Six Sigma Tips for Quality Improvements
Discover valuable Six Sigma tips for enhancing quality and efficiency. Learn how to implement Six Sigma methodologies for continuous improvement.
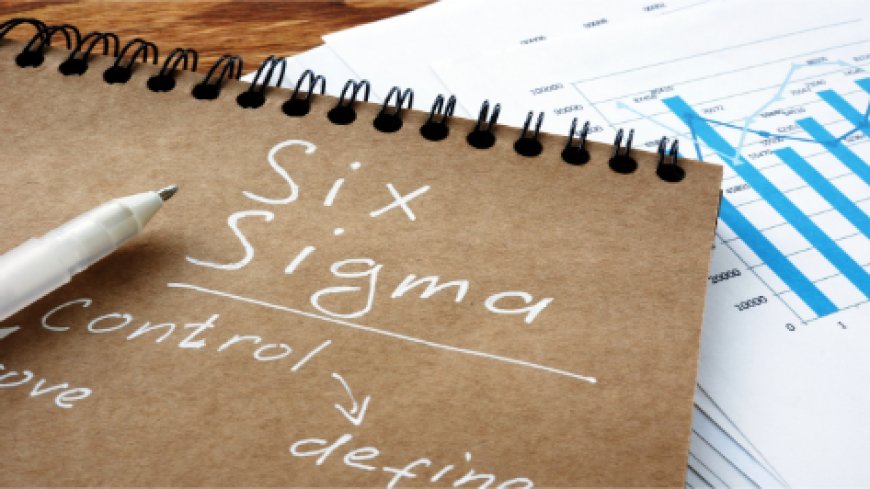
Six Sigma is like a toolkit for businesses to make things better. It helps them find and fix problems in how they work, making sure they deliver top-notch quality and efficiency. By following a step-by-step approach, companies can figure out what's not working, make changes, and keep getting better over time. This is super important because it helps businesses stand out, keep customers happy, and stay ahead of the competition. Plus, it gets everyone in the team involved, making work more satisfying and bringing out new ideas for success.
Implementing Six Sigma is super important for companies to keep up in today's fast-changing market. By always delivering great quality, businesses can make customers happy and keep them coming back. Plus, using data to make decisions means they're making smart moves, not just guessing. And when everyone on the team gets involved, it makes work more exciting and brings out cool ideas to help the company grow. So, Six Sigma isn't just about fixing problems—it's about making sure everyone's part of the success story.
What are the Six Sigma Principles and their importance?
Six Sigma principles are all about improving how a company works to make things better for customers and the business itself. One key part of Six Sigma is the DMAIC methodology, which stands for Define, Measure, Analyze, Improve, and Control. This method helps companies identify problems, measure them, figure out why they're happening, make changes to fix them, and then make sure those fixes stick.
Customer focus and process optimization are also critical in Six Sigma. Customer focus is keeping the needs and wants of the customer in mind at all times and ensuring that the business meets those needs. Finding methods to improve workflow efficiency and effectiveness is known as process optimization. Organizations may ensure customer satisfaction through customer-centric design and process optimization while reducing costs and waste. This increases business success and maintains client satisfaction.
Selecting the Right Projects
-
Criteria for Identifying Projects Suitable for Six Sigma: Pick projects that matter to the company and can make a big difference. Look for ones that line up with what the company wants to achieve and tackle important problems.
-
Importance of Aligning Projects with Organizational Goals: Make sure Six Sigma projects help the company reach its overall goals. When projects fit with what the company aims to do, they become more meaningful and help move the company forward.
-
Tips for Prioritizing Projects Based on Potential Impact: Choose projects that can make the most significant improvements. Think about how much each project can help and how doable it is. Focus on the ones that offer the biggest benefits and can be done efficiently with the resources available. This way, efforts go into projects that will make a difference for the company.
Key Quality Improvement Techniques
To improve quality, businesses use various techniques to find and fix problems. Root cause analysis methods help identify the main reasons behind issues, so they can be addressed effectively. Process mapping and value stream mapping are like drawing a roadmap of how things get done, helping to see where things might be going wrong or could be done better.
