Boost Your Business with Six Sigma
Boost your business efficiency and performance with Six Sigma methodologies for process improvement and quality management.
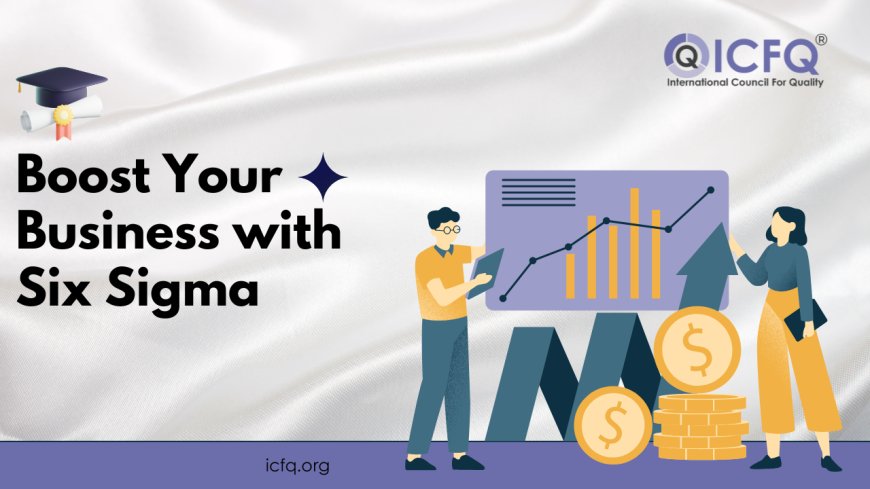
In today's business climate, efficiency and quality are essential for success. Across industries, companies strive to streamline operations, improve product or service quality, and reduce costs. Heightened customer expectations, globalization, and rapid technological advancements drive this. Businesses must continuously innovate and adapt to remain competitive. From manufacturing to healthcare, finance, and retail, the need to optimize operations and enhance quality is universal. Achieving this requires a strategic approach, leveraging technology and data-driven insights to drive efficiency and deliver value to customers.
Organizations must focus on efficient processes, effective resource management, and customer-centric strategies to thrive in this environment. By prioritizing efficiency and quality, companies can meet customer demands, outperform competitors, and drive growth. Embracing innovation and fostering a culture of continuous improvement is key to staying ahead in today's competitive landscape. By doing so, businesses can position themselves for long-term success and sustainable growth in the ever-evolving market.
What is Six Sigma and its main goals?
Six Sigma is a methodology aimed at improving business processes by minimizing defects and reducing variation. Its core objectives revolve around achieving near-perfect performance by systematically identifying, analyzing, and eliminating errors or inefficiencies. By focusing on statistical analysis and data-driven decision-making, Six Sigma aims to ensure that processes operate within specified limits and consistently meet customer requirements. Its ultimate goal is to drive continuous improvement and deliver products or services that exceed customer expectations while minimizing waste and maximizing efficiency. Through rigorous problem-solving techniques and the implementation of standardized processes, Six Sigma helps organizations achieve higher levels of quality, reliability, and customer satisfaction.
Common process improvement pitfalls
Process improvements often need to be addressed, including inconsistent execution, difficulties in measuring outcomes, and slow adaptation to market changes. Inconsistent execution means improvements aren't applied consistently, leading to uneven results. Without clear outcomes to measure progress, it's hard to know if improvements are effective. Slow adaptation to market changes means processes may not keep up with shifting customer needs or competitive landscapes. Overcoming these challenges requires clear communication, consistent implementation, and a willingness to adapt to evolving circumstances.
How can Six Sigma improve business performance and competitiveness?
Six Sigma stands as a pivotal force in enhancing business performance and competitiveness by offering a systematic approach to process improvement. Through its methodology, it targets defects and variations within processes, driving efficiency gains, waste reduction, and heightened product or service quality. This structured implementation equips organizations with the necessary tools to achieve superior operational outcomes, elevate customer satisfaction levels, and secure a competitive edge in the market.
Moreover, Six Sigma instills a culture of continual advancement and data-driven decision-making across all organizational tiers. Promoting active employee involvement in process enhancement initiatives cultivates collaboration, engagement, and innovation. Additionally, Six Sigma empowers businesses to grasp customer needs and preferences, enabling the delivery of offerings that meet and exceed expectations. Six Sigma catalyzes heightened performance, efficiency, and customer satisfaction, solidifying organizational leadership within industries and bolstering competitive standing in the marketplace.
