How Six Sigma Boosts Quality Management
Discover how Six Sigma methodology enhances quality management, streamlines processes, and reduces defects for improved efficiency and customer satisfaction.
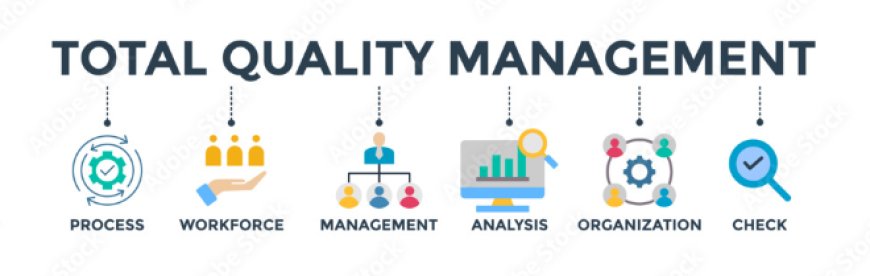
Quality management is like the backbone of a business in today's competitive world. It's all about making sure that what a company offers, whether it's a product or a service, meets the mark. When things are done right the first time, it saves time and money, which are both crucial to staying ahead of the game. Plus, happy customers mean repeat business and good word of mouth, which are invaluable in a crowded market.
Without quality management, businesses risk falling behind or losing out to competitors who prioritize consistency and excellence. It's not just about meeting standards; it's about exceeding them and costantly finding ways to improve. By focusing on quality, businesses can build trust, save resources, and keep up with the ever-changing demands of the market.
Traditional Quality Management Limitations
Traditional quality management methods, while effective to some extent, often fall short of addressing the complexities of modern business environments. One major limitation lies in their static nature. These methods tend to focus on fixing problems as they arise rather than preventing them in the first place. This reactive approach can lead to increased costs as resources are diverted to resolving issues rather than investing in proactive measures.
Moreover, traditional quality management methods may struggle to adapt to rapidly changing markets and technologies. They often rely heavily on manual processes and paperwork, which can be time-consuming and prone to errors. In today's dynamic landscape, where innovation and agility are key to staying competitive, these outdated methods can hinder rather than facilitate progress
What is Six Sigma, and How Does It Improve Quality?
Six Sigma is a systematic methodology aimed at improving the quality of processes by reducing defects and variations. It relies on data-driven decision-making and statistical tools to identify and eliminate errors and inefficiencies. By emphasizing precise measurement and analysis, Six Sigma helps organizations achieve consistent and near-perfect performance in their operations.
Here's how it improves quality:
-
Reduces Variation: Six Sigma identifies sources of variation in processes, whether they are related to manufacturing, service delivery, or administrative tasks. By minimizing these variations, Six Sigma ensures consistency in outputs, leading to higher-quality products or services.
-
Data-Driven Decision Making: Data analysis is at the core of Six Sigma. It uses statistical tools and techniques to collect, analyze, and interpret data, enabling organizations to identify root causes of defects or inefficiencies accurately. This data-driven approach helps in making informed decisions about process improvements.
-
Process Improvement: Six Sigma emphasizes process improvement through a structured approach known as DMAIC (Define, Measure, Analyze, Improve, and Control). This methodology guides organizations through the steps of defining project goals, measuring current process performance, analyzing data to identify areas for improvement, implementing solutions, and establishing controls to sustain improvements over time.
-
Customer-centric: One of the central tenets of Six Sigma is understanding and meeting customer needs. By focusing on customer requirements and feedback, organizations can ensure that their products or services align closely with market demands, thereby enhancing customer satisfaction and loyalty.
-
Cross-Functional Collaboration: Six Sigma encourages collaboration across different departments or functional areas within an organization. By involving individuals with diverse expertise and perspectives, Six Sigma fosters a culture of teamwork and shared responsibility for quality improvement initiatives.
