustain improvements over time. Organizations can ensure consistency and prevent deviations that could lead to quality issues by establishing standard operating procedures and control mechanisms.
-
Continuous Improvement Culture: One of the most significant benefits of Lean Six Sigma is its focus on fostering a culture of continuous improvement. By empowering employees to identify and implement small incremental changes, organizations can continuously enhance quality and efficiency, driving ongoing success and adaptation to changing market conditions.
Lean Six Sigma provides a systematic framework for enhancing the quality and streamlining processes by leveraging data-driven analysis, process optimization, standardization, and control, and fostering a culture of continuous improvement.
Efficiency Through Waste Elimination
Optimizing processes by eliminating waste and non-value-added activities is a cornerstone of Lean Six Sigma methodology. Waste, categorized into seven types such as overproduction, waiting, unnecessary transportation, excess inventory, unnecessary motion, defects, and over-processing, significantly contributes to inefficiencies and increased costs within organizations. By pinpointing and eradicating these wasteful activities, companies can streamline their operations, leading to improved efficiency and reduced expenditures.
Key metrics to monitor for ensuring ongoing success
Key metrics play a crucial role in monitoring ongoing success in any organization. Some important metrics to consider include:
-
Quality Metrics: These measure the quality of products or services delivered, such as defect rates, customer complaints, or customer satisfaction scores.
-
Financial Metrics: Financial indicators like revenue growth, profit margins, and return on investment (ROI) provide insights into the financial health and profitability of the organization.
-
Operational Metrics: Operational metrics, such as cycle time, throughput, and capacity utilization, track the efficiency and productivity of processes within the organization.
-
Customer Metrics: Customer-related metrics, including customer retention rates, Net Promoter Score (NPS), and customer lifetime value (CLV), gauge customer loyalty and satisfaction levels.
-
Employee Metrics: Employee engagement, turnover rates, and productivity metrics help assess the organization's ability to attract, retain, and motivate talent.
-
Compliance and Regulatory Metrics: These metrics track adherence to regulatory requirements and industry standards, ensuring legal compliance and mitigating risks.
-
Innovation Metrics: Metrics related to innovation, such as new product development cycle time or number of patents filed, measure the organization's ability to innovate and stay competitive.
Monitoring these key metrics allows organizations to track their performance, identify areas for improvement, and make data-driven decisions to ensure ongoing success and continuous improvement.
Mastering Lean Six Sigma offers numerous benefits for businesses. It leads to improved efficiency, reduced waste, and enhanced quality, resulting in cost savings and increased customer satisfaction. By adopting Lean Six Sigma practices, organizations can streamline processes, boost productivity, and drive continuous improvement. Embracing these methodologies fosters a culture of innovation and empowers employees to identify and solve problems proactively. Ultimately, integrating Lean Six Sigma into business operations lays the foundation for long-term success and sustainable growth in an ever-evolving market landscape.