Boost Efficiency with Lean Six Sigma
Discover how Lean Six Sigma methodologies enhance efficiency and streamline processes for optimal performance. Drive success with proven strategies.
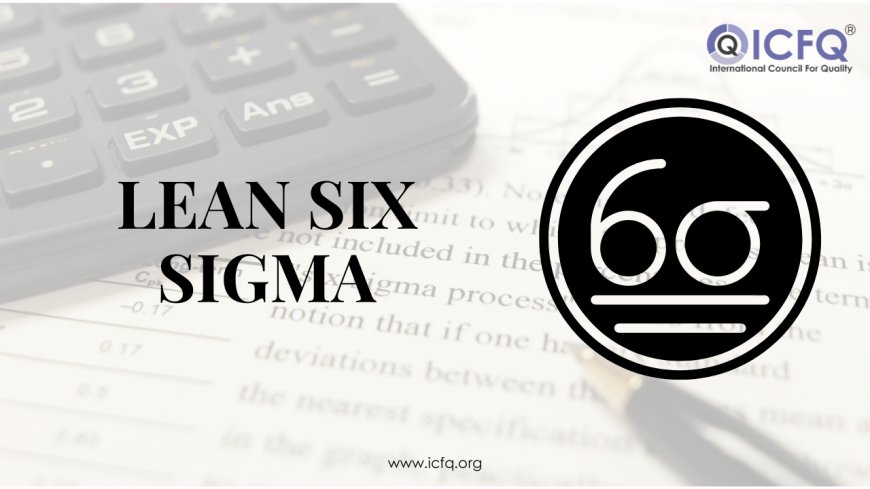
Introducing Lean Six Sigma combines two powerful methodologies: Lean and Six Sigma. Lean focuses on eliminating waste and optimizing processes for efficiency, while Six Sigma aims to reduce defects and variation to improve quality. Together, they create a holistic approach to process improvement. The synergy between Lean and Six Sigma lies in their complementary nature. Lean techniques identify and eliminate non-value-added activities, while Six Sigma tools ensure processes meet quality standards and reduce variation. This integration leads to streamlined operations, cost reduction, and enhanced customer satisfaction.
Efficiency improvement is central to Lean Six Sigma. By eliminating waste and reducing defects, organizations can achieve higher productivity and resource utilization. This not only improves operational efficiency but also enhances competitiveness in the market. Adopting Lean Six Sigma enables organizations to foster a culture of continuous improvement, driving sustainable growth and success.
Understanding the Principles of Lean Six Sigma
A. Lean Principles
-
Value Stream Mapping: This technique involves visually mapping out the steps in a process from beginning to end, including both value-added and non-value-added activities. It helps identify waste and opportunities for improvement by highlighting areas of inefficiency and bottlenecks.
-
Waste Reduction: Lean principles target various forms of waste, such as overproduction, waiting time, transportation, excess inventory, motion, overprocessing, and defects. By eliminating or minimizing these wastes, organizations can optimize their processes and improve efficiency.
-
Continuous Flow: This principle focuses on maintaining a steady and uninterrupted flow of work throughout the production process. It aims to eliminate batch processing and reduce cycle times, leading to smoother operations and reduced lead times.
-
Pull Systems: Pull systems operate based on customer demand, where production is triggered only when an order is received. This helps prevent overproduction and excess inventory while ensuring that resources are allocated efficiently to meet actual customer needs.
-
Kaizen (Continuous Improvement): Kaizen refers to the practice of continuous improvement, where small incremental changes are made to processes over time. It involves empowering employees at all levels to identify and implement improvements regularly, leading to a culture of continuous learning and innovation.
B. Six Sigma Principles
-
DMAIC Methodology: DMAIC stands for Define, Measure, Analyze, Improve, and Control. It's a structured approach used to solve problems and improve processes. It begins with defining the problem and ends with implementing sustainable solutions while ensuring control measures are in place to maintain improvements.
-
Data-Driven Decision Making: Six Sigma relies on data and statistical analysis to make informed decisions. Data is collected and analyzed to understand current process performance, identify root causes of issues, and validate improvement efforts.
-
Variability Reduction: Six Sigma aims to reduce variability in processes to achieve consistency and quality. By minimizing variation, organizations can produce products or deliver services that meet customer specifications more consistently.
-
Process Capability Analysis: This involves evaluating the ability of a process to meet customer requirements. Process capability analysis assesses whether a process is capable of producing outputs within specified tolerances and helps identify areas for improvement.
-
Customer Focus: Six Sigma places a strong emphasis on understanding and meeting customer needs and expectations. It involves gathering feedback from customers, understanding their requirements, and aligning process improvements with customer satisfaction goals.
How can Lean Six Sigma be effectively applied in practice?
