The Power of Lean Six Sigma in Process Improvement
Discover the transformative power of Lean Six Sigma for efficient process improvement. Streamline operations, reduce waste, and enhance productivity.
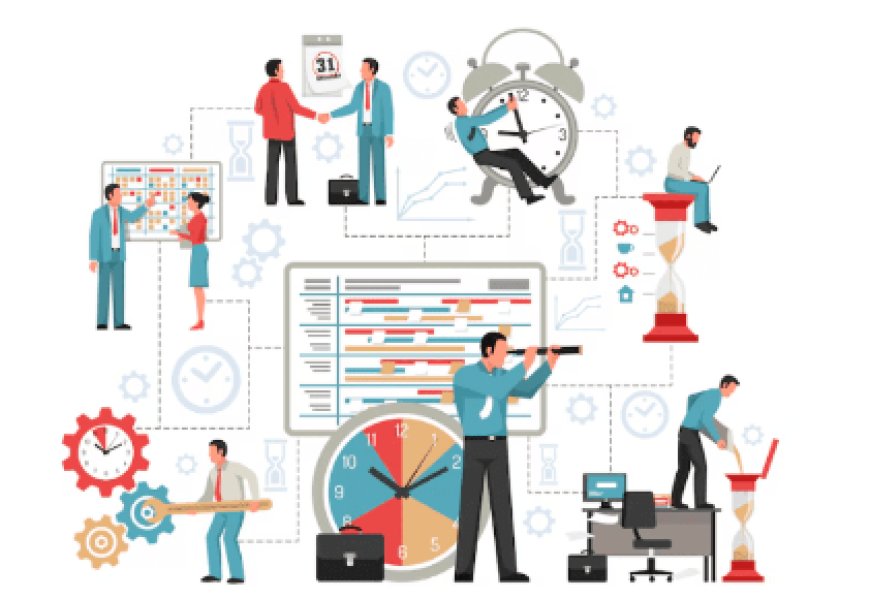
Efficient processes are crucial for organizational success as they streamline operations, reduce waste, and enhance productivity. By optimizing processes, businesses can deliver products or services more quickly, leading to increased customer satisfaction and loyalty. Efficient processes also contribute to cost savings by minimizing resources wasted on unnecessary steps or errors, thereby improving profitability.
Lean Six Sigma is a methodology that combines principles from lean manufacturing and Six Sigma to achieve process improvement. Lean focuses on eliminating waste and maximizing value, while Six Sigma emphasizes reducing defects and variations. Together, they provide a comprehensive approach to identifying inefficiencies, analyzing root causes, and implementing solutions. By applying Lean Six Sigma principles, organizations can achieve significant improvements in quality, efficiency, and customer satisfaction, ultimately driving organizational success.
Understanding Lean Six Sigma
Lean Six Sigma is a methodology combining lean principles and Six Sigma Strategies to streamline processes and improve quality. Lean originated from Toyota's manufacturing system, focusing on eliminating waste to enhance efficiency. Its key principles include identifying and eliminating non-value-added activities, optimizing flow, and fostering continuous improvement. Six Sigma, originating from Motorola and popularized by General Electric, targets reducing variation to enhance quality and consistency. Its core concepts involve defining, measuring, analyzing, improving, and controlling processes to minimize defects and enhance customer satisfaction.
Integrating Lean and Six Sigma is like combining two powerful tools to make things better. Lean helps cut out waste and make processes smoother, while Six Sigma makes sure things are consistent and of high quality by reducing mistakes. When you put these together, you can improve both how efficiently things run and how well they work. This means happier customers and better performance overall. By using Lean to get rid of unnecessary steps and Six Sigma to make sure everything stays on track, organizations can make lasting improvements that make them more competitive and profitable.
