How Does Six Sigma DMAIC Work
Discover how Six Sigma DMAIC works to improve processes and reduce defects. Learn the step-by-step approach of Define, Measure, Analyze, Improve, and Control.
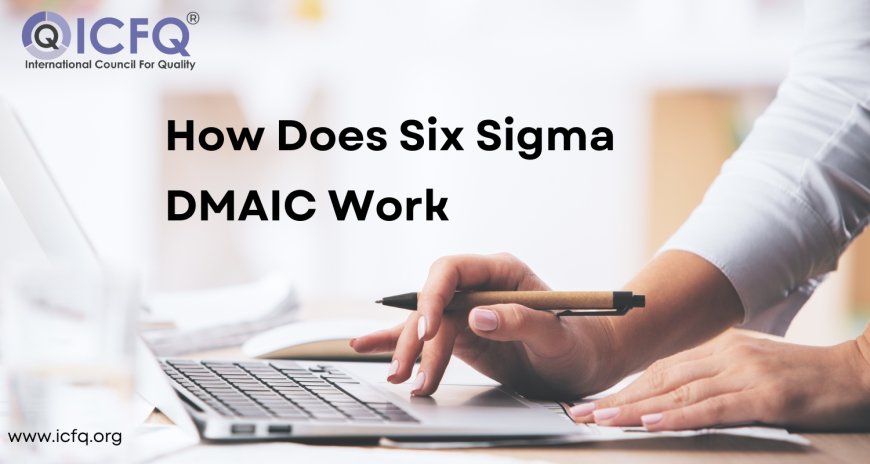
Six Sigma DMAIC(Define, Measure, Analyze, Improve, Control) is a method used to make processes better in a company. It combines math with a step-by-step way to find and fix problems or inefficiencies. In the Define step, the project's goals and what it includes are written down, and important people are identified. This makes sure everyone knows what the project wants to do and that it matches the company's goals. Next, in the Measure step, the current process performance is checked using data. This means gathering the right information to see how well things are going and to find out how big the problem or opportunity is.
The Analyze step looks closely at the reasons behind the problems found in the Measure step. Math tools are used to look at data and find out what's causing the issues or mistakes in the process. Once the reasons are clear, the Improve step focuses on making things better. Ideas are tested to fix the problems found earlier. The goal is to make real improvements in how well the process works. Finally, the Control step makes sure these improvements stick around. Steps are taken to watch how well things are going and to stop things from going back to how they were. This step often means making clear ways of working, training people, and putting in good ways to watch how things are going.
The Six Sigma DMAIC way is used in many industries because it's good at solving problems and making things better all the time. People who want to learn more about making processes work better can take courses in Six Sigma, like Lean Six Sigma or Six Sigma online courses, where they can get certifications like Six Sigma Green Belt certification.
Understanding Six Sigma DMAIC
Six Sigma DMAIC (Define, Measure, Analyze, Improve, Control) is a structured method for improving processes that is widely used across industries. It involves a series of steps aimed at boosting quality and efficiency by identifying and fixing defects or inefficiencies in processes.
Six Sigma DMAIC is crucial for achieving better operations and reducing variations. It starts with the Define phase, where project goals and customer needs are set. Next is the Measure phase, which involves measuring current process performance using data-driven methods. During the analysis phase, the root causes of problems are pinpointed through statistical analysis. This sets the stage for targeted improvements in the improvement phase. These improvements are then Controlled in the final phase to maintain process improvements over time.
Professionals can progress through different levels of Six Sigma certification: Yellow Belt, Green Belt, Black Belt, and Master Black Belt. Each level represents increasing expertise in implementing DMAIC principles. Understanding Six Sigma DMAIC is essential for professionals who want to enhance organizational efficiency and quality. Mastering DMAIC principles is key to obtaining Six Sigma certifications and becoming skilled in optimizing processes and managing quality effectively.
