Understanding Lean Six Sigma Principles
Understand Lean Six Sigma principles that blend waste reduction and defect elimination to streamline processes, improve quality, and encourage continuous improvement.
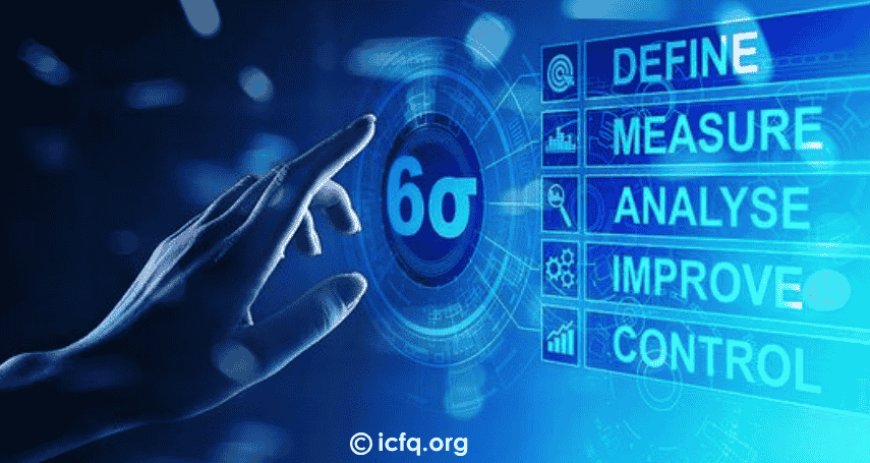
In my experience, the principles of Lean Six Sigma have had a transformative impact on organizations aiming to enhance their performance. Whether it's reducing waste, improving process efficiency, or elevating product quality, I've personally witnessed how Lean Six Sigma offers a structured, data-driven approach that truly improves operations.
Lean Six Sigma combines two powerful methodologies: Lean, which focuses on cutting down waste, and Six Sigma, which targets minimizing variation and defects. From my work, I've learned that when these two methodologies are combined, they create a comprehensive framework for continuous improvement. This framework drives greater efficiency, consistency, and long-term success across various processes and operations.
What is Lean Six Sigma?
Lean Six Sigma is a method that helps businesses improve their processes by making them more efficient and reducing mistakes or waste. It combines two approaches: Lean, which focuses on getting rid of unnecessary steps and speeding things up, and Six Sigma, which focuses on reducing errors and making sure things are done right every time.
Together, these approaches work to create a culture where businesses are always looking for ways to improve. They use data and tools to streamline operations, improve quality, and better meet the needs of customers. The Lean Six Sigma principles provide guidelines that help businesses use these methods to reduce waste, fix problems, and achieve better results.
The Core Lean Six Sigma Principles
There are five key principles of Lean Six Sigma that organizations must embrace to successfully implement this methodology:
1. Define
The first principle in Lean Six Sigma principles is defining the problem or opportunity for improvement. The define phase is crucial because it sets the foundation for the entire project. During this phase, teams must clearly identify the goals, scope, and objectives of the project. This is also where the team defines the voice of the customer (VOC) and what they expect from the process improvements.
Businesses usually use brainstorming sessions, value stream mapping, and process mapping to define the problem properly. Once they understand the problem fully, they can develop a clear strategy to address it.
2. Measure
Once the problem is defined, the next Lean Six Sigma principle is to measure the current state of the process. The Measure phase focuses on collecting data that reflects the performance of the existing process. This data helps identify areas where inefficiencies, delays, or defects occur.
By gathering accurate data, organizations can assess the current performance and determine the root causes of the issues. Common tools used during the Measure phase include control charts, histograms, and Pareto analysis. These tools provide insights into the areas that need improvement.
3. Analyze
The analyze phase is where organizations take the data collected during the measure phase and perform a detailed analysis. In this phase, teams identify the underlying causes of process inefficiencies and defects. The goal is to pinpoint the root causes that contribute to variability and poor performance.
By analyzing the data, businesses can uncover patterns, correlations, and trends that reveal the factors affecting process quality. Common analytical tools used in this phase include regression analysis, failure mode and effect analysis (FMEA), and fishbone diagrams (Ishikawa diagrams). This step is critical to ensuring that improvements target the most significant issues.
4. Improve
After identifying the root causes, the next principle of Lean Six Sigma is improving the process. In the Improve phase, teams design and implement solutions that address the identified problems. This phase focuses on making changes that will streamline the process, reduce waste, and enhance quality.
The improvements can take many forms, including process redesign, automation, or employee training. Organizations also use tools like brainstorming, design of experiments (DOE), and simulation to test potential solutions before implementing them. The objective is to create a more efficient and effective process that delivers consistent results.
5. Control
The final principle in Lean Six Sigma principles is to control the new process and ensure that the improvements are sustained over time. The control phase involves monitoring the process to ensure that the gains achieved during the improvement phase are maintained. It’s also important to standardize the new process to prevent any backslide into old habits.
In this phase, organizations often use control charts, process audits, and visual management techniques to monitor the performance of the process. By regularly reviewing the process, businesses can identify new opportunities for improvement and ensure long-term success.
The Benefits of Lean Six Sigma Principles
By adopting the Lean Six Sigma principles, organizations can reap numerous benefits, including:
-
Reduced Waste: One of the primary goals of Lean is to eliminate waste, which can significantly reduce operational costs.
-
Improved Quality: By focusing on reducing defects and variability, organizations can improve the quality of their products and services.
-
Faster Processes: Lean techniques help streamline processes, resulting in shorter cycle times and quicker delivery to customers.
-
Increased customer satisfaction: With improved quality and faster delivery, customers are more likely to be satisfied with the products or services they receive.
-
Data-Driven Decision Making: Lean Six Sigma relies on data to drive decisions, ensuring that improvements are based on objective evidence rather than assumptions.
These benefits make Lean Six Sigma an essential methodology for businesses looking to stay competitive in their respective industries.
How to Implement Lean Six Sigma Principles in Your Organization
Implementing the Lean Six Sigma principles within an organization requires a structured approach. Here’s a general outline of how businesses can implement Lean Six Sigma:
-
Training and Certification: Start by training employees in Lean Six Sigma concepts and certifying them at the appropriate levels (Yellow Belt, Green Belt, Black Belt).
-
Leadership Buy-In: Ensure that leaders within the organization are committed to the Lean Six Sigma methodology and are ready to provide the necessary resources and support.
-
Project Selection: Choose a project that aligns with organizational goals and has a significant impact on process improvement.
-
Follow the DMAIC Process: Use the Define, Measure, Analyze, Improve, and Control (DMAIC) framework to guide the project and ensure that each phase is completed effectively.
-
Sustain and Scale: Once the project is completed, ensure that the improvements are sustained. Expand the Lean Six Sigma approach to other areas of the organization to drive continuous improvement.
Lean Six Sigma helps organizations improve processes, reduce waste, and boost quality. For successful implementation, proper training and certification are key. ICFQ offers recognized Six Sigma certifications (Yellow Belt, Green Belt, Black Belt, and Master Black Belt) to equip you with the skills needed to drive improvement and achieve success.