Easy Steps to Start Using Six Sigma Today
Discover easy steps to begin implementing Six Sigma methodology today. Enhance efficiency and quality in your processes effortlessly.
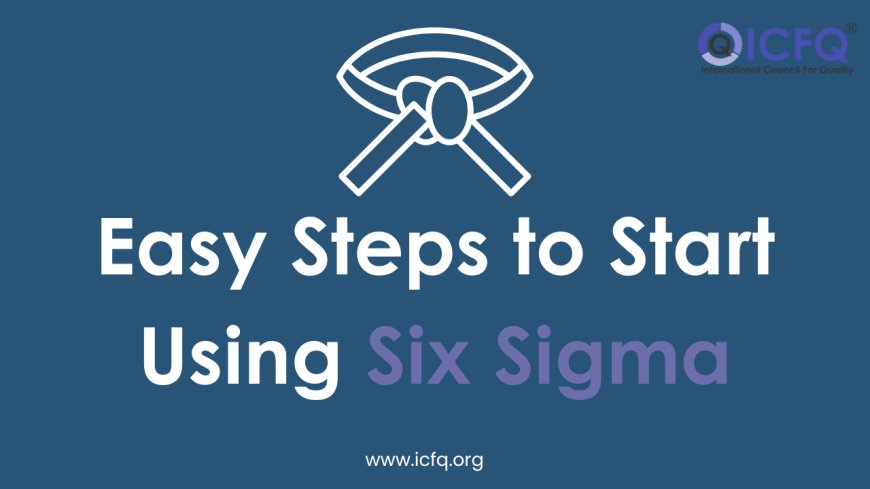
Continuous improvement is the ongoing effort to enhance processes, products, and services within a business. It involves systematically identifying areas for enhancement, making incremental changes, and consistently striving for better outcomes. This approach fosters adaptability and agility, enabling businesses to respond effectively to market shifts and evolving customer needs. By embracing continuous improvement, organizations can optimize efficiency, enhance quality, and ultimately, drive long-term success.
Six Sigma serves as a structured methodology for achieving continuous improvement and process excellence. It emphasizes data-driven decision-making and problem-solving techniques to identify and eliminate defects and variations within processes. Through methods like DMAIC (Define, Measure, Analyze, Improve, and Control), Six Sigma enables organizations to pinpoint the root causes of issues, implement targeted solutions, and monitor performance to sustain improvements over time. By focusing on quality and customer satisfaction, Six Sigma helps businesses enhance competitiveness, reduce costs, and increase operational efficiency.
Understand the Basics of Six Sigma
Six Sigma is all about making things better in a business. It aims to improve quality, reduce mistakes, and keep customers happy. By focusing on these objectives, Six Sigma helps companies deliver products or services that meet or exceed customer expectations consistently.
At the heart of Six Sigma is the DMAIC method: Define, Measure, Analyze, Improve, and Control. It's like a step-by-step guide for making improvements. First, you define what you want to improve and set goals. Then, you measure how things are going right now and identify areas for change. Next, you analyze the data to figure out why things aren't working perfectly. After that, you come up with solutions to fix the problems and make things better. Finally, you put measures in place to make sure things stay on track in the future.
Aligning Six Sigma with what the business wants to achieve and what customers want is important. It means focusing on the right things and making sure efforts are directed where they matter most. By doing this, companies can make the most of Six Sigma and see real improvements in how they operate and serve their customers.
Identifying Opportunities for Six Sigma Projects
To identify processes suitable for Six Sigma projects, conduct a thorough assessment of various operational areas within the organization. Look for processes that exhibit recurring issues, high error rates, or significant variations. Consider input from employees, customer feedback, and historical data to identify potential improvement opportunities accurately.
Criteria for selecting impactful Six Sigma projects
-
Impact: Prioritize projects with the potential to deliver significant improvements in quality, efficiency, or customer satisfaction.
-
Feasibility: Assess the feasibility of projects in terms of available resources, time constraints, and organizational readiness for change.
-
Data availability: Ensure that relevant data is readily accessible for analysis and measurement to support the project's objectives.
-
Strategic alignment: Select projects that align closely with organizational goals and strategic priorities to ensure maximum impact and relevance.
Tips for involving stakeholders and gaining buy-in
-
Engage stakeholders early: Involve key stakeholders from different departments and levels of the organization to ensure diverse perspectives and support.
-
Communicate benefits: Communicate the potential benefits of Six Sigma initiatives, such as cost savings, improved quality, or enhanced customer satisfaction.
-
Address concerns: Listen to stakeholders' concerns and address them transparently to build trust and foster support for the initiative.
-
Demonstrate success: Start with small-scale projects to demonstrate the effectiveness of Six Sigma methodologies and build credibility for broader implementation. Regularly communicate progress and celebrate successes to maintain momentum and enthusiasm among stakeholders.
Six Sigma Roles & Recruitment
In Six Sigma projects, various roles play crucial functions:
-
Champions: These are senior leaders who provide strategic direction and ensure alignment of Six Sigma projects with organizational goals. They play a key role in securing resources, prioritizing initiatives, and driving organizational change.
-
Black Belts: full-time project leaders responsible for leading Six Sigma projects from start to finish. They possess advanced analytical and problem-solving skills and are trained in Six Sigma methodologies. Black Belt leads project teams, conducts data analysis, and implements improvement strategies to achieve project goals.