Challenges in Implementing Six Sigma DMAIC
Six Sigma DMAIC (Define, Measure, Analyze, Improve, Control) is a powerful method used by organizations globally to enhance processes and reduce defects. However, putting DMAIC into practice comes with its challenges. Here are some main issues
1. Resistance to Change: Introducing DMAIC often requires a shift in company culture. Employees might resist new methods or worry about changes to their roles, which can make implementation difficult.
2. Complexity in Data Collection: Successful DMAIC depends heavily on collecting and analyzing accurate data. Gathering relevant data from different departments or systems can take time and may have errors.
3. Skill and Training Gaps: Using DMAIC needs trained professionals who understand statistical tools and problem-solving methods. Companies may struggle to find or train people who know DMAIC well.
4. Sustainability of Improvements: Keeping improvements made through DMAIC can be hard. Without proper monitoring and control, there's a risk of going back to old, inefficient ways over time.
5. Integration with Existing Processes: Making DMAIC work with current company processes and frameworks can be tricky. Companies might face problems when trying to use DMAIC across different departments or in different parts of the world.
Getting past these challenges needs strong leadership, ongoing training, and a promise to DMAIC principles. Overcoming these problems can lead to big improvements in processes and better quality that last throughout the company.
What is Six Sigma DMAIC and how does it work?
1. Define:
-
Six Sigma DMAIC (Define, Measure, Analyze, Improve, Control) is a methodical approach used in Six Sigma projects to boost process efficiency.
-
It starts by clearly defining the problem and setting project goals.
2. Measure:
-
Next, in the Measure phase, data about the process is gathered to establish a starting point.
-
Key metrics and performance indicators are identified to measure the current state.
3. Analyze:
-
During the analysis phase, the collected data is scrutinized to pinpoint the root causes of issues or inefficiencies.
-
Tools like statistical analysis and process mapping are used to identify where problems occur.
4. Improve:
-
The Improve phase focuses on developing and testing solutions to address identified issues.
-
Innovative approaches are tried, and changes are made based on data-guided decisions.
5. Control:
-
Finally, the Control phase ensures that improvements are sustained over time.
-
Control plans are put in place to monitor performance and prevent issues from recurring.
6. Overall Process:
-
Six Sigma DMAIC offers a structured way to solve problems and enhance processes in organizations.
-
It emphasizes using data to make decisions and continually improving to achieve measurable results.
Following the Six Sigma DMAIC methodology helps organizations streamline operations, reduce errors, and improve overall effectiveness, making it a valuable tool in Six Sigma practices.
Exploring the Phases of Six Sigma DMAIC
Six Sigma DMAIC (Define, Measure, Analyze, Improve, Control) is a structured method used by organizations to enhance their processes. Let's break down each phase:
1. Define Phase: This first step clarifies project goals and scope. It outlines what needs improvement and gathers stakeholder requirements, laying the groundwork for the entire Six Sigma project.
2. Measure Phase: After defining the scope, the Measure phase focuses on quantifying current process performance. It identifies key metrics and collects data to establish a starting point. This data-driven approach ensures decisions are based on facts, not assumptions.
3. Analyze Phase: Here, collected data is thoroughly examined. Statistical tools are used to find the root causes of defects or inefficiencies in the process. Pinpointing these causes helps prioritize areas for improvement.
4. Improve Phase: Using insights from the Analyze phase, the Improve phase aims to develop and implement solutions. Creativity is encouraged to find the best fixes that will lead to measurable improvements in process performance.
5. Control Phase: The final phase focuses on maintaining improvements. Control plans are created to standardize the new process and ensure gains are sustained over time. Monitoring systems are put in place to detect any deviations and allow for quick corrections.
Understanding Six Sigma DMAIC empowers organizations to systematically enhance their processes, boost efficiency, and achieve higher quality and customer satisfaction. By following the Define, Measure, Analyze, Improve, and Control approach, organizations can drive continuous improvement and achieve sustainable success. For more detailed insights into Six Sigma DMAIC and its applications, visit icfq for comprehensive resources and tools tailored to support your improvement initiatives.