A Beginner's Guide to Lean Six Sigma
Discover the essentials of Lean Six Sigma with our beginner's guide. Learn key concepts, methodologies, and tools for process improvement.
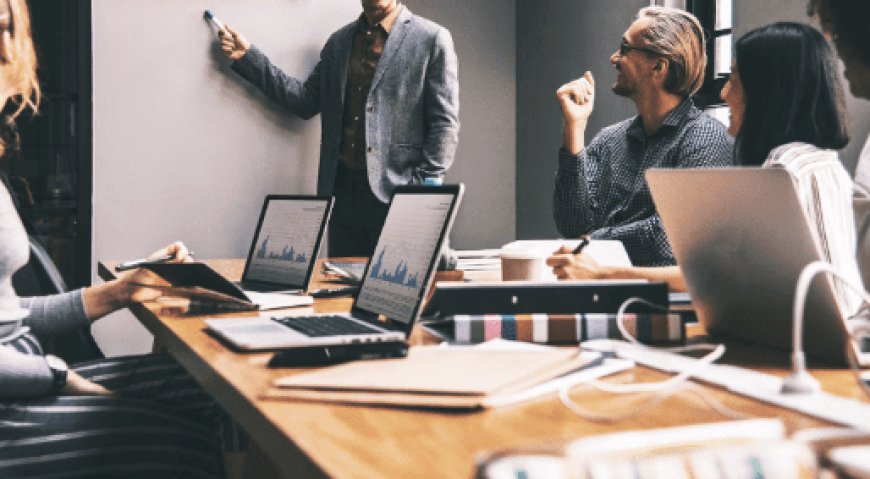
Lean Six Sigma is a method used by businesses to make their operations better. It combines two strategies: Lean, which is about cutting waste, and Six Sigma, which is about making processes more precise. Lean focuses on getting rid of unnecessary steps and things that waste time and resources. Six Sigma is all about making processes work better by reducing mistakes and variations. Together, they help businesses work more efficiently and deliver better-quality products or services.
Nowadays, businesses need to be efficient and deliver high-quality results in today’s competitive world. Lean Six Sigma helps them do this by finding and fixing problems in their processes. It's a way for businesses to stay ahead by working smarter, not harder.
Understanding Lean Principles
Lean is a method used by businesses to do things more efficiently. It's about cutting out anything that doesn't add value to the customer and making processes run smoother.
Key principles of lean:
-
Value: This means focusing on what the customer wants and is willing to pay for. Anything else is considered waste and should be eliminated.
-
Value Stream: This is the sequence of steps that a product or service goes through from start to finish. Understanding and optimizing this flow is crucial for efficiency.
-
Flow: Once you know the value stream, you want to make sure things move through it smoothly and without delays. This involves organizing work in a way that minimizes interruptions and waiting times.
-
Pull: Instead of making things in anticipation of demand, Lean encourages producing only what is needed when it's needed. This helps prevent overproduction and excess inventory.
-
Continuous Improvement (Kaizen): Lean is all about getting better over time. It's about constantly looking for ways to improve processes, even if they seem to be working well already. This mindset of continuous learning and refinement is essential for success in learning.
Delving into Six Sigma
Six Sigma is a structured approach used by businesses to enhance the quality of their processes by minimizing defects and variations. It aims to achieve near-perfectness in the products or services delivered to customers.
Key principles of Six Sigma:
-
Define: This initial phase involves clearly defining the problem and the project goals, as well as understanding customer requirements and expectations.
-
Measure: In this phase, data related to the problem is collected and analyzed to quantify the extent of the issue and establish a baseline for improvement.
-
Analyze: Through statistical tools and techniques, the causes of defects or variations in the process are identified and prioritized to focus efforts on the most significant factors.
-
Improve: Solutions to address the identified causes are developed and implemented. These solutions are tested on a small scale before being fully deployed to ensure effectiveness.
-
Control: Once improvements are implemented, control measures are established to monitor the process and ensure that the gains achieved are sustained over time. This phase involves setting up ongoing monitoring systems and implementing corrective actions as needed to maintain performance.