-
Standardization: Standardization is another key aspect of Six Sigma. By establishing standardized procedures and practices, organizations can reduce errors, eliminate waste, and enhance predictability in outcomes. This standardization also facilitates continuous improvement efforts by providing a baseline for measuring progress and identifying further opportunities for enhancement.
Importance of data-driven decision-making and statistical tools
Data-driven decision-making and statistical tools play a crucial role in Six Sigma by providing objective insights and guiding improvement efforts. These tools enable organizations to analyze large datasets to identify patterns, trends, and areas for improvement accurately. By relying on data rather than intuition or guesswork, Six Sigma ensures that decisions are grounded in evidence, leading to more effective outcomes.
Statistical tools within Six Sigma, such as histograms, control charts, and regression analysis, help organizations understand the root causes of defects and variations in processes. This understanding allows for targeted interventions to address underlying issues systematically. By using statistical methods to measure process performance and quantify improvement opportunities, Six Sigma enables organizations to prioritize initiatives and allocate resources effectively.
Real-life examples of organizations benefiting from Six Sigma
Walmart is a prime example of Six Sigma's success. By implementing Six Sigma techniques in its supply chain management, Walmart significantly reduced costs and improved efficiency. This enabled Walmart to offer lower prices to customers while maintaining quality, ultimately solidifying its position as a retail giant
Another example is Amazon. Through Six Sigma, Amazon streamlined its fulfillment processes, resulting in faster delivery times and higher customer satisfaction. This contributed to Amazon's reputation as a leader in e-commerce and helped fuel its exponential growth. Healthcare organizations like the Mayo Clinic have also seen notable benefits from Six Sigma implementation. By focusing on reducing medical errors and improving patient care processes, Mayo Clinic has enhanced patient outcomes and operational efficiency, positioning itself as a top-tier healthcare provider.
How can businesses effectively address quality management challenges?
Businesses can effectively address quality management challenges through proactive measures and systematic approaches:
-
Clear Quality Objectives: Establish measurable goals to guide quality improvement efforts and ensure alignment throughout the organization.
-
Robust Processes: Develop standardized procedures and workflows to maintain consistency and reliability in delivering products or services.
-
Employee Training: Provide comprehensive training to empower employees with the skills and knowledge needed to identify and address quality issues effectively.
-
Utilize Quality Tools: Implement methodologies like Six Sigma, Lean, or Total Quality Management to systematically identify and eliminate root causes of quality issues.
-
Customer Feedback: Actively solicit and listen to customer feedback to understand their needs and preferences, enabling adjustments to products or services accordingly.
-
Performance Monitoring: Regularly track key quality metrics to detect deviations and take corrective actions promptly, ensuring continuous improvement.
Six Sigma in driving organizational success
Six Sigma plays a pivotal role in driving organizational success by focusing on improving processes, reducing defects, and enhancing efficiency. Six Sigma helps organizations deliver consistent quality and value to customers by systematically identifying and eliminating sources of variation and waste.
Through its data-driven approach and rigorous methodology, Six Sigma enables organizations to make informed decisions and prioritize initiatives that have the most significant impact on performance. This not only leads to cost savings but also fosters a culture of continuous improvement and innovation.
Moreover, Six Sigma enhances customer satisfaction by ensuring products and services meet or exceed expectations. Satisfied customers are more likely to remain loyal and recommend the organization to others, thereby contributing to long-term success and growth.
Six Sigma is like a roadmap for businesses to improve how they work. Focusing on using data to make decisions, making processes better, and always trying to get a little bit better, helps companies make fewer mistakes and waste less time and resources.
With Six Sigma, teams work smarter, not harder, to fix problems and make sure things run smoothly. This means happier customers, more efficient operations, and staying ahead of the competition. It's not about being perfect, but about always striving to be better, step by step. So, Six Sigma isn't just a tool; it's a mindset that helps businesses thrive in today's fast-paced world.