Define Six Sigma in Simple Terms
Define Six Sigma in Simple Terms: Learn how this data-driven methodology improves business processes, reduces defects, and boosts efficiency for optimal performance.
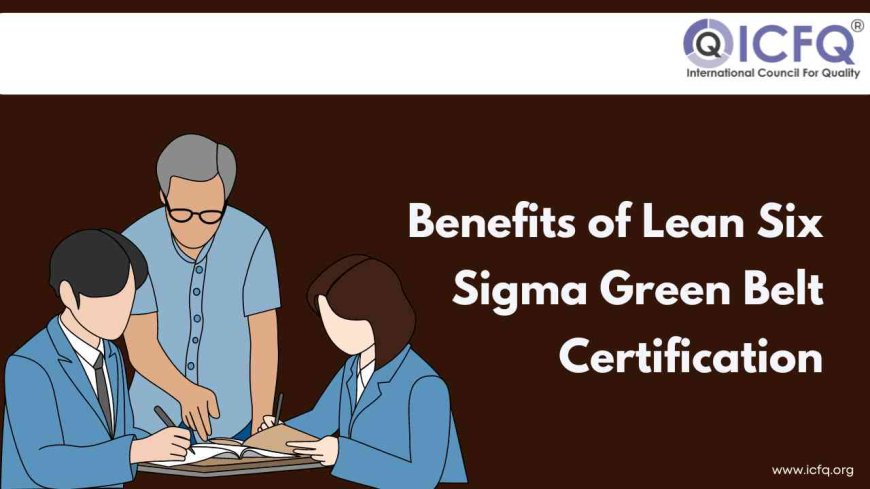
Six Sigma is a method used to improve how a business works by reducing mistakes and inconsistencies. It relies on data and statistical tools to boost quality and efficiency in various processes. If you're interested in learning this approach, Six Sigma Courses provide in-depth training on Six Sigma principles and practices. Whether you’re just starting out or want to deepen your knowledge, there are different levels available, like Six Sigma Green Belt, Six Sigma Black Belt, and Six Sigma Yellow Belt courses. Each level teaches a different amount of detail and is suited for different roles in a company. You can easily find Six Sigma Online Courses on various platforms, allowing you to learn from anywhere at your own pace. For those who want formal recognition, Six Sigma certification and Six Sigma Lean Certification confirm your skills and knowledge. Advanced certifications, such as the Six Sigma Master Black Belt and Six Sigma Professional Certification, are for experts who want to lead Six Sigma projects and drive changes within an organization. To define Six Sigma simply: it’s a method to make business processes more efficient and less error-prone using data and statistical methods.
Understanding Quality Improvement with Six Sigma
Six Sigma is a powerful method for driving quality improvement. It aims to reduce errors and inconsistencies by using data-driven techniques. For those looking to learn more about this method, there are many Six Sigma courses available, including flexible Six Sigma Online Courses. Starting with the Six Sigma Yellow Belt provides a solid foundation. Progressing to Six Sigma Green Belt and Six Sigma Black Belt certifications offers more advanced skills. For those seeking even deeper expertise, Six Sigma Master Black Belt and Six Sigma Lean Certification provide advanced insights into complex problem-solving and process optimization.
Complexity of Quality Management Concepts
A significant challenge is how to define Six Sigma, a well-known quality management method. Six Sigma aims to reduce errors and improve processes using statistical techniques. However, putting it into practice can be tough because it requires precise data collection, analysis, and a good grasp of complex statistical tools. The real challenge is not just adopting Six Sigma principles but also integrating them smoothly into existing processes.
What parts of Six Sigma are most relevant to your business or personal goals, and how do you use or plan to use its principles?
Define Six Sigma
To define Six Sigma, it’s helpful to understand its main parts. "Six Sigma" is a term that measures how well a process is performing. In simple terms, it means that the process is so good that there are very few mistakes or defects. Achieving "Six Sigma" means that your processes are running with very few errors, leading to highquality results.
Principles of Six Sigma
1. DMAIC Framework: Six Sigma uses the DMAIC method—Define, Measure, Analyze, Improve, Control. This stepbystep approach helps in identifying and fixing problems systematically.
2. DataDriven Decisions: Six Sigma relies on collecting and analyzing data to make decisions and improvements.
3. Focus on Customer Satisfaction: The main goal is to improve customer satisfaction by making sure products and services consistently meet their expectations.
Benefits of Six Sigma
Using Six Sigma can lead to better process efficiency, lower costs, and higher quality. It helps create a culture of continuous improvement and precision, which can be very beneficial for any organization.
Simplified Explanation of Six Sigma
Six Sigma is a method to improve business processes and cut down on errors. The goal is to deliver almost perfect products and services by fixing mistakes and inefficiencies. Here’s a straightforward guide to understanding and using Six Sigma:
What Is Six Sigma?
Define Six Sigma as a way to boost quality and efficiency in business. It uses data and statistical tools to find and fix defects in processes, aiming for no more than 3.4 defects per million chances. Here are the five main ideas behind Six Sigma:
-
Customer Focus: Start with understanding what the customer needs and expects. Six Sigma aims to create value from the customer’s viewpoint.
-
DataDriven Decisions: Use accurate data and statistical analysis to find problems, measure performance, and improve processes. Data helps in making smart choices and confirming solutions.
-
Process Improvement: Work on making processes better by cutting waste and reducing variations. Six Sigma techniques streamline workflows and enhance efficiency.
-
Standardization: For consistent results, Six Sigma emphasizes making processes and procedures uniform. This consistency helps maintain improvements over time.
-
Continuous Improvement: Six Sigma is an ongoing effort. It promotes a culture of regular review and improvement to keep striving for excellence.
Key Methods
Six Sigma uses two main methods to improve processes:
1. DMAIC: This stands for Define, Measure, Analyze, Improve, and Control. It’s used to improve existing processes.
Define: Find the problem and set goals.
Measure: Collect data and see current performance.
Analyze: Look at the data to find the root causes of issues.
Improve: Create and apply solutions.
Control: Monitor the process to keep improvements in place.
2. DMADV: This stands for Define, Measure, Analyze, Design, and Verify. It’s used for developing new processes or products.
Define: Set project goals and customer needs.
Measure: Collect data and set benchmarks.
Analyze: Use data to create design options.
Design: Develop and test the new process or product.
Verify: Make sure the design meets customer needs and works as intended.
Tips for Success
1. Engage Leadership: Make sure top management supports Six Sigma. Their involvement helps align the project with business goals and provides needed resources.
2. Train Employees: Provide training on Six Sigma principles and tools. Welltrained employees are more effective in making and maintaining improvements.
3. Use the Right Tools: Apply Six Sigma tools like process mapping and control charts to analyze data and find issues.
4. Foster a Culture of Quality: Create an environment that values quality and constant improvement. Recognize and reward efforts that lead to better processes.
5. Communicate Clearly: Keep communication open throughout the Six Sigma project. Clear communication helps align the team and manage expectations.
By understanding and applying these Six Sigma principles and methods, businesses can greatly improve their processes, reduce defects, and enhance customer satisfaction.