The DMAIC Methodology
The DMAIC method in Six Sigma guides process improvement in five steps: Define, Measure, Analyze, Improve, and Control. First, Define set project goals. Measure gathers data on the current process. Analyze and dig into the data to find issues. Improve, implement solutions, and Control ensure changes stick. Each step uses specific tools: Define uses project charters; Measure employs process maps; Analyze uses cause-and-effect diagrams; Improve relies on brainstorming; and Control uses control charts. This method helps organizations fix problems, boost efficiency, and maintain progress over time.
Benefits of Lean Six Sigma in Process Improvement
-
Efficiency improvements: Lean Six Sigma identifies and eliminates waste in processes, including overproduction, waiting times, unnecessary transportation, excess inventory, unnecessary motion, defects, and underutilized talent. By streamlining workflows and removing non-value-added activities, processes become more efficient, reducing lead times, and increasing throughput.
-
Quality enhancements: Six Sigma focuses on reducing process variation to achieve consistent and predictable outcomes. By using statistical tools and techniques, it identifies the root causes of defects and errors, allowing organizations to implement targeted improvements. This results in higher quality products or services, fewer defects, and increased customer satisfaction.
-
Cost savings and increased profitability: Lean Six Sigma's focus on efficiency and quality directly impacts the bottom line. By eliminating waste and reducing defects, organizations can reduce operating costs, lower rework expenses, and optimize resource utilization. This leads to increased profitability and a competitive edge in the market.
-
Enhanced customer satisfaction: Lean Six Sigma ensures that processes are designed and optimized to meet customer requirements. By delivering products or services with fewer defects, shorter lead times, and consistent quality, organizations can exceed customer expectations, leading to higher satisfaction levels, increased loyalty, and positive word-of-mouth referrals.
Case Study and Examples
Lean Six Sigma has been successfully applied across various industries. For example, in manufacturing, companies like Toyota and General Electric use it to improve production and quality. Healthcare organizations like the Mayo Clinic and Virginia Mason Medical Center use it to enhance patient care and reduce wait times. Even in services, companies like American Express and Bank of America used Lean Six Sigma to improve customer service and satisfaction. These examples show how Lean Six Sigma can make processes better in different areas, from making cars to providing healthcare and banking services.
Lean Six Sigma Certification
Lean Six Sigma certification offers various levels of expertise, including Yellow Belt, Green Belt, and Black Belt. Yellow Belt certification introduces basic concepts and terminology, while Green Belt certification delves deeper into problem-solving methodologies and statistical tools. Black Belt certification signifies mastery in leading complex projects, statistical analysis, and mentoring teams in Lean Six Sigma methodologies.
Obtaining Lean Six Sigma certification benefits professionals by enhancing their problem-solving skills, boosting career prospects, and increasing earning potential. For organizations, certified professionals contribute to improved process efficiency, reduced waste, and enhanced quality. Additionally, certified individuals can drive cultural change by promoting a data-driven approach to decision-making and fostering a continuous improvement mindset throughout the organization. Overall, Lean Six Sigma certification serves as a valuable asset for both professionals seeking career advancement and organizations striving for operational excellence.
Barriers and Considerations
Implementing Lean Six Sigma can face challenges like resistance to change and a lack of leadership support. Strategies for success include effective change management, engaging stakeholders, and clear communication. Training and support for employees, along with fostering a culture of improvement, are crucial. To ensure lasting improvement, organizations need to regularly monitor progress, review performance, and adapt processes as necessary. Continuous learning and feedback from stakeholders are key to long-term success.
We've seen how Lean Six Sigma can shake up how things work for the better. It gives people the tools to solve problems, makes processes run smoother, and even changes how companies do things. By focusing on cutting waste, fixing mistakes, and always getting better, Lean Six Sigma helps companies do their best work. It's not just for factories either; it works in healthcare, services, and more. So, if your organization wants to be sharper, more efficient, and more successful, Lean Six Sigma is worth checking out. It's a game-changer that can open up new opportunities and take your operations to the next level.