Overcoming Common Challenges in Six Sigma Implementation
Overcoming common Six Sigma challenges involves securing leadership support, fostering a data-driven culture, ensuring proper training, and addressing resistance to change effectively.
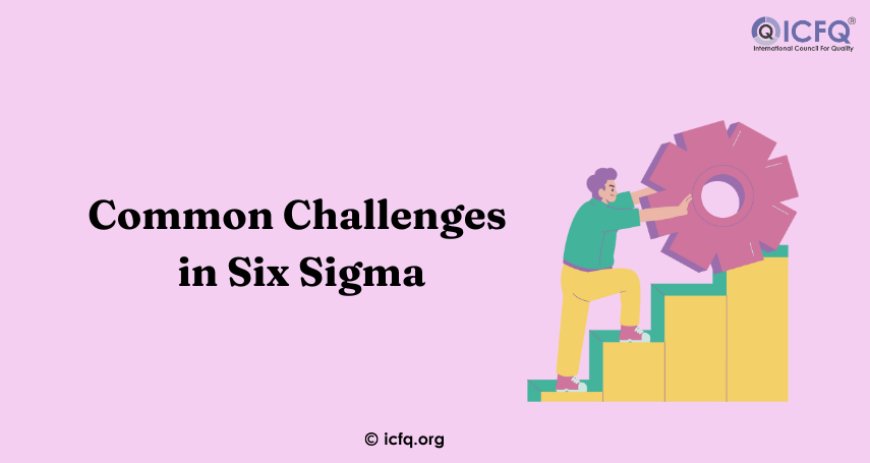
Having spent over 20 years in the Six Sigma field, I’ve seen organizations of all sizes and industries struggle with the implementation of this powerful methodology. Six Sigma, with its focus on reducing defects, improving process efficiency, and enhancing product quality, offers immense benefits. However, its success depends on the effective application of its principles. Over my career, I’ve observed the common obstacles companies face and developed strategies to address them through training and understanding among employees.
Lack of Proper Training and Knowledge
One of the most common barriers to successful Six Sigma implementation is insufficient training. Six Sigma relies heavily on statistical analysis and data-driven decision-making, which can be overwhelming for employees without proper knowledge.
Challenges:
-
Employees struggle with understanding the statistical tools and techniques.
-
insufficient training leads to misapplication of Lean Six Sigma principles.
Solution:
-
Invest in comprehensive training programs for all levels: Yellow Belt, Green Belt, and Black Belt certifications.
-
Encourage continuous learning by offering mentorship from experienced Six Sigma practitioners.
-
Ensure that teams have access to resources and support as they apply Six Sigma methods.
Resistance to Change
As with any change initiative, introducing Six Sigma in an organization often meets with resistance. Employees accustomed to existing processes may be reluctant to adopt new methods, especially if they do not fully understand the benefits of Six Sigma.
Challenges:
-
Employees feel uncertain about the changes and are unwilling to embrace the new methodology.
-
Lack of trust in the effectiveness of Six Sigma.
Solution:
-
Communicate the benefits of Six Sigma clearly to all employees, highlighting how it will improve efficiency and reduce defects.
-
Involve employees early in the process, demonstrating quick wins that show tangible results.
-
Provide support and encouragement, showing that their concerns are being addressed.
Insufficient Management Support
For Six Sigma to succeed, it needs strong support from top management. Without the commitment of senior leaders, it can be difficult to secure the necessary resources, time, and focus needed for successful implementation.
Challenges:
-
Insufficient leadership commitment results in a lack of resources for Six Sigma projects.
-
Lack of visibility and attention from senior management leads to stalled projects.
Solution:
-
Gain commitment from senior leaders before beginning the Six Sigma journey. Management should actively participate in training and champion Six Sigma efforts.
-
Allocate the necessary resources and time for the team to execute Six Sigma projects successfully.
-
Continuously monitor the progress of Six Sigma initiatives and adjust strategies as needed.
Defining Clear Objectives and Metrics
A common pitfall during Six Sigma implementation is the failure to set clear goals and measurable metrics. Without a clear understanding of what success looks like, it’s difficult to track progress and make necessary adjustments.
Challenges:
-
Teams may lack clarity on what they are trying to achieve with Six Sigma.
-
Failure to measure success can result in missed opportunities for improvement.
Solution:
-
Set SMART (Specific, Measurable, Achievable, Relevant, Time-bound) goals for each Six Sigma project.
-
Use key performance indicators (KPIs) to track progress, such as defect rates, process efficiency, and customer satisfaction.
-
Regularly review the results to ensure that objectives are being met and adjust strategies as necessary.
Insufficient Resources and Tools
Six Sigma requires specific tools and resources to analyze data and optimize processes. In many cases, businesses face challenges in providing their teams with the right resources to carry out Six Sigma projects effectively.
Challenges:
-
Lack of advanced data analysis software and statistical tools.
-
Limited access to skilled professionals and resources necessary for project execution.
Solution:
-
Invest in software that supports Six Sigma methodologies, such as data analysis tools and process mapping software.
-
Ensure that teams are equipped with the right tools to collect and analyze data accurately.
-
Allocate enough time and personnel to support the full implementation process.
Overcomplicating the Process
Another challenge is the tendency to overcomplicate Six Sigma initiatives. Organizations sometimes try to apply lean Six Sigma principles to every aspect of the business, leading to confusion and an overly complex implementation process.
Challenges:
-
Teams may become overwhelmed by trying to tackle too many processes at once.
-
Overcomplicating solutions can delay progress and reduce the effectiveness of the Six Sigma approach.
Solution:
-
Start with simple, well-defined projects that can show quick results and help build confidence in Six Sigma.
-
Avoid overcomplicating the process by focusing on practical solutions that address specific issues.
-
Expand the use of Six Sigma methodology gradually as the organization gains experience.
Maintaining Continuous Improvement Culture
Six Sigma is not a one-time effort but rather an ongoing commitment to continuous improvement. After initial success, many organizations struggle to maintain the momentum needed for long-term impact.
Challenges:
-
Lack of continued focus on Six Sigma leads to stagnation.
-
Employees and management may lose interest over time.
Solution:
-
Establish a culture of continuous improvement by integrating Six Sigma into daily business practices.
-
Regularly review processes and set new objectives for improvement.
-
Celebrate successes and highlight the value Six Sigma has added to the organization, motivating staff to keep the momentum going.
Successfully implementing Six Sigma requires overcoming challenges like insufficient training, resistance to change, and lack of resources. By addressing these issues through clear goals, continuous support, and a focus on gradual improvement, organizations can achieve lasting results.