Understanding Quality Management through Six Sigma
Explore the principles of Quality Management through Six Sigma. Understand its methodologies and benefits for efficient processes.
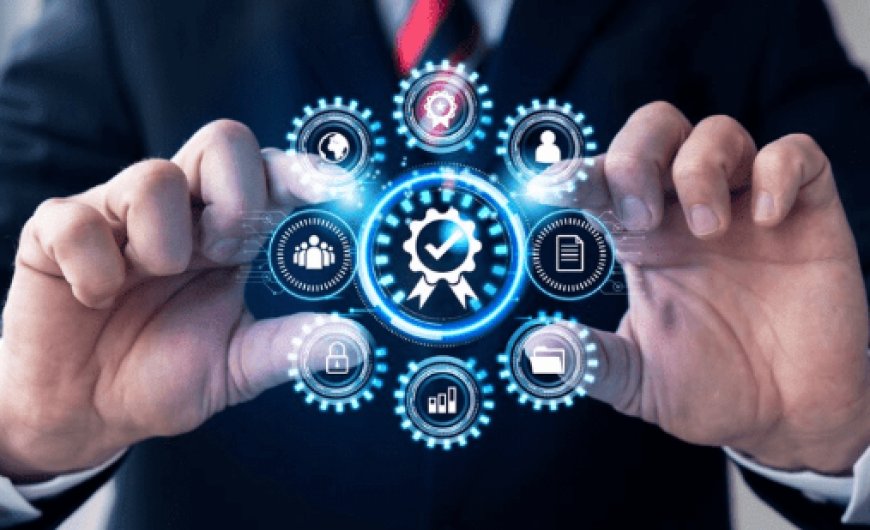
Six Sigma is a renowned methodology used in quality management to enhance process efficiency, reduce defects, and improve overall business performance. It focuses on minimizing variability and ensuring consistency in processes to meet customer requirements and enhance overall quality. It originated at Motorola in the 1980s and has since been adopted by numerous organizations across various industries. The term "Six Sigma" refers to a statistical measure of process performance, aiming to achieve an extremely low defect rate.
By employing statistical tools and methodologies, Six Sigma helps identify areas for improvement, optimize processes, and enhance customer satisfaction. It fosters a culture of continuous improvement, with a focus on data-driven decision-making and customer-centricity. Ultimately, Six Sigma plays a pivotal role in driving organizational excellence and achieving competitive advantage in today's dynamic business environment.
What is Six Sigma?
Six Sigma is a systematic approach to process improvement that aims to minimize defects and errors in products or services. It originated at Motorola in the 1980s and has since been widely adopted by companies across various industries. The term "Six Sigma" refers to a statistical measure of process performance, aiming to achieve an extremely low defect rate—approximately 3.4 defects per million opportunities.
At its core, Six Sigma focuses on identifying and eliminating causes of variation in processes to enhance efficiency, reduce costs, and improve customer satisfaction. It employs a structured methodology, data-driven decision-making, and statistical tools to achieve these goals.
Key Principles of Six Sigma:
-
Customer Focus: Six Sigma places a strong emphasis on understanding and meeting customer needs and expectations. It aims to deliver products or services that consistently meet or exceed customer requirements.
-
Data-Driven Decision-Making: Decisions within Six Sigma are based on factual analysis of data rather than intuition or guesswork. Data is collected, analyzed, and used to drive process improvements and problem-solving.
-
Process Improvement: Six Sigma seeks to continuously improve processes by identifying and eliminating sources of variation, defects, and inefficiencies. It follows a structured approach to problem-solving and process optimization.
-
Employee Involvement: Six Sigma encourages the active involvement and engagement of employees at all levels of the organization. Employees are trained in Six Sigma methodologies and empowered to contribute to process improvement initiatives.
-
Management Leadership: Leadership support and commitment are essential for the success of Six Sigma initiatives. Management provides direction, resources, and support to ensure that Six Sigma goals are achieved.
DMAIC Methodology:
The DMAIC (Define, Measure, Analyze, Improve, and Control) methodology is a structured problem-solving approach used to improve existing processes within an organization.
-
In the Define phase, teams establish the project's goals, objectives, and scope. They identify stakeholders and gather information about customer requirements, ensuring alignment with organizational objectives. This phase lays the groundwork for the entire improvement initiative by defining critical-to-quality characteristics and setting the stage for data collection and analysis.
-
The Measure phase involves collecting relevant data to quantify the current state of the process. Teams determine process capability and performance metrics, identifying key process inputs (X) and outputs (Y) to measure. Through data collection and analysis, they gain insights into process performance and variability, laying the foundation for subsequent analysis and improvement efforts.
-
During the Analyze phase, teams delve deep into the collected data to identify patterns, trends, and root causes of defects or inefficiencies. They utilize statistical tools such as Pareto charts, histograms, and scatter plots to understand process variation and identify potential sources of problems. This phase is critical for pinpointing the underlying causes of process issues, enabling teams to develop effective solutions.
-
In the Improve phase, teams develop and implement solutions to address the root causes identified during the analysis phase. They test potential solutions using pilot studies or experiments, optimizing process parameters to achieve desired outcomes. Continuous improvement is emphasized, with teams seeking innovative solutions to drive significant enhancements in process performance and efficiency.
-
The Control phase focuses on establishing controls to monitor process performance and sustain improvements over time. Teams develop standard operating procedures (SOPs) and control plans to ensure consistency and reliability in process execution. By implementing visual management tools and mistake-proofing techniques, teams prevent regression and ensure that improvements are maintained.
DMADV Methodology:
The DMADV (Define, Measure, Analyze, Design, and Verify) methodology is used to design new processes or products that meet customer needs and achieve Six Sigma levels of quality.
