Six Sigma Techniques for Effective Process Control
Explore Six Sigma techniques for effective process control. Learn how tools like DMAIC, SIPOC, and control charts help reduce defects and enhance operational efficiency.
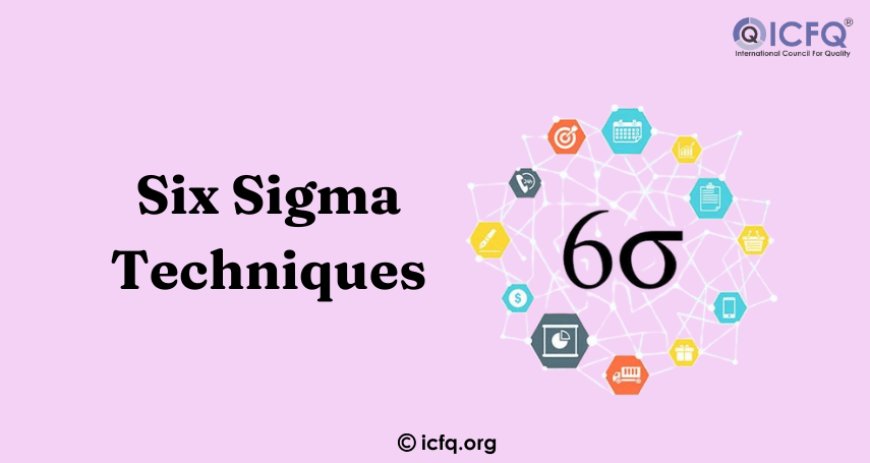
As a Six Sigma practitioner, I have hands-on experience applying various Six Sigma techniques to improve process efficiency and reduce defects across different industries. Using data-driven methods like DMAIC tools such as control charts, I’ve helped organizations identify process inefficiencies, streamline operations, and achieve measurable improvements in quality and customer satisfaction.
What Are Six Sigma Techniques?
Six Sigma techniques are a set of statistical and problem-solving methods designed to improve business processes by identifying and eliminating the causes of defects and inefficiencies. The methodology is based on the idea that any process will have inherent variability, but by understanding and controlling this variability, businesses can achieve significant improvements in quality, cost, and time.
The Importance of Process Control in Quality Management
-
Crucial for Quality Management: Process control ensures that processes operate within defined limits, preventing defects from occurring.
-
Continuous Monitoring: Enables businesses to monitor, adjust, and optimize operations regularly.
-
Prevents Defects: Without proper process control, companies risk producing defective products or services.
-
Risk of Negative Outcomes: Poor process control can lead to customer dissatisfaction, increased costs, and damaged reputations.
-
Role of Six Sigma: Six Sigma techniques provide a structured approach to identifying process inefficiencies and reducing variation.
-
Data-Driven Tools: Tools like statistical analysis and process mapping help businesses gain insights into their operations.
-
Corrective Actions: With Six Sigma, businesses can take timely corrective actions to improve processes and prevent defects.
Key Six Sigma Techniques for Process Improvement
Several key techniques are used in Six Sigma to improve processes and achieve better control over production. These techniques involve data collection, statistical analysis, and continuous monitoring of processes. Let's explore some of the most commonly used Six Sigma techniques:
DMAIC (Define, Measure, Analyze, Improve, Control)
DMAIC is the core methodology of Six Sigma and is used to improve existing processes. It is a structured, five-phase approach that helps organizations identify and solve problems systematically.
-
Define: Identify the problem, define the goals, and understand the project scope.
-
Measure: Collect data to measure the current performance of the process.
-
Analyze: Use statistical tools to analyze the data and identify the root causes of defects or inefficiencies.
-
Improve: Develop and implement solutions to address the root causes and improve the process.
-
Control: Monitor the process after improvements are made to ensure the gains are sustained.
DMAIC is one of the most effective Six Sigma techniques for process control, providing a clear framework for problem-solving and continuous improvement.
SIPOC (Suppliers, Inputs, Processes, Outputs, Customers)
SIPOC is a high-level tool used in Six Sigma to map out the key elements of a process. It helps teams gain a better understanding of how a process works by focusing on the following elements:
-
Suppliers: The sources that provide inputs to the process.
-
Inputs: The materials, information, or resources required for the process.
-
Process: The steps involved in transforming inputs into outputs.
-
Outputs: The final products or services produced by the process.
-
Customers: The end-users or recipients of the process outputs.
Control Charts
-
Purpose: Control charts are used in Six Sigma techniques to monitor the stability of a process over time.
-
Data Tracking: These charts plot process data points to track performance trends and variations.
-
Identifying Variations: Control charts help identify both common cause variation (normal process variation) and special cause variation (due to external factors).
-
Process Stability: By monitoring processes, control charts help ensure that processes remain stable and consistent.
-
Corrective Actions: If the process falls out of control, control charts allow organizations to take corrective actions to address the issue.
-
Quality Assurance: Ensures that products and services consistently meet quality standards by maintaining process control.
Reducing Variability in Processes with Six Sigma Techniques
Variability is the enemy of quality. Whether it's a manufacturing process or service delivery, variability leads to inconsistencies and defects. One of the key goals of Six Sigma techniques is to reduce variability to a minimum, allowing businesses to produce high-quality products and services consistently.
By analyzing process data and identifying the root causes of variation, organizations can implement corrective actions such as refining process steps, improving employee training, or upgrading equipment. Reducing variability results in better quality, lower costs, and enhanced customer satisfaction.
The Role of Data in Six Sigma
Data is at the heart of Six Sigma techniques. Unlike traditional quality control methods, which often rely on subjective judgment, Six Sigma emphasizes the use of data to make decisions. Data allows businesses to understand their processes more clearly, identify areas for improvement, and measure the impact of changes.
Key data-driven tools used in Six Sigma include:
-
Statistical Process Control (SPC): Used to monitor and control a process through real-time data analysis.
-
Pareto Analysis: Helps identify the most significant factors contributing to defects by focusing on the 80/20 rule.
-
Regression Analysis: A statistical technique used to understand relationships between variables and predict outcomes.
Benefits of Implementing Six Sigma Techniques
Implementing Six Sigma techniques offers numerous benefits for organizations looking to improve their processes and control quality:
-
Reduced defects: By minimizing variation and focusing on process improvement, Six Sigma helps businesses reduce defects and produce higher-quality products and services.
-
Cost savings: Improved process efficiency reduces waste and unnecessary costs, resulting in greater profitability.
-
Customer satisfaction: Consistently delivering high-quality products and services enhances customer satisfaction and loyalty.
-
Increased efficiency: streamlined processes and optimized workflows lead to greater operational efficiency.
-
Employee empowerment: Six Sigma encourages employee involvement in process improvement, fostering a culture of continuous improvement.
Six Sigma techniques are vital for effective process control and continuous improvement. Using approaches like DMAIC, SIPOC, and control charts, businesses can eliminate inefficiencies and optimize operations. With data-driven decisions, Six Sigma ensures sustainable improvements. Six Sigma certification at various levels helps professionals lead these efforts to achieve world-class quality and operational excellence.