Six Sigma's Unique Benefits
Six Sigma stands out from other quality improvement methods by relying on data-driven decision-making and statistical analysis. Instead of subjective opinions, it uses precise statistical tools to identify and measure variations in processes, pinpointing the root causes of defects. This approach ensures that organizations make informed decisions and prioritize improvement efforts effectively.
Moreover, Six Sigma follows a structured problem-solving approach, such as the DMAIC (Define, Measure, Analyze, Improve, Control) methodology. This systematic framework guides improvement projects from start to finish, ensuring that changes are implemented efficiently and consistently. As a result, businesses experience tangible benefits like increased efficiency, reduced defects, and improved customer satisfaction. By providing a reliable method for continuous improvement grounded in data and analysis, Six Sigma empowers businesses to drive meaningful change and achieve long-term success.
Exploring Six Sigma
To begin implementing Six Sigma, businesses can start by providing training for staff, selecting appropriate projects, and setting realistic improvement goals. By embracing Six Sigma principles and methodologies, organizations can embark on a journey of continuous improvement and achieve sustainable success. The DMAIC (Define, Measure, Analyze, Improve, Control) methodology guides Six Sigma projects, ensuring a systematic approach to process improvement. Each step, from defining project goals to implementing control measures, contributes to measurable enhancements in operational efficiency and quality.
Benefits of Implementing Six Sigma
-
Reduced Operational Costs: Six Sigma identifies and eliminates inefficiencies, leading to cost savings through waste reduction and resource optimization.
-
Heightened Customer Satisfaction: By enhancing product or service quality, Six Sigma ensures consistent delivery, resulting in increased customer satisfaction and loyalty.
-
Improved Regulatory Compliance: Six Sigma's systematic approach aligns processes with regulatory standards, reducing the risk of non-compliance and associated penalties.
-
Increased Employee Engagement: Six Sigma fosters a culture of continuous improvement, empowering employees to contribute to organizational success and boosting morale and retention.
-
Methodical Approach: Six Sigma's DMAIC methodology provides a structured framework for process improvement, ensuring changes are based on data-driven insights and deliver measurable results.
Integrating Six Sigma with Other Business Strategies
Six Sigma can work well with other business strategies like Lean methodologies and ISO certifications to improve overall business performance. Lean methods focus on cutting waste and boosting efficiency, while Six Sigma reduces variation and enhances quality by fixing defects. Using these strategies together can improve process speed and accuracy. Also, aligning Six Sigma with ISO certifications helps standardize processes and meet international quality standards, improving competitiveness in global markets. Integrating these approaches not only results in better overall improvements but also supports more sustainable business practices by ingraining quality and efficiency into the company's culture.
Sustaining Six Sigma Gains and Quality Culture
Measuring Success in Six Sigma Projects
Setting measurable goals is crucial in Six Sigma projects to quantify the effectiveness of the initiatives. Typical metrics to track include reduction in process cycle times, cost savings, and improvements in product quality. By establishing clear, quantifiable targets at the outset, organizations can monitor progress and make adjustments as needed, ensuring that the Six Sigma projects deliver tangible benefits. Measuring these outcomes helps validate the investment in Six Sigma and demonstrates the value added to the business.
Sustaining Improvements and Fostering a Culture of Quality
To sustain the improvements achieved through Six Sigma, it's important to embed the methodology deeply into the company's culture. This includes regular training sessions, revisiting key Six Sigma projects periodically, and encouraging all employees to think in terms of continuous improvement. Organizations should also recognize and reward improvements to motivate staff and maintain momentum. By fostering a culture that values quality and efficiency, companies can ensure that the gains from Six Sigma initiatives are maintained over the long term and continue to drive the business forward.
Six Sigma offers unique advantages in enhancing business efficiency and quality through its structured approach to process improvement. By adopting Six Sigma as a strategic framework, businesses can achieve not only short-term improvements but also long-term operational excellence. For those interested in delving deeper into Six Sigma, exploring certifications and training resources can provide valuable insights and knowledge to support successful implementation.