Implementing Six Sigma in Operations Management for Efficiency
Implementing Six Sigma in operations management streamlines processes, eliminates defects, and fosters continuous improvement, driving sustainable success and efficiency.
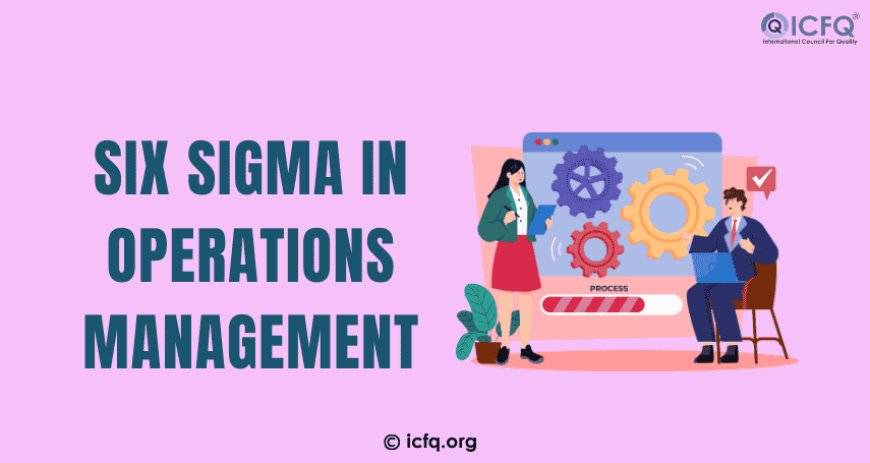
As an expert in operations management, I believe Six Sigma is one of the most powerful methodologies available for driving operational excellence. The core of Six Sigma is its data-driven approach, focusing on reducing variation and eliminating defects, which directly enhances process efficiency. By integrating the DMAIC framework (Define, Measure, Analyze, Improve, Control), organizations can identify and address inefficiencies at their root cause, leading to sustainable improvements.
In my experience, when Six Sigma is properly implemented, it not only boosts quality but also fosters a culture of continuous improvement. It aligns teams towards common goals, enabling them to make data-backed decisions rather than relying on intuition. This leads to better resource allocation, cost reductions, and ultimately, an increase in customer satisfaction.
Understanding Six Sigma and Its Role in Operations Management
Six Sigma is a data-driven methodology that improves processes by identifying and eliminating defects and variations. It enhances efficiency, reduces waste, and ensures consistent quality, helping organizations meet customer expectations and drive continuous improvement for better performance and satisfaction.
In operations management, Six Sigma helps organizations streamline their processes, improve production timelines, and eliminate inefficiencies. By using data and statistical analysis, businesses can identify performance gaps, make data-driven decisions, and foster a culture of continuous improvement. Implementing Six Sigma in operations management ensures that companies not only meet but exceed customer expectations.
The Key Benefits of Implementing Six Sigma in Operations Management
Adopting Six Sigma in operations management offers several key benefits that can significantly impact business performance. Below are some of the major advantages:
-
Reduced Defects and Variability: Six Sigma focuses on eliminating process defects, reducing variability, and ensuring consistent product quality. This leads to a reduction in errors and rework, which translates to cost savings and higher customer satisfaction.
-
Improved Efficiency: By optimizing processes, organizations can reduce waste, streamline workflows, and enhance resource utilization. This leads to better productivity, faster delivery times, and improved bottom-line performance.
-
Data-Driven Decision Making: Six Sigma empowers businesses to make decisions based on accurate data and statistical analysis, eliminating guesswork and subjective assumptions. This results in more informed and effective management strategies.
-
Enhanced customer satisfaction: When products and services meet or exceed customer expectations, businesses gain a competitive edge. By focusing on process improvement, Six Sigma helps ensure that quality is maintained throughout production, enhancing customer loyalty.
The DMAIC Methodology: A Framework for Six Sigma Success
The DMAIC (Define, Measure, Analyze, Improve, Control) methodology is at the heart of Six Sigma. It provides a structured approach to solving problems and driving improvements in operations management.
The DMAIC methodology is a key framework in Six Sigma for continuous improvement. It consists of five phases:
-
Define: Identify the problem, set goals, and define project scope and stakeholders.
-
Measure: Collect data to assess current performance and identify areas for improvement.
-
Analyze: Examine the data to find the root causes of issues and inefficiencies.
-
Improve: Develop and implement solutions to eliminate root causes and optimize processes.
-
Control: Monitor the improved process to ensure sustained performance and prevent regression
Integrating Six Sigma with Lean Principles for Enhanced Operations
While Six Sigma focuses on reducing defects and variability, Lean methodology is centered around eliminating waste and optimizing resource utilization. By integrating Six Sigma with Lean principles, organizations can create a more powerful approach to operations management. This combined methodology, often referred to as Lean Six Sigma, helps businesses achieve both high-quality output and streamlined processes.
The integration of Six Sigma and Lean helps organizations:
-
Eliminate Waste: Lean focuses on eliminating non-value-added activities in the production process, such as excess inventory, waiting times, and unnecessary movement. Combining Lean with Six Sigma ensures that both inefficiency and defects are addressed simultaneously.
-
Maximize Value: By improving process quality and reducing waste, Lean Six Sigma enables businesses to deliver more value to customers while minimizing costs.
-
Foster Continuous Improvement: Both methodologies promote a culture of ongoing improvements. By continually refining processes, organizations can maintain a competitive edge and adapt to changing market conditions.
The Role of Six Sigma Green Belts and Black Belts in Operations Management
To successfully implement Six Sigma in operations management, it is crucial to have qualified professionals with the necessary expertise. Six Sigma certifications, such as Green Belts and Black Belts, are essential for guiding improvement projects and driving process optimization.
-
Six Sigma Green Belt: Green Belts are typically individuals who are trained in the fundamentals of Six Sigma and play a key role in smaller improvement projects. They assist in data collection, analysis, and the implementation of improvements. Green Belts works alongside Black Belts to ensure that projects stay on track and deliver results.
-
Six Sigma Black Belt: Black Belts are experts in Six Sigma methodologies and lead larger, more complex improvement projects. They are responsible for managing teams, driving change, and overseeing the implementation of process improvements. Black Belts possess advanced statistical knowledge and are highly skilled in problem-solving techniques.
The collaboration between Green Belts and Black Belts is essential for the successful application of Six Sigma in operations management. Their combined efforts ensure that projects are executed efficiently and that desired outcomes are achieved.
Overcoming Challenges When Implementing Six Sigma in Operations Management
While Six Sigma offers tremendous benefits, organizations may face several challenges when implementing it in operations management. Common obstacles include:
-
Resistance to Change: Employees may resist process changes, especially if they feel their roles or workflows will be disrupted. Overcoming resistance requires strong leadership, clear communication, and training to ensure that everyone understands the benefits of Six Sigma.
-
Lack of Data: Six Sigma is a data-driven methodology, and its success depends on accurate and reliable data. Organizations that lack proper data collection systems may struggle to implement Six Sigma effectively.
-
Resource Constraints: Implementing Six Sigma projects requires time, effort, and resources. Small or resource-constrained businesses may find it challenging to allocate the necessary resources to Six Sigma initiatives.
Six Sigma improves operations by reducing defects, optimizing processes, and fostering continuous improvement through the DMAIC framework. Integrating lean principles further enhances efficiency. The expertise of Green Belts and Black Belts ensures successful implementation while addressing challenges like resistance and data limitations. Ultimately, Six Sigma drives better performance, customer satisfaction, and a competitive edge.