How to Use Six Sigma Tools in Your Business
Boost your business with Six Sigma Tools! Discover how to make your operations smoother and better. Start improving now!
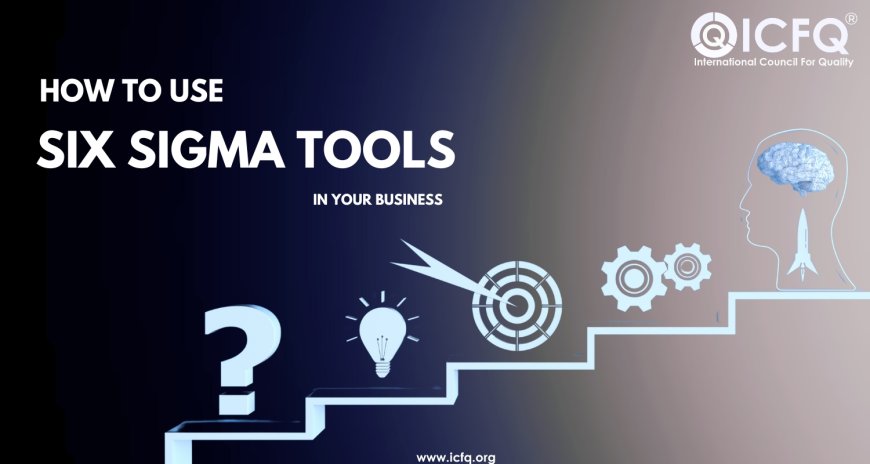
Making things work better and keeping quality high is super important for lasting success. One great way to do this is by using Six Sigma tools. These tools help you fix problems, make things smoother, and make customers happier. Six Sigma is like a big toolbox full of ways to make your business run better. It's all about using data to make smart choices and always trying to get better. Whether you're just starting with Six Sigma or you're already using it, these tools can help.
You can learn about Six Sigma in different ways, like taking courses or getting certified. There are different levels of certification, like Green Belt, Black Belt, and Yellow Belt, depending on how much you know and what you do in your job. Some people even become Master Black Belts, which means they're skilled at leading Six Sigma projects.
There are lots of ways to learn about Six Sigma, from classes to online courses. Getting certified doesn't just help you; it also makes your whole team better at improving things all the time. Talk about how Six Sigma tools can make your business work better. We'll share easy tips on how to use these tools to save time, cut waste, and make everything run smoother, no matter what kind of business you have.
Understand Your Business with Six Sigma Tools
Companies are always looking for ways to do better. That's where Six Sigma tools come in. They're like a super helpful toolkit for making your business run smoother and more successful. First off, let's talk about what Six Sigma is all about. It's a set of tricks and techniques for making things work better. Companies send their workers to Six Sigma classes so they can learn all these cool tricks. Once they're done, they can become certified at different levels, like Green Belt or Black Belt, which means they're experts at fixing things that aren't working right.
One of the best things about Six Sigma tools is that they're all about using data to make decisions. Instead of just guessing, you look at the numbers and figure out what's going wrong. Then, you can come up with a plan to make things better. Another cool thing is that Six Sigma plays well with other improvement methods, like Lean Six Sigma. It's like mixing two powerful potions to make an even better one. By combining them, businesses can get rid of waste and make everything run smoother. And guess what? You don't even have to leave your house to learn about Six Sigma anymore! There are lots of online classes you can take. That means no matter where you are in the world, you can become a Six Sigma expert and help your company succeed.
Overcoming Operational Challenges with Six Sigma Tools
When it comes to making things run smoother and better in a business, Six Sigma tools are like a guide. They promise to help fix problems and make everything work more efficiently. But underneath all that promise, there are some tricky parts that companies have to deal with to make Six Sigma work for them. Let's take a closer look at these challenges.
1. Change is Hard: People don't always like changing the way they do things. When a company tries to introduce Six Sigma tools, employees might resist because they're used to doing things the old way. It takes good communication and a plan to help everyone understand why the change is important.
2. Data Troubles: Six Sigma relies on using data to make decisions. But sometimes, the data isn't perfect. It might be missing or wrong, which makes it hard to trust. Without good data, Six Sigma tools can't do their job properly.
3. Changing Culture: Making Six Sigma work means changing the culture of a company. Everyone needs to be on board with always trying to do better. But if a company is used to doing things a certain way, it can be tough to get everyone to embrace a new way of thinking.
4. Tools Can Be Tricky: Six Sigma tools are powerful, but they're not always easy to use. If people don't understand how to use them right, they might end up with the wrong answers. Training and support are important to help everyone get the hang of using these tools correctly.
5. Not Enough Resources: Doing Six Sigma takes time and money. If a company doesn't have enough resources, it can be hard to make it work. This is especially true for smaller companies or ones that don't have a lot of money to spare.
6. Keeping the Changes: Once a company starts using Six Sigma tools and makes things better, they need to keep it up. If they don't keep an eye on things, they might slip back into old habits. Making Six Sigma a part of everyday work helps make sure the changes stick around.
Using Six Sigma tools can help a company do better, but it's not always easy. By facing these challenges and learning how to use Six Sigma tools the right way, companies can make big improvements and stay ahead of the game.
How can businesses make good use of Six Sigma Tools?
Businesses can use Six Sigma Tools effectively by first understanding their processes well and finding areas they can make better. Then, they need to pick the right tools, like DMAIC or DFSS, depending on what they need to improve. It's important to train employees on how to use these tools properly so everyone's on the same page. Also, setting clear goals and ways to measure progress helps a lot. Regular check-ins and reviews are necessary to keep things on track and fix any problems. By using Six Sigma Tools, businesses can get better at what they do, make customers happier, and waste less time and resources.
Implementing Six Sigma Tools for Success
Companies are always looking for ways to do things better, faster, and with fewer mistakes. That's where Six Sigma tools come in. They're like a set of strategies and techniques for making sure everything runs smoothly and without errors. Let's break down how you can use Six Sigma tools to make your business more successful:
1. Identify the Problem: The first step is figuring out what needs fixing. Use tools like the SIPOC diagram and process maps to get a clear picture of where things are going wrong.
2. Measure Performance: Once you know what's wrong, you need to figure out how bad it is. Six Sigma tools like statistical process control charts and data collection plans help you measure how well things are working and where there's room for improvement.
3. Find the Cause: Next, you need to figure out why things are going wrong. Tools like cause-and-effect diagrams and Pareto charts help you dig deep and find the root causes of problems.
4. Fix the Problem: Once you know what's causing the issues, it's time to fix them. Use tools like brainstorming and control plans to come up with solutions and put them into action.
5. Keep Things on Track: Finally, you need to make sure things stay fixed. Use tools like control charts and performance dashboards to monitor how things are going and make adjustments as needed.
Here are some key Six Sigma tools you can use:
1. DMAIC: This is a step-by-step method for solving problems and improving processes.
2. SIPOC Diagram: This is a simple chart that shows how inputs turn into outputs in a process.
3. Pareto Chart: This is a bar graph that helps you figure out which problems are the most important to fix first.
4. Control Charts: These are graphs that help you keep track of how well a process is working over time.
5. FMEA: This is a tool for identifying and preventing potential problems before they happen.
Using Six Sigma tools in your business plan can make things better. It helps you work more efficiently, make higher-quality stuff, and keep your customers happier. How? Well, by following a method called DMAIC and using tools like process maps, stats, and finding the root cause of problems. This approach helps tidy up how things are done, cut down on mistakes, and make everything work as smoothly as possible. And because Six Sigma focuses on always getting better, it helps teams find and fix problems, leading to long-term success and staying ahead of the competition.