Improve Quality Management with Six Sigma Strategies
Discover how Six Sigma strategies can improve quality management. Reduce errors and optimize performance.
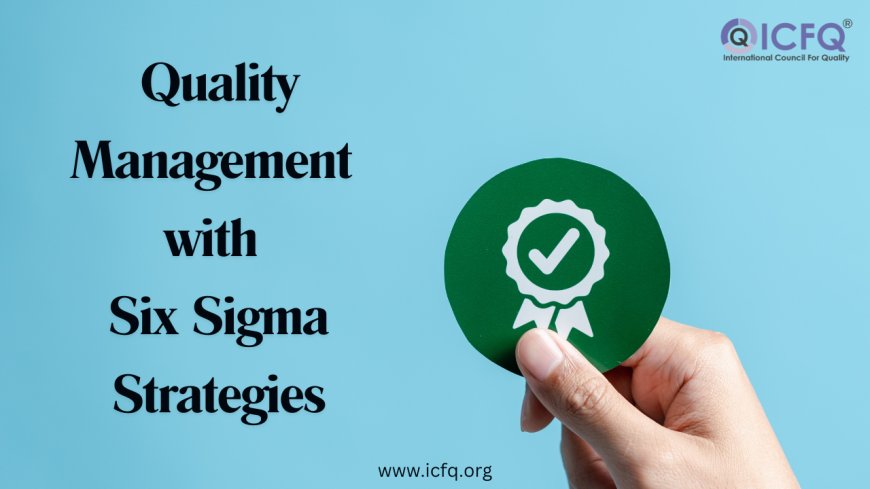
Six Sigma is a method used in quality management that focuses on reducing mistakes and improving processes through detailed analysis. It uses specific steps known as DMAIC: Define, Measure, Analyze, Improve, and Control, to find and fix errors in business operations. This method is helpful in many industries because it aims to make processes efficient and reduce defects to a very low level, enhancing the quality of products and services.
When businesses apply Six Sigma strategies, they can see significant improvements like lower costs and better customer satisfaction. Six Sigma helps identify and cut down on unnecessary steps or waste in processes, making operations smoother and more cost-effective. Furthermore, by consistently monitoring and improving quality, products and services become more reliable, meeting customer expectations better. This makes the company more competitive and able to sustain its market position by delivering high-quality offerings.
Six Sigma Fundamentals
Six Sigma is a detailed methodology designed to improve business processes by minimizing errors and variability in manufacturing and service-related industries. Its core objectives are to enhance efficiency, reduce waste and costs, increase customer satisfaction, and boost profitability by refining operations. The methodology is grounded in several certification levels, each denoting a proficiency degree in the Six Sigma approach: Yellow Belt for beginners, Green Belt for intermediate project participants, Black Belt for project leaders, and Master Black Belt for organizational strategy and mentoring roles.
At the heart of Six Sigma is the process begins by defining the project goals and identifying customer requirements. It then measures the current processes to establish baselines for improvement. The Analyze phase digs deeper into the data to find the root causes of defects. During the improvement phase, solutions are developed and implemented to rectify these defects. Finally, the Control phase ensures that these improvements are sustained over time, embedding them into the organization’s daily practices. This systematic approach is pivotal in driving significant quality improvements in any organization.
Key Tools in Six Sigma for Quality Management
Six Sigma employs a variety of tools and techniques to enhance quality management in organizations. These tools are used throughout the DMAIC (Define, Measure, Analyze, Improve, Control) process to identify, analyze, and solve quality problems. Here are some key Six Sigma tools commonly used for quality management:
1. Fishbone Diagram (Cause and Effect Diagram)
This tool helps identify the root causes of a problem. It visually organizes potential causes into categories, making it easier to brainstorm and explore relationships between factors causing quality issues.
2. SIPOC Diagram (Suppliers, Inputs, Processes, Outputs, Customers)
SIPOC diagrams are used in the Define phase to give a high-level overview of a process. This tool outlines the suppliers, inputs, process steps, outputs, and customers, providing a clear snapshot of all relevant aspects of the process.
3. Control Charts
Control charts are used to monitor process stability and performance over time. They help determine whether a process is under control or if there are variations that need to be addressed.
4. Pareto Chart
This tool, based on the Pareto principle, identifies and prioritizes problems or defects that have the greatest overall impact. It helps focus efforts on the issues that will provide the most significant benefits.