How do Lean and Six Sigma complement each other?
Lean and Six Sigma work together to improve processes in different ways. Lean focuses on reducing waste and streamlining operations, while Six Sigma targets reducing defects and variations. Combining these methods allows businesses to tackle both efficiency and quality issues comprehensively. Lean helps identify and eliminate non-value-added activities, making processes smoother and faster, while Six Sigma ensures that the remaining steps are performed with minimal errors and consistent results.
Benefits of Lean and Six Sigma methodologies:
Cost Savings:
Lean principles aim to identify and eliminate non-value-added activities, reducing costs associated with overproduction, waiting times, and excess inventory. Conversely, Six Sigma methodologies focus on minimizing defects and errors, resulting in significant cost savings by reducing rework, scrap, and warranty claims.
Improved Profitability:
Streamlining processes and minimizing waste through lean practices enhance operational efficiency, leading to increased productivity and profitability for businesses. Meanwhile, Six Sigma ensures processes are performed with minimal variations, resulting in higher-quality products or services that meet customer expectations and reduce costs associated with defects and rework.
Enhanced customer satisfaction:
Lean principles such as flow and pull ensure timely delivery of products or services, contributing to enhanced customer satisfaction and loyalty. Furthermore, by reducing defects and errors, businesses can consistently deliver products or services that meet or exceed customer requirements, leading to improved satisfaction and retention rates.
Culture of Continuous Improvement:
Integrating Lean and Six Sigma fosters a culture of continuous improvement and innovation within organizations. This integration encourages employees at all levels to participate in identifying and solving problems. Both methodologies rely on data and metrics to drive improvements, empowering employees to make informed decisions based on evidence and analysis, thereby sustaining the culture of continuous improvement.
Tools and Techniques:
Overview of Lean Tools:
5S is like giving your workspace a makeover for better efficiency and safety. It involves five steps: sorting out what you need and don't need, logically organizing everything, cleaning up to keep things tidy, setting standards for how things should be done, and making sure these improvements stick around. Value stream mapping is like drawing a map of how things flow in a process. It helps find areas where things get stuck or wasted, so you can make changes to make everything run smoother.
Overview of Six Sigma Tools:
DMAIC is a five-step method for solving problems and making processes better. It starts by defining the problem and then measuring it to understand how bad it is. Next, it analyzes why the problem is happening, improves the process, and sets up controls to keep things on track. Root-cause analysis is like finding the main reason behind a problem. It helps figure out why things go wrong in a process so that targeted solutions can be applied to prevent them from happening again.
Examples of how these tools are applied in real-life scenarios:
-
Lean tools like 5S can be applied in a manufacturing plant to organize workstations and reduce time spent searching for tools or materials, leading to increased productivity.
-
Six Sigma's DMAIC approach can be used in a healthcare setting to reduce patient waiting times by identifying bottlenecks in the appointment scheduling process and implementing improvements to streamline the process.
Common Difficulties and Solutions
Identifying common challenges in implementing Lean Six Sigma:
When introducing Lean Six Sigma, challenges may include resistance to change, difficulty prioritizing projects, and insufficient support from leaders or resources. Maintaining improvements over time and ensuring everyone stays engaged can also be ongoing hurdles.
Strategies for overcoming obstacles:
To address resistance, involve employees early, provide training, and provide clear communication about the benefits. Prioritize projects based on strategic goals and use data to pinpoint areas for improvement. Gain leadership support for resources and remove barriers. Maintain improvements through consistent monitoring and foster engagement with regular communication and recognition. Establishing a culture that values problem-solving and innovation at all levels helps sustain Lean Six Sigma efforts effectively.
Lean Six Sigma, is a method for making processes better by cutting waste and reducing errors. By applying Lean principles and Six Sigma tools, businesses can save costs, improve quality, and keep customers happy. Despite challenges, like resistance to change, proactive strategies can help overcome obstacles. I encourage you to explore Lean Six Sigma further and consider how it could benefit your organization. Embracing continuous improvement can lead to greater success in today's competitive world.