The Path of Six Sigma Management
Learn about Six Sigma Management, a method that uses data to improve business processes, enhance quality, and increase efficiency.
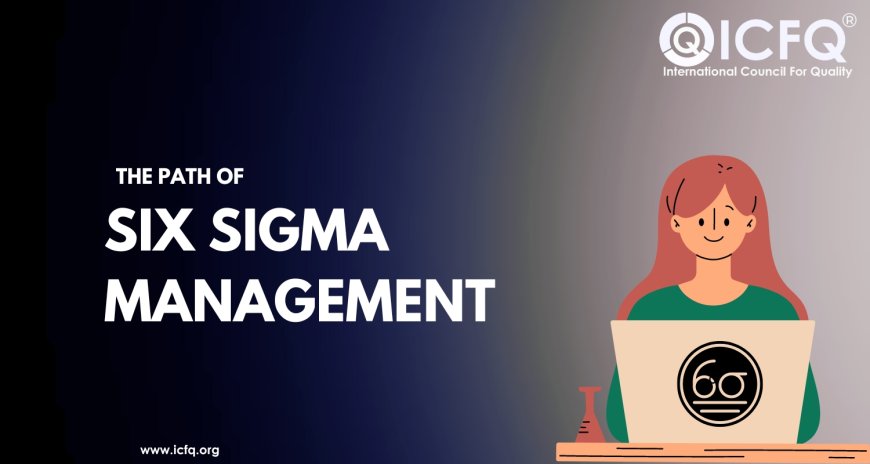
Quality management is crucial as companies aim to meet customer expectations and stay competitive. Effective quality management ensures products and services meet high standards, leading to customer satisfaction and loyalty.
Six Sigma is a popular method for improving quality and reducing defects. It focuses on identifying and eliminating errors and variations in business processes using data-driven techniques and statistical analysis. By following Six Sigma, companies can streamline operations, reduce waste, and improve efficiency. This leads to better products, lower costs, and increased competitiveness. Adopting quality management practices like Six Sigma helps businesses maintain high standards, improve performance, and achieve long-term success in a changing market.
Understanding Six Sigma and Lean Principles
Six Sigma and Lean principles are two methodologies aimed at improving business processes, but they focus on different aspects.
Six Sigma
It focuses on reducing defects and variations in processes by using statistical methods and data analysis. Its goal is to achieve near-perfect quality by identifying and eliminating the root causes of defects and minimizing variability in manufacturing and business processes.
Lean Principles focus on eliminating waste and improving flow within processes. Waste can be anything that does not add value from the customer’s perspective, such as excess inventory, unnecessary steps, or long wait times. Lean aims to streamline processes, improve efficiency, and deliver value to customers more quickly.
Lean Six Sigma
Lean Six Sigma combines the strengths of both methodologies. It integrates the waste-reduction focus of Lean with the defect-reduction focus of Six Sigma. By doing so, Lean Six Sigma aims to improve process efficiency and quality simultaneously.
-
Efficiency and Quality: Lean Six Sigma seeks to improve both efficiency and quality by eliminating waste and reducing defects.
-
Customer Focus: Both methodologies prioritize delivering value to the customer by ensuring high-quality products and efficient services.
-
Data-Driven: Lean Six Sigma uses data and statistical analysis to identify problems and implement solutions.
-
Continuous Improvement: Lean Six Sigma encourages a culture of continuous improvement, where employees at all levels are involved in finding and implementing process improvements.
Organizations Struggle with Implementing Six Sigma
Many organizations face difficulties when implementing Six Sigma due to several common challenges. One major issue is resistance to change. Employees may be reluctant to adopt new processes or technologies, especially if they do not understand the benefits or feel uncertain about the changes. Overcoming this resistance requires effective communication and training to ensure everyone understands the purpose and advantages of Six Sigma.
Another significant challenge is the lack of leadership support. Successful implementation of Six Sigma requires commitment from top management. With strong support from leaders, it is easier to allocate the necessary resources and maintain momentum. Additionally, sustaining improvements can be challenging. Organizations may find it hard to keep up with the initial improvements and integrate them into everyday practices. Consistent monitoring, ongoing training, and a focus on continuous improvement are essential to overcome these challenges and ensure long-term success with Six Sigma.