5. Histogram
A histogram is a type of bar chart that represents the distribution of numerical data. It is used to analyze the frequency of data points within certain ranges and can help visualize the variation in a process.
6. Scatter Diagram
Scatter diagrams are used to analyze and identify potential relationships between two variables. This can help determine if changes in one variable might be causing changes in another.
7. Failure Modes and Effects Analysis (FMEA)
FMEA is an analytical method used to ensure potential problems are anticipated, identified, and mitigated in a process. It examines possible failures and their impacts to prioritize which ones need corrective actions first.
8. 5 Whys
This simple but powerful tool involves asking "Why?" five times to drill down to the root cause of a problem. It is often used in conjunction with the Fishbone Diagram to thoroughly explore and resolve underlying issues.
These tools are integral to the Six Sigma methodology, supporting the objective of reducing variability in processes and improving quality to near perfection. Each tool has a specific function and is chosen based on the particular phase of the DMAIC process and the nature of the problem being addressed.
Role of Data in Six Sigma
Data is essential in Six Sigma because it helps make informed decisions throughout the process. In Six Sigma, data is collected at every step to accurately identify problems, measure their impact, and analyze which processes aren't working well. This data-driven approach ensures that solutions are based on solid evidence rather than guesses. By thoroughly analyzing data, Six Sigma practitioners can pinpoint where processes can be improved, see how well changes are working, and make sure these improvements lead to real results. This makes data the backbone of the Six Sigma process, guiding efforts to enhance quality and efficiency.
Measuring the Impact of Six Sigma on Quality Management
To effectively measure the impact of Six Sigma initiatives on quality management, organizations can follow these steps:
-
Performance Indicators: Identify key performance indicators (KPIs) relevant to the goals of Six Sigma projects, such as defect rates, process cycle times, customer satisfaction levels, and cost savings.
-
Pre- and Post-Implementation Analysis: Compare the baseline data collected before the implementation of Six Sigma to the data obtained after changes have been made. This will directly show the improvements in processes and quality.
-
Statistical Analysis: Utilize statistical tools integral to Six Sigma, like control charts and regression analysis, to measure changes and ensure they are statistically significant.
-
Return on Investment (ROI): Calculate the ROI from Six Sigma initiatives by comparing the cost of implementing Six Sigma (including training, time, and resources) against the financial benefits gained from the improvements.
Strategies for Sustaining Improvements Over the Long Term
Maintaining the gains from Six Sigma over the long term requires several key strategies:
-
Standardization of Processes: Develop and implement standard operating procedures (SOPs) for the improved processes. Standardization helps maintain consistency and quality even as personnel or other elements change.
-
Regular Audits and Reviews: Schedule regular audits and process reviews to ensure adherence to SOPs and to identify areas where processes may be drifting from the standard.
-
Ongoing Training: Continuously train new and existing employees on Six Sigma methodologies and the specific processes they operate within. This ensures that all team members are competent and fully aware of their roles in maintaining quality.
-
Adaptation to Change: Be prepared to adjust processes in response to new challenges, technologies, or market conditions. Flexibility is key to sustaining long-term improvement.
Continuous Improvement: The Role of Leadership and Team Engagement
Leadership and team engagement are critical in driving and sustaining continuous improvement:
-
Leadership Commitment: Leaders must be fully committed to a culture of continuous improvement. They should set clear goals, allocate resources effectively, and lead by example to drive the continuous improvement agenda.
-
Empowering Teams: Empower employees by involving them in decision-making processes, recognizing their contributions, and providing them with the tools and authority to make improvements.
-
Communication: Maintain open lines of communication across all levels of the organization. Regular updates on progress, challenges, and successes help keep everyone aligned and motivated.
-
Incentivization: Recognize and reward teams and individuals who contribute to improvements. This can boost morale and encourage ongoing participation in Six Sigma initiatives.
Adopting Six Sigma strategies can greatly improve how well a business runs by making processes more efficient, reducing costs, and increasing customer satisfaction. For organizations looking to improve, getting started with Six Sigma certification or implementing it on a small scale can be good first steps. Six Sigma can transform business operations by creating a culture that constantly seeks to improve. This approach helps businesses achieve their goals more effectively and maintain high-quality standards, making it a worthwhile strategy for any company aiming to enhance its processes.