-
In the Define phase, clearly define project goals, objectives, and customer requirements for the new process or product. They identify stakeholders and gather information about customer needs and expectations, ensuring alignment with organizational objectives. Critical-to-quality characteristics and design specifications are established to guide the development process.
-
During the Measure phase, gather data on customer requirements, market trends, and industry standards. Through market research, customer surveys, and benchmarking, teams gain insights into customer preferences and expectations. Performance metrics and benchmarks are established to assess the success of the new process or product.
-
In the Analyze phase, analyze collected data to identify critical factors for success and design parameters. Utilizing tools such as Quality Function Deployment (QFD) and Failure Mode and Effects Analysis (FMEA), teams assess risks and prioritize design features based on their impact on customer satisfaction and organizational objectives.
-
The Design phase involves developing and designing the new process or product based on customer requirements and critical factors identified during the analysis phase. Using tools such as computer-aided design (CAD) and simulation, teams create prototypes and validate designs to ensure they meet performance specifications. Design features are optimized to maximize performance and minimize defects.
-
In the Verify phase, validate the designed solution through testing, prototyping, and simulation. Pilot runs or trials are conducted to assess performance under real-world conditions, and feedback from stakeholders and customers is obtained to ensure the solution meets their needs and expectations. By rigorously verifying the solution, teams ensure that it achieves the desired results and delivers value to the organization and its customers.
Is Six Sigma suitable for your business?
The decision to adopt Six Sigma should be based on a thorough assessment of your business's needs, culture, resources, and potential benefits. If your business is facing quality or process challenges and is committed to continuous improvement, Six Sigma could be a valuable tool for driving positive change and achieving operational excellence.
There are several reasons why companies choose to implement Six Sigma:
-
Quality Improvement: Six Sigma focuses on reducing defects and errors in processes, leading to improved product or service quality. If your business is struggling with quality issues or customer complaints, Six Sigma can help address these concerns.
-
Cost Reduction: By streamlining processes and eliminating waste, Six Sigma can lead to cost savings for your business. This can result from reduced rework, lower inventory levels, and increased operational efficiency.
-
Customer Satisfaction: Six Sigma emphasizes understanding and meeting customer requirements. By delivering products or services that meet or exceed customer expectations, your business can enhance customer satisfaction and loyalty.
-
Data-Driven Decision Making: Six Sigma relies on data and statistical analysis to identify the root causes of problems and make informed decisions. If your business values data-driven decision-making and continuous improvement, Six Sigma provides a structured approach to achieving these goals.
-
Competitive Advantage: Implementing Six Sigma can give your business a competitive edge in the marketplace. By consistently delivering high-quality products or services at lower costs, your business can differentiate itself from competitors and attract more customers.
Six Sigma implementation roles
Six Sigma implementation involves various roles within an organization, each contributing to the success of the initiative.
-
Executive Leadership: Executive leaders are the guiding force behind Six Sigma implementation within an organization. They offer direction and support by assigning resources, defining strategic objectives, and ensuring that Six Sigma efforts align with the organization's broader goals. The commitment of executive leadership is vital for the success of Six Sigma initiatives, as their involvement sets the tone for the entire organization and reinforces the importance of continuous improvement.
-
Champions: Champions are senior leaders who take charge of Six Sigma efforts within their departments or areas. They guide their teams, offering advice and support along the way, and they're always ready to step in and remove any obstacles that might come up. One of their most important tasks is deciding which projects to focus on and making sure everyone understands why they're important.
-
Master Black Belts (MBBs): The highly experienced Six Sigma experts who contribute significantly to the implementation process. They coach, mentor, and provide technical expertise to Black and Green Belts. MBBs lead complex projects, facilitate training sessions, and ensure consistency in Six Sigma implementation across the organization. Their strategic insights often influence decision-making related to Six Sigma initiatives.
-
Black Belts: Black Belts serve as project leaders, executing Six Sigma projects from start to finish. They leverage Six Sigma methodologies and tools to identify and solve process problems, reduce defects, and improve efficiency. Leading cross-functional teams, analyzing data, and implementing solutions are all part of their responsibilities, ultimately aiming to achieve project goals and deliver measurable results.
-
Green Belts: Green Belts, though working part-time on Six Sigma projects, play a valuable role within their departments or areas. They support Black Belts in project execution, data collection, analysis, and implementation of process improvements. Trained in Six Sigma methodologies and tools, Green Belts contribute to driving continuous improvement and enhancing overall efficiency within their respective roles.
-
Project Sponsors: Project sponsors, whether senior leaders or stakeholders, provide critical support for specific Six Sigma projects. They ensure alignment with organizational objectives, allocate resources and remove barriers to project success. Additionally, project sponsors champion the project's importance, securing buy-in from stakeholders and ensuring successful project outcomes.
-
Subject Matter Experts (SMEs): It bring specialized knowledge and expertise relevant to specific Six Sigma projects. They provide technical guidance, insights, and data necessary for project analysis and solution development. Collaborating closely with Black Belts and Green Belts, SMEs ensure that solutions are practical, effective, and aligned with the organization's business needs.
-
Agents: They are responsible for driving organizational change and promoting a culture of continuous improvement. They communicate the benefits of Six Sigma, facilitate training sessions, and encourage employee engagement in improvement initiatives. Overcoming resistance to change and ensuring the integration of Six Sigma principles into daily operations are key responsibilities for change agents.
Six Sigma offers a powerful approach to improving quality management within organizations. By focusing on reducing defects, streamlining processes, and enhancing customer satisfaction, Six Sigma helps businesses achieve operational excellence and competitive advantage. Embracing Six Sigma principles can lead to significant improvements in efficiency, cost reduction, and overall business performance. As businesses strive for excellence in today's competitive landscape, adopting Six Sigma methodologies can be a strategic investment in driving sustainable growth and success.