-
Green Belts: Part-time team members who support Black Belts in executing Six Sigma projects. They have a basic understanding of Six Sigma principles and tools and are responsible for data collection, analysis, and implementation of improvement initiatives within their respective areas.
-
Team Members: These individuals come from different departments or functions within the organization and contribute subject matter expertise and insights to the project teams. They actively participate in problem-solving activities, provide input on process improvements, and help implement changes.
Recruiting or training team members for these roles involves identifying individuals with relevant skills and providing the necessary training. Look for individuals with strong analytical abilities, problem-solving skills, and a commitment to continuous improvement. Training programs or certifications, such as Black Belt or Green Belt certification courses, can help develop the skills and knowledge required for specific roles in Six Sigma projects.
Leadership support and commitment are crucial for the success of Six Sigma initiatives. Senior leaders must actively champion Six Sigma efforts, allocate resources, and remove barriers to implementation. Their visible support and commitment create a culture of accountability and drive organizational buy-in, ensuring the success and sustainability of Six Sigma projects.
Training and Education
By investing in training and education, organizations can empower their teams to effectively apply Six Sigma methodologies, drive process improvements, and achieve tangible results. Ongoing skill development ensures that teams remain equipped to address evolving challenges and continuously drive organizational excellence. Training and education are essential components of Six Sigma implementation:
-
Six Sigma offers various training programs and certifications to equip individuals with the necessary skills and knowledge. These programs range from basic to advanced levels and cover topics such as DMAIC methodology, statistical analysis, and process improvement techniques.
-
For team members new to Six Sigma, starting with basic training, such as Green Belt certification, is recommended. Green Belt training provides a solid foundation in Six Sigma principles and methodologies, equipping individuals to contribute effectively to project teams and support improvement initiatives.
-
Ongoing education and skill development are crucial for maintaining proficiency in Six Sigma principles and tools. Continuous learning ensures that team members stay updated on best practices, new techniques, and emerging trends in process improvement. It also enables individuals to enhance their problem-solving abilities and drive sustainable improvements within their organizations.
Selecting Tools and Techniques
In Six Sigma projects, various tools and techniques are utilized to analyze data, identify root causes, and implement solutions:
-
Process maps: are visual representations of a process flow, highlighting steps, inputs, outputs, and interactions. They help teams understand process complexity and identify areas for improvement.
-
Cause-and-effect diagrams (Fishbone diagrams): used to identify potential causes of a problem or effect. They organized brainstormed ideas into categories, such as people, methods, materials, machines, and environment.
-
Statistical analysis: utilizes statistical methods to analyze data and identify patterns, trends, and relationships. Techniques include hypothesis testing, regression analysis, and control charts.
When picking tools for a Six Sigma project, match them with the problem you're dealing with. Think about what data you have and make sure the tools match your goals. Start with a few basic tools that help with the main issues. You can add more tools to your collection as you get more experienced and face different problems. This way, you'll get better at solving problems and making things run smoothly, which leads to success in your projects.
Beginning of First Six Sigma Project
Case studies can provide valuable insights into how the DMAIC methodology is applied in practice. By following these steps and incorporating tips for goal setting, data gathering, root cause analysis, solution implementation, and sustainability, teams can effectively initiate and execute Six Sigma projects to drive process improvements and achieve successful outcomes.
-
Define Project Goals: Clearly outline the objectives and desired outcomes of the project to provide a clear direction for the team.
-
Gather Data: Collect relevant data related to the process or problem being addressed. This may include process metrics, customer feedback, or performance indicators.
-
Analyze Root Causes: Use data analysis techniques to identify the underlying factors contributing to the problem or process inefficiencies.
-
Implement Solutions: Develop and implement targeted solutions based on the root causes identified. Ensure that solutions are feasible and aligned with project goals.
-
Sustain Improvements: Put measures in place to ensure that improvements are sustained over time. This may involve implementing control measures, training team members, or updating procedures
Monitoring and Sustaining Improvement
After making improvements with Six Sigma, it's crucial to keep an eye on how well your processes are doing. This helps ensure that the changes you've made stick and continue to benefit the organization.
-
Using Control Charts: Control charts are handy tools for keeping track of process performance over time. They help identify any changes or trends that might indicate problems creeping back in.
-
Establishing a Culture of Continuous Improvement: Encourage everyone in the organization to always be looking for ways to do things better. Make it clear that improving processes isn't a one-time thing but an ongoing effort.
-
Fostering Accountability: Hold teams accountable for maintaining the improvements made through Six Sigma projects. Regular reviews and discussions can help keep everyone focused on sustaining the gains achieved.
By regularly monitoring process performance and using tools like control charts, organizations can ensure that improvements made through Six Sigma initiatives remain effective. Moreover, fostering a culture of continuous improvement and accountability reinforces the importance of ongoing efforts to maintain and enhance operational excellence.
starting your Six Sigma journey is achievable with a few key steps. Begin by identifying areas in your organization that could benefit from improvement and selecting a small-scale project to tackle first. Use Six Sigma methods like DMAIC and choose the right tools for your project. Keep an eye on progress and celebrate achievements. Taking action on Six Sigma today can lead to positive changes and lasting improvements in your organization. Feel free to explore more resources or get help from professionals as you move towards operational excellence.