The Role of DMAIC in Six Sigma
DMAIC in Six Sigma improves processes by defining, measuring, analyzing, improving, and controlling workflows for better efficiency and quality management.
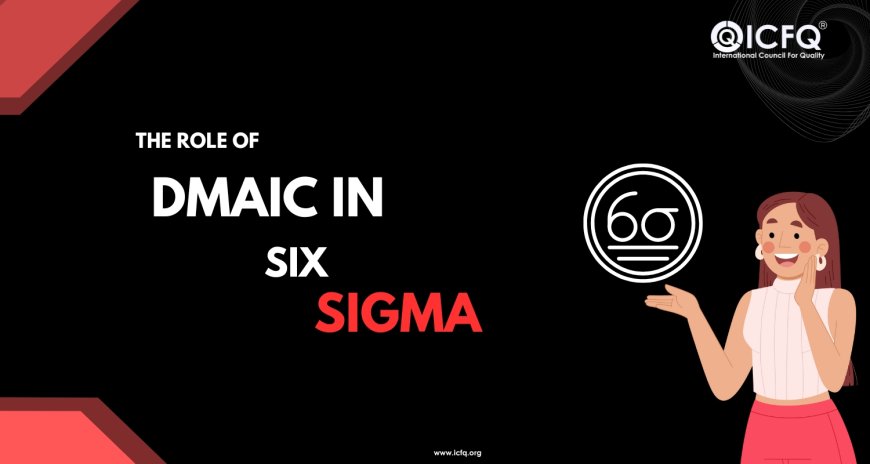
In Six Sigma, there's a cool method called DMAIC that helps make things better. DMAIC stands for Define, Measure, Analyze, Improve, and Control. It's like a roadmap that guides people in making processes smoother and fixing mistakes. Six Sigma started in factories but now it's used in lots of other areas like hospitals, banks, and tech companies. DMAIC helps them find problems, see how things are going now, figure out why problems happen, make things better, and make sure they stay better.
People who learn Six Sigma, from beginners to experts, learn all about DMAIC and other important Six Sigma stuff. They take classes, either in a classroom or online, to learn how to use DMAIC to fix problems at work. Companies want to be good at what they do and make customers happy. That's why knowing about DMAIC in Six Sigma is so important. When companies use DMAIC, they can save money, do better work, and make everyone happier.
Understanding DMAIC in Six Sigma for Better Process Improvement
Making things better, Six Sigma is a big deal. It's a way of fixing problems and making stuff good. DMAIC is a special way Six Sigma does this: Define, Measure, Analyze, Improve, and Control. However, figuring out how to use DMAIC in Six Sigma can be tricky. Six Sigma is all about using numbers and facts to make things work better. It helps companies make their stuff good and fix any mistakes. If you want to learn Six Sigma, you start with a Green Belt. But getting good at DMAIC needs more than just knowing the theory. You have to practice and understand how companies work.
People can learn about Six Sigma in classes or online. There are different levels, like Green Belt and Black Belt, to help people get better at fixing things. Some courses mix Six Sigma with another method called Lean to make it even better. As companies try to be good at what they do, knowing DMAIC in Six Sigma is super important. It helps them find and fix problems smartly.
Complications of Improving Processes with DMAIC in Six Sigma
Improving how things work, like with DMAIC in Six Sigma, sounds great. It means things run smoother and everyone's happier. But it's not always easy. Let's look at some problems that can pop up:
1. People Don't Like Change: We're creatures of habit. Changing how things are done can upset folks used to the old way. To fix this, we need good plans for change, clear talk, and a culture that likes getting better.
2. Bad Data Messes Things Up: DMAIC needs good data to work right. If the info we use is wrong or old, it can lead us the wrong way. So, we need to make sure our data is good from the start.
3. Projects Grow Too Big: We start small, but things can get out of hand fast. This means more work, more time, and losing focus. We need to watch out and keep things in check.
4. Leaders Need to Be Onboard: If bosses aren't into it, our projects might not go far. They need to help, give us what we need, and show they're serious about change.
5. Teams Don't Talk: In big places, teams don't always work together. This makes fixing things hard. We need to break down walls and share info.
6. Outside Stuff Messes With Plans: Things outside our control, like laws changing or new tech, can mess up our plans. We need to be ready to change course fast.
7. Keeping Things Good Long-Term is Hard: Getting better is cool, but it's hard to keep it up. We need to keep an eye on things and make improvements stick.
Improving how things work with DMAIC in Six Sigma is a good idea. But it's not easy. We must be ready for problems and work hard to improve things for the long haul.
How can companies use DMAIC in Six Sigma to be more successful?
DMAIC is like a step-by-step plan that helps companies make things better. Here's how they can do it:
1. Start by figuring out exactly what needs fixing (Define).
2. Measure how things are right now to see where improvements can be made (Measure).
3. Look closely at the data to find out why things aren't working as well as they could (Analyze).
4. Come up with solutions to make things better (Improve).
5. Put measures in place to make sure things stay better over time (Control).
By following this plan, companies can find and fix problems, make things run smoother, and be more successful overall.
Understanding DMAIC in Six Sigma
When it comes to improving things at work, Six Sigma is a method that works. And at the heart of Six Sigma is something called DMAIC. It's like a step-by-step plan to fix problems and make things run smoother in a company. Let's break down each part of DMAIC and see how it helps in Six Sigma.
1. Define: First off, we need to know exactly what the problem is and how big it is. We do this by figuring out what the customers want, setting goals, and getting a team together to work on it. This helps everyone know what they're aiming for.
2. Measure: Next, we measure how things are going right now. We use tools to gather data and see how well the process is working. This helps us know where we stand and what needs to change.
3. Analyze: Once we have the data, we dig in to find out why things aren't working perfectly. We use different tools to figure out what's causing the problems. This helps us focus on the most important things to fix.
4. Improve: Now it's time to try out some solutions. We come up with ideas, test them out, and see what works best. This step helps us make things better.
5. Control: Finally, we make sure the improvements stick. We set up rules and checks to keep things running smoothly in the long run. This step helps us keep up the good work.
By using DMAIC in Six Sigma, companies can find and fix problems, which leads to better quality, lower costs, and happier customers. But it's not just about following steps it's about using data, learning as we go, and working together to make things better. So, if you want to be great at Six Sigma, mastering DMAIC is the way to go.
DMAIC in Six Sigma is a go-to method for improving things in all sorts of businesses. It's a step-by-step way to find problems, figure out why they're happening, fix them, and make sure they stay fixed. By using data and special tools, DMAIC helps companies make their processes smoother, make fewer mistakes, and make customers happier. It's not just about fixing things once—DMAIC helps teams keep getting better and better at what they do. DMAIC works so well that it's become a must-have for making sure everything runs smoothly in Six Sigma.