Statistical tools like Pareto analysis and control charts help make sense of the data. Pareto analysis helps prioritize what problems to tackle first by showing which ones have the biggest impact. Control charts help monitor processes over time, making sure they stay on track and consistent.
Using these techniques helps companies understand their problems, find solutions, and keep track of progress. It's like having a toolbox full of different tools to fix different things, making sure everything runs smoothly and efficiently.
What are some important tools and techniques for quality control?
There are some essential tools and techniques for monitoring and controlling quality, including:
A. Process Mapping
This involves visually representing the steps of a process to identify inefficiencies, bottlenecks, and areas for improvement. It helps teams understand the flow of work and streamline processes for better performance.
B. Pareto Analysis
This technique prioritizes problems by identifying the most significant factors contributing to them. It helps focus efforts on resolving the most critical issues first, leading to more impactful improvements.
C. Statistical Process Control (SPC)
SPC uses statistical methods to monitor and control processes, ensuring they remain within predefined limits. By tracking variations in data over time, SPC helps identify trends and deviations early on, allowing for timely interventions to maintain quality.
D. Failure Mode and Effects Analysis (FMEA)
FMEA anticipates potential failures in a process or product and assesses their potential impact. It helps proactively identify and address risks before they occur, minimizing the likelihood of defects and ensuring higher-quality outcomes.
E. Design of Experiments (DOE)
DOE systematically explores the relationship between inputs and outputs in a process to optimize performance. By testing various factors and their interactions, DOE helps identify the most effective settings for achieving desired outcomes efficiently.
Tips for Implementing Six Sigma
For Six Sigma to succeed, top management must fully support and commit to the initiative. They should actively promote the program, provide necessary resources, and remove obstacles. Team members need proper training and certification to implement Six Sigma effectively. This ensures everyone understands their roles. Setting achievable goals and metrics is crucial. Clear goals keep teams motivated and focused. Goals should be specific, measurable, attainable, relevant, and time-bound (SMART), allowing progress tracking and adjustments as needed.
Monitoring and Controlling Quality
Monitoring and controlling processes are crucial for improving the quality of any task. Without keeping a close eye on things, standards can slip and progress can be lost. By regularly checking processes, teams can catch any deviations from the set standards early on and fix them quickly to maintain quality.
-
Establishing Clear Rules: Clearly define what constitutes good performance, including specific metrics, targets, and expectations. These rules should be easily understandable by everyone involved.
-
Implementing checks and balances: Regularly scheduled audits, performance reviews, and feedback sessions are essential to ensure that processes are being followed correctly and that any deviations from the established standards are promptly addressed.
-
Utilizing Automated Systems and Standardized Procedures: Automation can help maintain consistency and reduce the chance of human error. Standardized procedures ensure that tasks are performed consistently across different teams or departments, making it easier to monitor and control quality.
Leadership and Cultural Aspects
Leadership plays a pivotal role in Six Sigma implementation by setting the vision, providing resources, and demonstrating commitment. Leaders need to actively champion the initiative, align it with organizational goals, and empower teams to make data-driven decisions. Their involvement fosters accountability and motivates employees to embrace change.
Creating a culture of continuous improvement involves fostering an environment where learning and innovation thrive. This requires promoting open communication, encouraging feedback, and recognizing improvement efforts. Employees should feel empowered to suggest and implement changes, knowing their contributions are valued. By embedding the mindset of continuous improvement into the fabric of the organization, it becomes ingrained in daily operations.
Employee training and engagement are essential to Six Sigma's success. Training programs should equip employees with the necessary skills and knowledge to effectively participate in improvement projects. Engagement involves involving employees in problem-solving, soliciting their input, and recognizing their contributions. When employees understand the importance of Six Sigma and feel invested in its success, they are more likely to actively participate and contribute to quality improvements.
the discussed tips offer valuable insights for enhancing quality through Six Sigma. Emphasizing leadership support, team training, and clear goal-setting are essential for success. Continuous improvement remains a central theme, fostering ongoing enhancements in processes and outcomes. Encouraging further exploration and implementation of Six Sigma principles can lead to tangible improvements in efficiency and customer satisfaction. By integrating these strategies, organizations can advance their quality initiatives and achieve sustainable success in today's competitive landscape.