Tools and Techniques in Six Sigma Projects
Six Sigma projects use various tools and techniques to analyze and improve processes. These tools help teams find problems, understand how processes work, and make effective changes.
-
Process Mapping shows the steps in a process. It helps identify inefficiencies and areas for improvement by providing a clear view of the workflow.
-
Statistical Analysis involves using data to make decisions. Tools like regression analysis, hypothesis testing, and ANOVA help understand relationships between different factors and determine the importance of changes. This helps in understanding how well a process is working and finding the causes of problems.
-
Root Cause Analysis (RCA), including methods like the 5 Whys and Fishbone (Ishikawa) diagrams, helps find the main causes of problems. By repeatedly asking "why" a problem occurs, teams can identify and fix the root cause instead of just dealing with the symptoms.
-
Control Charts track how a process performs over time. These charts help identify normal variations in the process and unusual changes caused by external factors. This helps maintain control over the process and ensure improvements last.
These tools and techniques help Six Sigma teams systematically analyze processes, find improvement opportunities, and make effective changes, leading to better quality and efficiency in the organization.
Benefits of Six Sigma for Organizations
Six Sigma provides several benefits for organizations by improving processes and eliminating defects. These advantages lead to better quality, reduced costs, and higher customer satisfaction. Here are the key benefits:
-
Improved Quality: Six Sigma helps identify and eliminate defects in products and services, leading to higher quality outputs and fewer errors.
-
Reduced Costs: By streamlining processes and reducing waste, Six Sigma lowers operational costs, making the organization more cost-efficient.
-
Increased Customer Satisfaction: Consistently delivering high-quality products and services enhances customer satisfaction and loyalty.
-
Enhanced Efficiency: Optimizing processes results in faster production times and more efficient service delivery, improving overall productivity.
-
Better Decision Making: Six Sigma uses data-driven methods to make well-informed decisions, helping to address and solve problems effectively.
-
Employee Engagement: Involving employees in Six Sigma projects boost their engagement and satisfaction, as they contribute to meaningful improvements.
-
Competitive Advantage: Improved performance and reliability through Six Sigma strengthen the organization’s competitive position in the market, making it more attractive to customers and stakeholders.
Six Sigma's Role in Continuous Improvement
Six Sigma helps promote continuous improvement and excellence in organizations. Here’s how it works:
-
Structured Methodology: Six Sigma uses a structured approach called DMAIC (Define, Measure, Analyze, Improve, Control) to solve problems. This helps teams find issues, understand root causes, and create effective solutions.
-
Data-Driven Decisions: Six Sigma relies on data and statistical analysis to make decisions. This helps organizations measure performance, identify areas to improve, and track the results of changes.
-
Focus on Quality: Six Sigma aims to reduce defects and variability in processes, leading to higher-quality products and services. This helps meet customer expectations and build a reliable reputation.
-
Employee Involvement: Six Sigma involves employees at all levels in the improvement process. Training employees in Six Sigma methods empowers them to contribute to problem-solving and process improvement, fostering a culture of continuous learning.
-
Sustainable Improvements: Six Sigma ensures that improvements are not only made but also maintained over time. The Control phase of DMAIC helps keep improvements in place and prevents backsliding.
-
Customer Satisfaction: Continuous improvement with Six Sigma leads to better quality, efficiency, and consistency, which enhances customer satisfaction. Happy customers are more likely to stay loyal and recommend the organization to others.
Six Sigma supports continuous improvement by offering a structured, data-driven way to improve quality and efficiency. It involves employees, focuses on customer needs, and ensures lasting improvements, helping organizations succeed in a competitive and changing environment.
Sx Sigma management uses the DMAIC method to reduce defects and improve process quality with data-driven decisions. It offers benefits like better quality, lower costs, increased efficiency, and higher customer satisfaction. However, challenges include resistance to change and the need for strong leadership. Organizations should use Six Sigma practices to continuously improve and achieve operational excellence, helping them stay competitive and meet market demands.