This involves systematically identifying areas within a process where improvements can be made. Once identified, these opportunities are prioritized based on factors such as impact on customer satisfaction, cost reduction potential, and alignment with organizational goals. There are also some lean and Six Sigma tools and techniques, except for the factors that help in more effective practice:
Lean Tools and Techniques
-
5S (Sort, Set in Order, Shine, Standardize, Sustain): 5S is a methodology for organizing the workplace to improve efficiency and effectiveness. It involves sorting items, systematically organizing them, cleaning and maintaining the workspace, standardizing processes, and sustaining these improvements over time.
-
Kanban Systems: Kanban is a visual management tool used to control and manage the flow of work. It helps teams visualize their workflow, limit work in progress, and identify bottlenecks. By using visual signals, such as cards or boards, teams can ensure that work is pulled only when there is capacity to handle it.
-
Just-in-Time (JIT) Production: JIT is a strategy aimed at minimizing waste by producing goods only as needed, in the right quantity, and at the right time. It helps reduce inventory costs, lead times, and space requirements while improving responsiveness to customer demand.
-
Poka-Yoke (error proofing): Poka-Yoke involves designing processes or products in a way that prevents errors from occurring or makes them immediately visible and correctable. By implementing error-proofing mechanisms, organizations can reduce defects and improve overall quality.
Six Sigma Tools and Techniques
-
Statistical Analysis: It involves techniques like averages, standard deviations, and correlations to make sense of data. By understanding data patterns, teams can make informed decisions and pinpoint areas for improvement.
-
Root Cause Analysis: This method involves asking "why" multiple times to get to the bottom of a problem. It helps uncover the underlying reasons behind issues, allowing teams to address them effectively and prevent recurrence.
-
Control Charts: These charts track process performance over time, showing if variations are within acceptable limits. If there's a significant deviation, it signals a need for investigation and corrective action to keep processes on track.
-
Design of Experiments (DOE): DOE systematically tests different factors that could affect a process. By changing one factor at a time and observing the results, teams can identify which factors have the most impact on outcomes, helping optimize processes efficiently.
Leadership's Role in Lean Six Sigma
-
Commitment and Support from Leadership: Leadership plays a crucial role in the success of Lean Six Sigma by providing commitment and support to the initiative. This involves demonstrating belief in the methodology, allocating resources, and actively participating in improvement projects.
-
Creating a Culture of Continuous Improvement: Leaders should encourage a culture where everyone is encouraged to find ways to make things better. They can do this by being open to new ideas, encouraging learning from mistakes, and showing that improvement is valued.
-
Empowering Employees to Drive Change: Leaders should give employees the tools, authority, and encouragement to make changes in their work. This means providing training, trusting them to make decisions, and recognizing their contributions to improvement efforts. When employees feel empowered, they're more likely to take ownership of improvement projects and drive positive change.
Implementing Lean Six Sigma in a manufacturing company improved production efficiency by removing bottlenecks and streamlining workflows, reducing lead times, and enhancing product quality. In a service organization, involving frontline employees in the process led to practical solutions for improving customer service. Clear communication and leadership support were vital in overcoming resistance to change. These experiences highlight the importance of collaboration and communication in achieving successful Lean Six Sigma outcomes, resulting in efficiency improvements and better customer satisfaction.
How can Lean Six Sigma implementation be effective?
Effective Lean Six Sigma implementation is the successful application of Lean Six Sigma methodologies to improve processes, increase efficiency, and drive continuous improvement within an organization.
-
Start Small and Scale Up Begin by implementing Lean Six Sigma in smaller, manageable projects before expanding to larger initiatives. Starting small allows teams to learn and refine their skills while demonstrating early successes, and building momentum for larger improvements.
-
Involve cross-functional teams: Form teams with members from different departments or areas of expertise to bring diverse perspectives to problem-solving. Cross-functional collaboration ensures that all aspects of a process are considered and increases the likelihood of identifying innovative solutions.
-
Focus on Customer Value: Keep the customer at the center of improvement efforts by understanding their needs and expectations. Align process improvements with customer requirements to deliver value and enhance satisfaction.
-
Measure and Track Progress: Establish clear metrics to measure the effectiveness of Lean Six Sigma initiatives and track progress over time. Regularly monitoring performance allows teams to identify areas for improvement, celebrate successes, and make informed decisions to drive continuous improvement.
We've discussed key aspects of Lean Six Sigma, highlighting the importance of leadership support, employee empowerment, and the use of tools like DMAIC and 5S. These elements are essential for successful implementation, enabling organizations to achieve efficiency improvements. Embracing Lean Six Sigma methodology offers significant benefits, including cost reduction, improved quality, and enhanced customer satisfaction. By adopting this approach, organizations can unlock their potential for continuous improvement and maintain competitiveness in today's market. Efficiency enhancement remains central to Lean Six Sigma, allowing organizations to streamline processes, reduce waste, and optimize resource utilization. By focusing on efficiency improvement efforts, organizations can drive productivity, profitability, and sustainable growth in the long term.